The Reverse Supply Chain - 4.0
By Sean Magann, Sims Lifecycle Services
There continues to be a large amount of buzz about Supply Chain 4.0, but what exactly is Supply Chain 4.0? Simply put, new digital technologies and improved non-linear data flows have increased the integration between the manufacturer, distributor, and end user. In addition, advanced robotics and “data everywhere” enabled by IoT adoption will result in both increased responsiveness and decreased costs within the “regular,” forward supply chain. The questions then become, can these innovations be applied to the reverse supply chain, and will there be a Reverse Supply Chain 4.0? The answer is a resounding “yes,” and I see the following benefits:
ORIGIN OF MATERIAL
Governments and businesses continue to express concerns about the possibility of counterfeit and/or raw materials originating from conflict areas entering the supply chain. Counterfeit materials compete with legitimate products, potentially resulting in margin erosion but units used in the healthcare field could pose risks of malfunctioning defects, which could result in consequences ranging from compromised diagnosis to patient fatality. The World Health Organization claims that 8% of medical devices were counterfeit or contained counterfeit components. Verifying component authenticity is difficult, as certificates can be altered or completely forged.
Identifying the geographic origin of raw materials can also be problematic. Manufacturers have ethical concerns about using materials extracted from conflict areas because the money from the sale of these commodities is used by warring parties to fund their operations. According to HBR1 “80% of companies don’t know if their products contain conflict minerals”. The supply chain for raw materials is often highly complex, with the origin of materials difficult to trace as they move through the supply chain.
Supply Chain 4.0 does offer a solution to these challenges using blockchain. To combat counterfeit materials, blockchain, with its shared and immutable ledger, would hold the original certificate of authenticity. Any forgeries or alterations to the certificate would be obvious. In addition, blockchain could be used to trace the journey of raw materials throughout the manufacturing process.
As an example, a mass balance of copper could be traced from the non-conflict zone mining site copper smelter, fabricator, circuit board manufacturer, and Original Equipment Manufacturer (OEM). While not practical before blockchain, OEMs can now know the origin of materials.
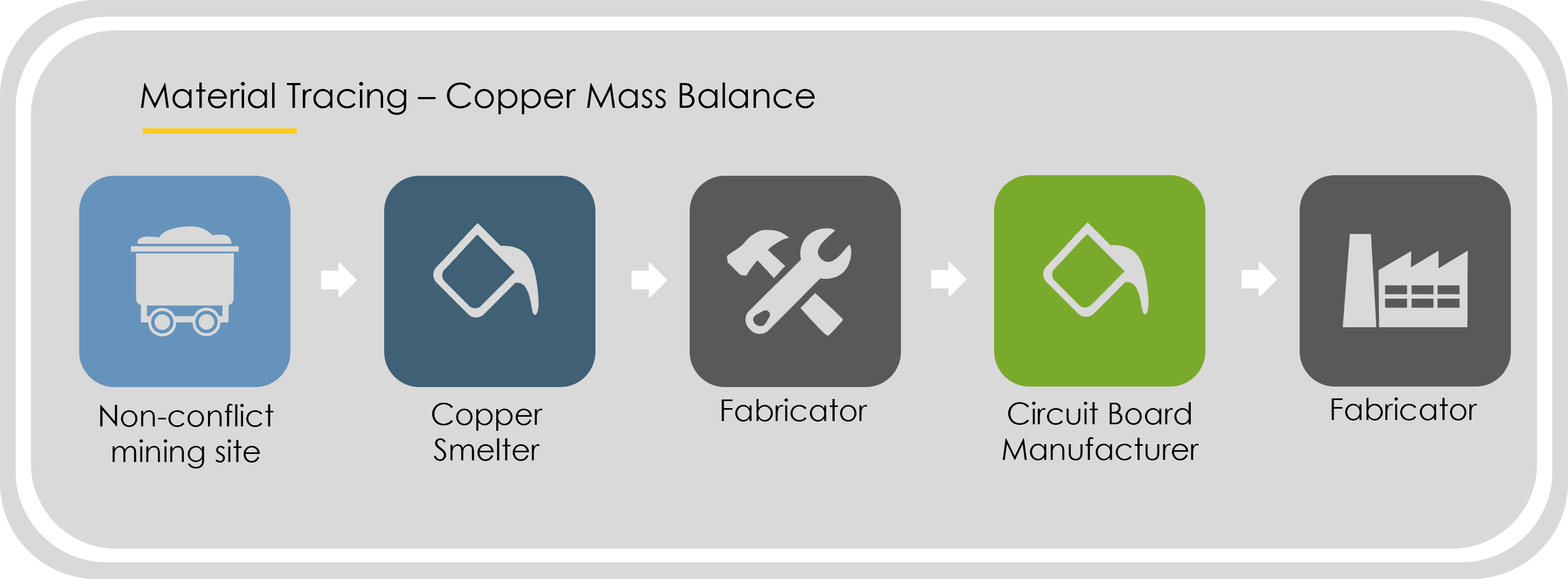
These benefits of blockchain equally apply to Reverse Supply Chain 4.0. Many proprietary materials, specifically electronic components, require destruction as they move toward the end of the reverse supply chain. This destruction is typically validated with a certificate of destruction, but as with certifications of authenticity, a certificate of destruction can be forged or altered. Blockchain provides a solution. The certificate of destruction could be stored, and its hash (digital fingerprint) would be uploaded to the block chain and alteration of the certificate of destruction would be easily apparent.
