The Power of Fleet Automation: Digitally Transforming Your Fleet to Enhance Operations
By Mark Thomas, Ridecell
The pandemic has hastened transformation efforts for companies around the globe—and this is especially true for fleet-based businesses who rely on drivers and vehicles for daily operations. Implementing and launching new digital technologies goes a long way toward improving business operations, helping fleets meet changing market and customer demands and boosting their competitive advantage.
Many fleets have already invested millions in management systems that generate insights. Connected technology solutions such as telematics, dashcams, and ELDs help you manage your fleet more efficiently and make more informed operational choices. The prolific data streams coming from inventory management, supply chain, ERP, security or CRM solutions work in tandem with these fleet systems.
But these systems are there to identify issues, not fix them. And as companies increase the scale and complexity of their fleets, next-level efficiencies must come from true integration and automation. To collect data and insights about your fleet is incredibly beneficial, but to fully automate the appropriate response and solution is the next horizon.
The power of fleet automation can help you tackle the operational “new normal” in three big ways: improving efficiency, enhancing safety and security for drivers, vehicles and their cargo, and keeping vehicles roadworthy.
THE BATTLE FOR THE LAST MILE
It seems the world has entered a new battle—the battle for the last mile. The ecommerce market has seen a tremendous boost in the wake of the global pandemic, putting additional stress on delivery fleets with increasing pick-ups and returns. Historically, year-over-year growth has hovered around 11% for the last decade, but in 2020 it suddenly grew 11% in just 10 weeks.1
The world has also become even more instant in the wake of this expanding market. Only a few years ago, the standard delivery expectation was seven days. Today, consumers expect immediate service and ultrafast deliveries—those expectations will only continue to grow, and delivery windows will continue to shrink.
The reverse is just as important. It’s estimated that retail returns alone made up $761 billion worth of products in 2021.2 Fast returns are a convenience that customers have grown accustomed to, and as online sales continue to increase, so too will return volume. Nearly every industry is experiencing new supply chain complexities and challenges—elevated costs, business model fragmentation and rising competition for top employees and drivers are just a few examples.
But there is good news: innovations in last mile delivery are just as applicable to reverse logistics. And new advances in automation technology can help fleets keep vehicles and their contents safe.
DIGITIZING DAILY FLEET MANAGEMENT
Fleet management is complicated, and it will only become more complex. Automation technology not only digitizes daily management tasks, but it can also completely transform your fleet, helping you meet changing market conditions and customer demands head-on.
By using a fleet automation solution, reportable data can be seen, understood, and acted upon effectively and automatically through integrated systems. The platform reads incoming notifications and decides if there is a routine resolution. If there is, the system prioritizes and dispatches the resolution—there’s no need for a “middleman” to read the alert and manually solve the problem.
Management teams can focus on the bigger picture with the assurance of a trustworthy system. Automating processes are creating new efficiencies and reducing time expenditures. Freeing up your staff has benefits on many levels: increased productivity, reduced costs and enhance customer service.
HOW KEYLESS ACCESS INCREASES PRODUCTIVITY AND SECURITY
Vehicle security is a major priority for any fleet-based business, but physical keys are a major source of risk. They are challenging to manage and can get lost or stolen, costing precious time and money to replace. The simple act of moving the key that drivers are used to having in their pocket into the cloud can be a major catalyst toward true fleet transformation.
When you make a key digital, it fundamentally changes how you access and use your fleet vehicles. With keyless technology, you can:
- Assign or reassign drivers to vehicles and provide instant access from anywhere
- Remotely control who can start a vehicle and the areas they access
- Grant specific access based on roles
- Set doors to lock automatically as the driver walks away from the vehicle, increasing security of the vehicle and its contents
- Unlock doors as the driver approaches to increase efficiency
Many fleet security problems are time-critical, such as an attempt to steal a vehicle or its content. By leveraging keyless vehicle access solutions, you control the “who, where, and how” of your fleet’s accessibility, immediately and automatically. With a digital keyless solution in place, only the right people with the right access with the right digital key can access a vehicle; and that access can be revoked, and the engine remotely shut down in case of any suspicious activity or potential theft.
With cargo theft on the rise, the right proximity locking solution allows you to set parameters to automatically lock the door when the driver exits the vehicle and unlock the doors when the driver approaches. This helps protect not only the vehicle and the driver but the goods being transported from point A to point B, ensuring productivity, safety and saving time on each and every delivery.