Manufacturers and customers are also demanding visibility as to the final destination of products. And blockchain enables this traceability as the materials enter the disposal and/or recycling stage. The origin of materials would continue to flow post-consumer to its final destination. Several electronic smelters are looking to trace recycled materials back into the forward supply chain completing the documentation of material circularity.
EFFICIENCY AND PREDICTABILITY
The current supply chain continues to be very linear. The manufacturer orders from the supplier, the distributor orders from the manufacturer, and the consumer orders from the distributor. Surprisingly, many of these orders are still done using highly manual tools such as spreadsheets, forms, and emails. With Supply Chain 4.0, all parties are interconnected with real-time digitized data. Consumer demand instantly flows to all parties in the supply chain allowing for better planning, predictions, and asset utilization.
“The more broadly technologies are deployed - from raw material extraction and sourcing to refinement, manufacturing, shipping, and sales - the better-positioned companies will be to compete over the longer term.” -Forbes, Nov. 2021
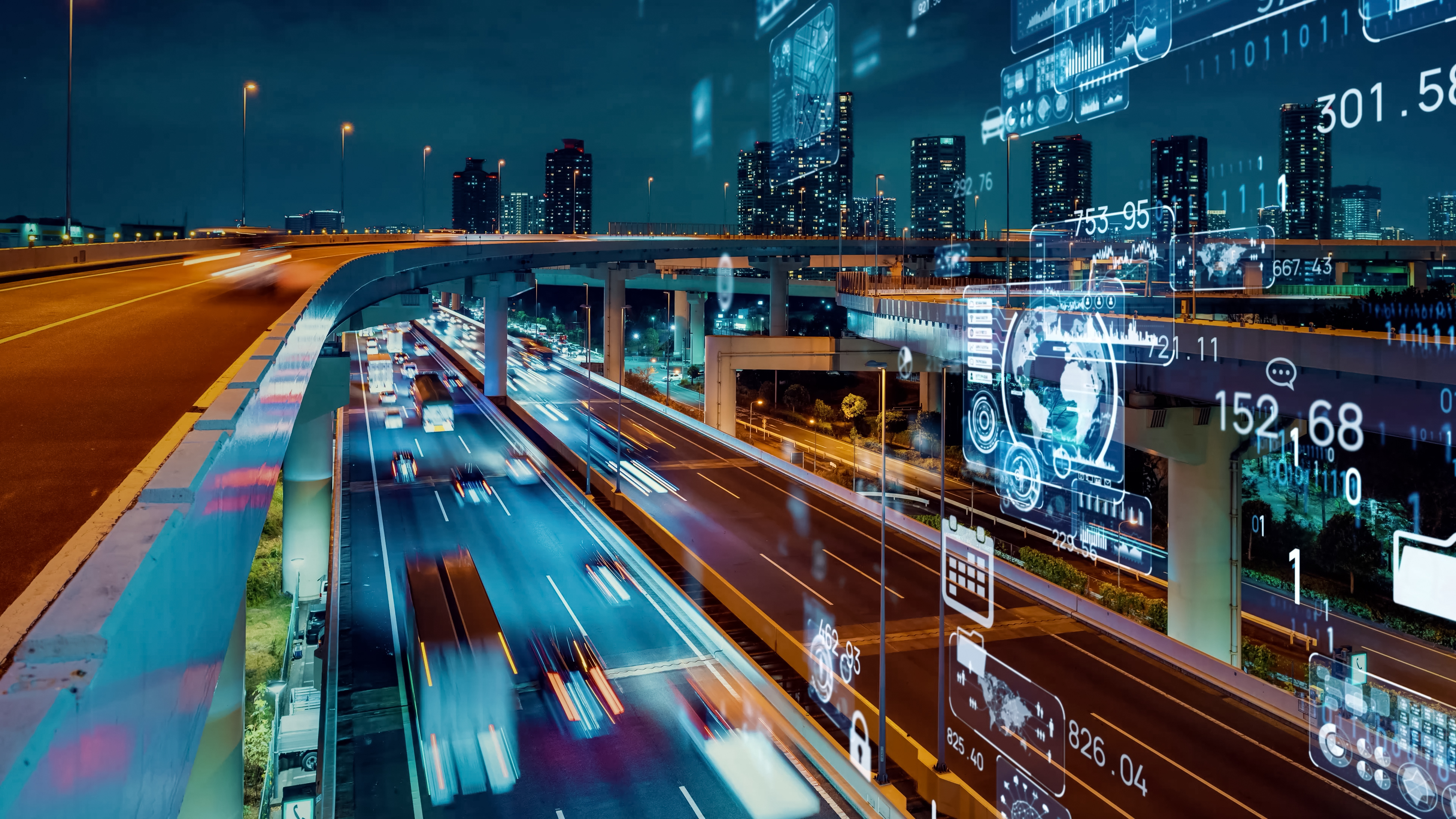
This dynamic digitization of data will also enable Reverse Supply Chain 4.0. A customer requesting the return of an item would automatically and immediately trigger a chain of events. The logistics to pick up the item with the most efficient routing would be scheduled, space at a reverse distribution facility would be held, and an order for the final disposition of the material would be built. In the ITAD space, world-class companies are using these technologies to automatically trigger trucks to be deployed to clients once a specific number of assets are ready for pick up and slotting in production time for the processing of these assets.
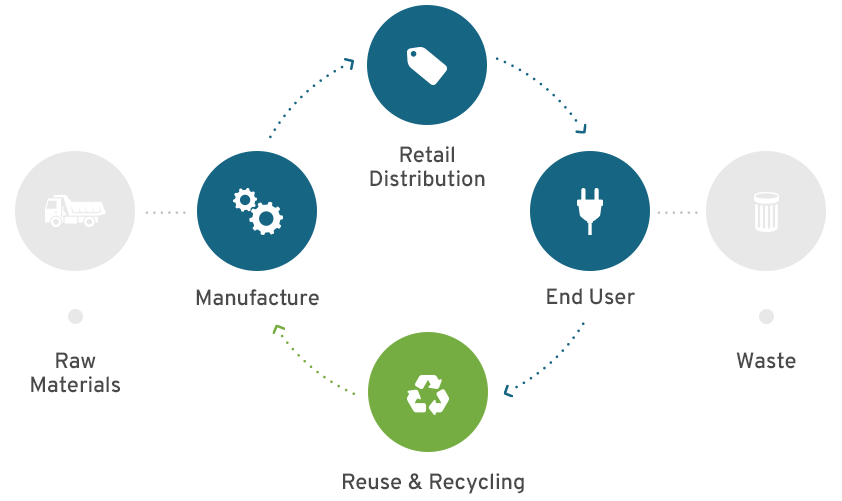
ENABLING SUSTAINABILITY
Supply chain issues continue to pose a challenge for a variety of industries and much attention has been focused on the global electronic chip shortage. Factors such as China’s COVID lockdowns and large forward supply chain bottlenecks continue to exacerbate the problem. Both the United States and EU Governments have passed legislation to fuel the domestic production of electronic chips but these investments will take years to have an impact. To bridge this gap, forward-thinking companies have looked to utilize an untapped source of supply, The Reverse Supply Chain.
As materials move into The Reverse Supply Chain, they may still contain components that could possibly supplement demand in the forward supply.
My company is currently working with several large enterprises to implement programs for the repurposing of enabling the harvest, testing, and recertification of components for either critical spares or as parts in new server buildouts.
In addition, electronic components are highly engineered products that generate large amounts of carbon during the manufacturing process. The reutilization of materials reduces the need for new components and the carbon created during the manufacturing process.
A key benefit of Reverse Supply Chain 4.0 is the real time, end to end transparency of the entire supply chain which is necessary for the large scale reutilization of components. Traditionally, Forward and Reverse Supply Chain sat in separate silos within an organization but 4.0 looks to unify the two. Data for the entire supply chain will reside in one place, giving enterprises the ability to truly see the entire availability of materials.
1 https://hbr.org/2017/01/80-of-companies-dont-know-if-their-products-contain-conflict-minerals
Sean MagannSean Magann, Sims Lifecycle Services’ Chief Commercial Officer, is one of the world’s thought leaders on all aspects of managing the lifecycle of enterprise IT and data center equipment. With more than 20 years of industry experience coupled with developing and executing the geographic expansion of facilities in international markets, Mr. Magann has developed a complementary background for helping global fortune 500 companies manage successful IT asset disposition and cloud recycling programs.