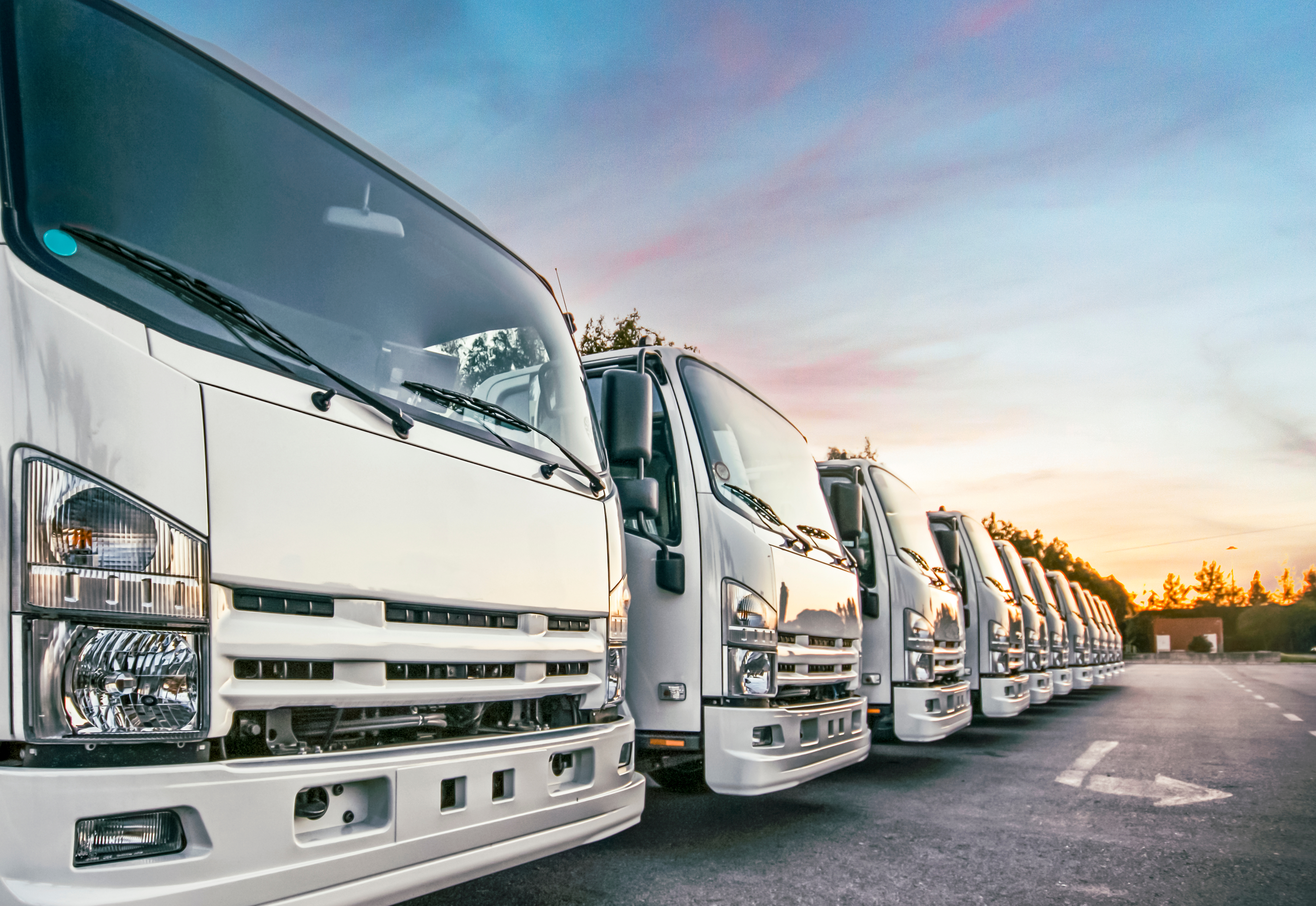
KEEPING VEHICLES ROADWORTHY, AUTOMATICALLY
Imagine a world where your vehicles automatically identify maintenance needs and schedule their own tire rotations, oil changes, and even repair services. Another benefit of fleet automation is the ability to automate vehicle maintenance monitoring—letting you stay one step ahead of any issues and keep your fleet roadworthy and safe.
Fleet managers may already receive vehicle maintenance alerts, but an automation system can inform them of upcoming repairs or part replacements, taking back the time lost to tracking and scheduling the appropriate service. Automatic maintenance work orders and tight integration with service professionals eliminates administrative bottlenecks and facilitates the ability to scale operations without the cost of hiring additional staff. Automating vehicle maintenance not only saves time, but it also establishes a database of vehicle history and all associated costs.
Dealing with unexpected repairs can take drivers off the road and consume valuable employee time if not handled efficiently. And improving the reliability of your vehicles improves the safety of your drivers and others on the road.
AUTOMATION FOR THE LAST MILE AND BEYOND
In the new supply chain reality and evolving market demands, the next step in your digital transformation journey is to turn your business insights into automated actions. The evolution of the customer experience isn’t over, and businesses should be making investments to modernize for the future. Fleets will be looking to technology to help streamline their last-mile and reverse logistics operations, and the right automation solution can truly set fleets up for success.
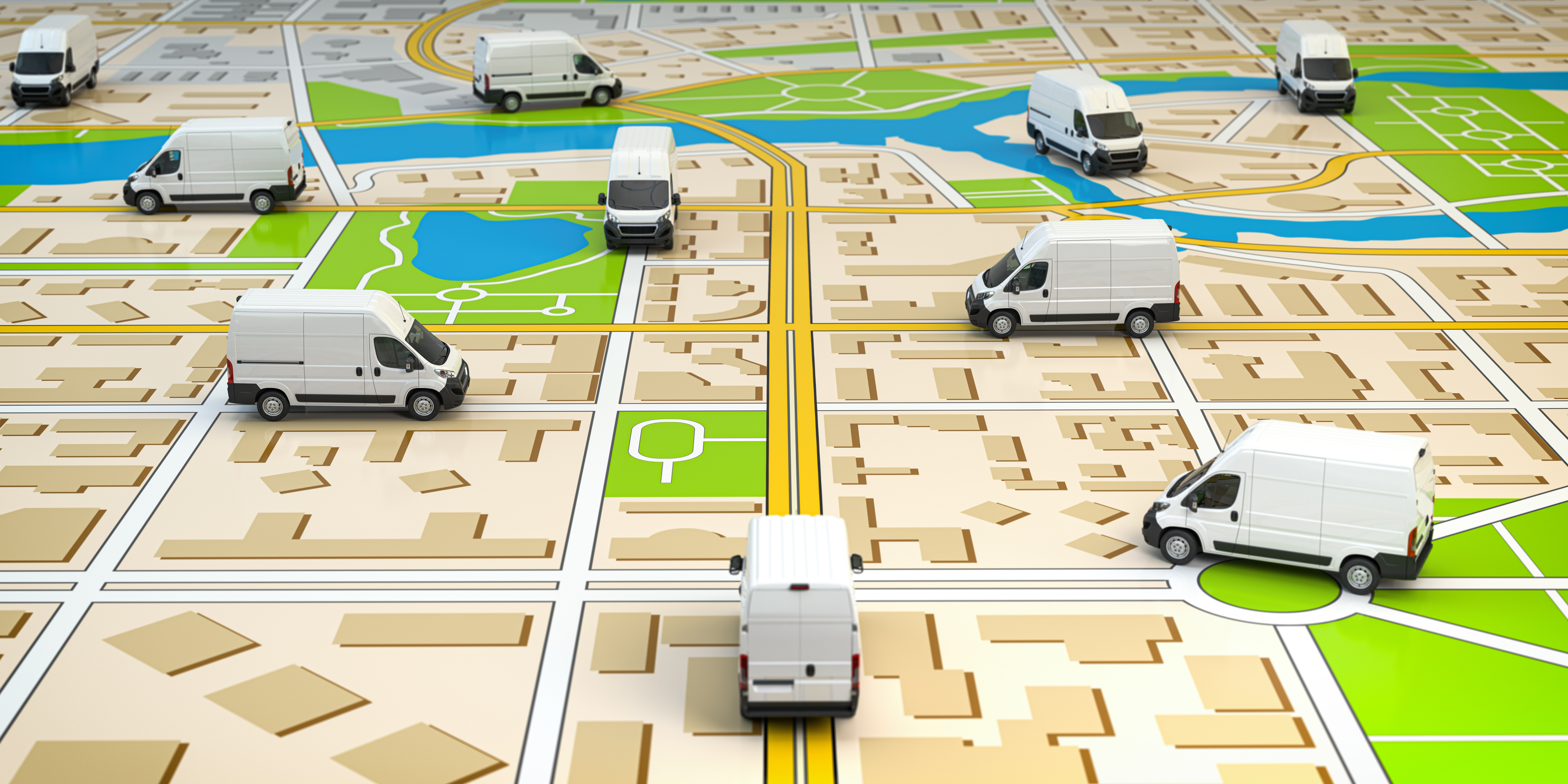
SOURCES
1 https://www.mckinsey.com/business-functions/strategy-and-corporate-finance/our-insights/five-fifty-the-quickening
2 https://www.cnbc.com/2022/01/25/retailers-average-return-rate-jumps-to-16point6percent-as-online-sales-grow-.html
Mark ThomasMark Thomas is the EVP of Marketing & Alliances at Ridecell, the leading automation and mobility platform provider for digital transformation. Prior to joining Ridecell, Thomas headed the connected car marketing team at Cisco Jasper, where he developed the product and go-to-market strategies for automotive OEMs. Prior to Cisco, Mark led product marketing at HERE, a leading automotive maps company. In addition, Mark served in marketing, strategy, and business development roles at Apple and Nokia. Mark holds a B.A. from the University of California, Berkeley, and an M.B.A. from the University of Pennsylvania Wharton School of Business.