Maturity Assessment: How Future-Proof Are Your Operations?
By Jennifer Foxworthy, Triage Partners
For 3PL providers and logistics companies, the key to surviving inflation, rising chain partner demand, and lingering pandemic effects is modernizing warehouse operations. Nearly all supply chain leaders identify innovation as “extremely important” to growth — yet, the biggest challenge for these companies is determining where, and how, innovation fits within their operations.
That’s why maturity assessments are a great place to begin.
In this article, we explain how to pinpoint operational gaps and opportunities, then provide a roadmap for successful warehouse modernization.
INNOVATION IN THE WAREHOUSE: FROM SILOED TO STREAMLINES OPERATIONS
Innovation in warehouse operations isn’t just wishful thinking — it’s a necessity. If you’re not innovating, you’re not growing. Third-party logistics providers in particular are under constant pressure from original equipment manufacturers (OEMs) to streamline and optimize their operations, and always need to be searching for new, unique, and more effective ways to delight their customers.
But creating digitized, resilient warehouse operations isn’t just a matter of installing new systems and software — it’s knowing where, and how, to use these tools for maximum impact.
Here are three technology trends in warehouse operations and, when done correctly, how they transform operational silos into streamlined processes:
Cloud
From processing returns to inspecting parts, there are already many moving parts in shop floor operations. But factor in multiple warehouses in various geographical locations, and shop floor control is downright overwhelming. This is where cloud-based software, like Triage Partner’s proprietary WipIT™ software, shines: it integrates seamlessly with your ERP and WMS systems via APIs to standardize operations and processes across all of your warehouses, regardless of location.
The benefit: Cloud-based software gives you total shop floor control and visibility into your supply chain. It orchestrates processes across all of your warehouses, allowing you to manage labor productivity, track materials, and streamline material planning at scale.
Business Intelligence
Collecting data is only half of the equation; the other half is knowing how to interpret it and use analytics to improve workflow efficiency and productivity. The right cloud-based software — like our WipIT™, Account4IT™, and FormIT™ solutions — provide clear, actionable data that uncovers patterns in your workflows, reveals bottlenecks, and highlights opportunities to reduce long-term costs.
The benefit: Tracking facility metrics and employing a data-driven approach makes warehouse operations more resilient, agile, sustainable and scalable. With readily available data on everything from inventory to number of returns, you can pinpoint ways to enhance the customer experience and, ultimately, become a better partner by shifting from reactive to proactive management.
Automation
Warehouse operations include many repetitive, process-oriented tasks like inventory management, fulfillment, and invoicing, all of which are well-suited for automation. But automation for the sake of automation won’t reap you the most rewards — so start by asking yourself two key questions: What manual steps in your process can you automate, and where will automation provide efficiencies in your process?
The benefit: Automation minimizes human error, accelerates turnaround time, and ultimately, saves both you and your customers money. It frees employees from time-consuming manual tasks so they can focus on areas where critical thinking is required, like relationship-building and business strategy.
MATURITY ASSESSMENT: HOW FUTURE-PROOF ARE YOUR WAREHOUSE PROCESSES
Even though most companies know they need to modernize their warehouse operations, the real challenge lies in knowing where to start.
Whether it’s lack of data, limited technical expertise, or a combination of both, many companies don’t have the capacity to assess warehouse improvement options on their own. But a good starting point for transformation is to consider the following questions:
- What are our metrics? How are we currently measuring ourselves, and what are we measuring against?
- Do we have the right tools? Does our technology support the future transformational vision for our organization? Does it provide the automation and analytical capabilities that we need to streamline operations? What are the limitations of our software?
- Do we have the right talent? Does our culture support experimentation and continuous improvement? Do we have digital-native talent who understand how, and where, to apply technology to transform our operations?
- Where are there gaps in our processes? Are our processes well-defined and consistent across warehouses? When was the last time we audited our processes?
Another way to identify gaps is to imagine your entire warehouse operations workflow as a metal chain, and each workflow component as a link: if one link is broken — even if you don’t feel it initially — your entire workflow is broken. Instead of band-aid solutions to fix those broken links, the key to innovation is to start by intentionally pulling and breaking those links. This stress testing not only forces you to fix the broken pieces, but also highlights other areas affected by the disruption so you know what needs to be optimized.
Finally, conduct these assessments early and often, and ask for feedback from the people managing these individual processes every day. There’s no finish line when it comes to optimizing warehouse operations — instead, it must be assessed repeatedly as business and customer needs evolve.
TRANSFORMATION ROADMAP: THE RIGHT PATH TO MODERNIZING YOUR WAREHOUSE
Historically, companies have struggled to transform their warehouse operations for various reasons: lack of experience, cost concerns, inability to define their wants and needs from a solution, etc. But the largest inhibitor is fear of change. Many companies will stick with their current system — even if it’s inefficient and costs them more in the long run — because the change is monumental.
Luckily, there are some steps you can take to ease your transformation:
- Define your enterprise vision and strategic goals. What are your short-term goals? Long-term goals? What external influences — competition, supply chain disruptions, etc. — are most likely to impact your business, and how can you adapt to them?
- Map out your warehouse operational objectives. Don’t innovate just for innovation’s sake — determine how each technology you implement ties back to your overarching objectives (e.g., cloud-based software streamlines materials tracking, which reduces unnecessary touches and reduces transportation costs). Also, figure out your wants and your needs: if money were no object, and you didn’t have any technical barriers, what would your wish list look like for your new solution?
- Choose the right partner. Overhauling warehouse operations is a massive undertaking that you shouldn’t tackle alone. Vet multiple service providers and ask about their capabilities, change management approach, and ability to fulfill your requirements and wish list. Do you require workers to be on site, but you’re currently facing a talent shortage? Triage Partners, for example, provides highly certified, in-demand talent and colocation services to meet requirements like these.
Warehouse operations will continue to be scrutinized as market demands rise and supply chain disruptions occur. To succeed long term, 3PL providers and logistics companies need to turn inward to find new ways to reduce costs, boost performance, and maintain a competitive edge.
For more information on how Triage Partners can help you meet your operational needs, please visit www.triage-partners.com or email Jennifer Foxworthy, Director of Business Development, Integrated Supply Chain (jfoxworthy@triage-partners.com)
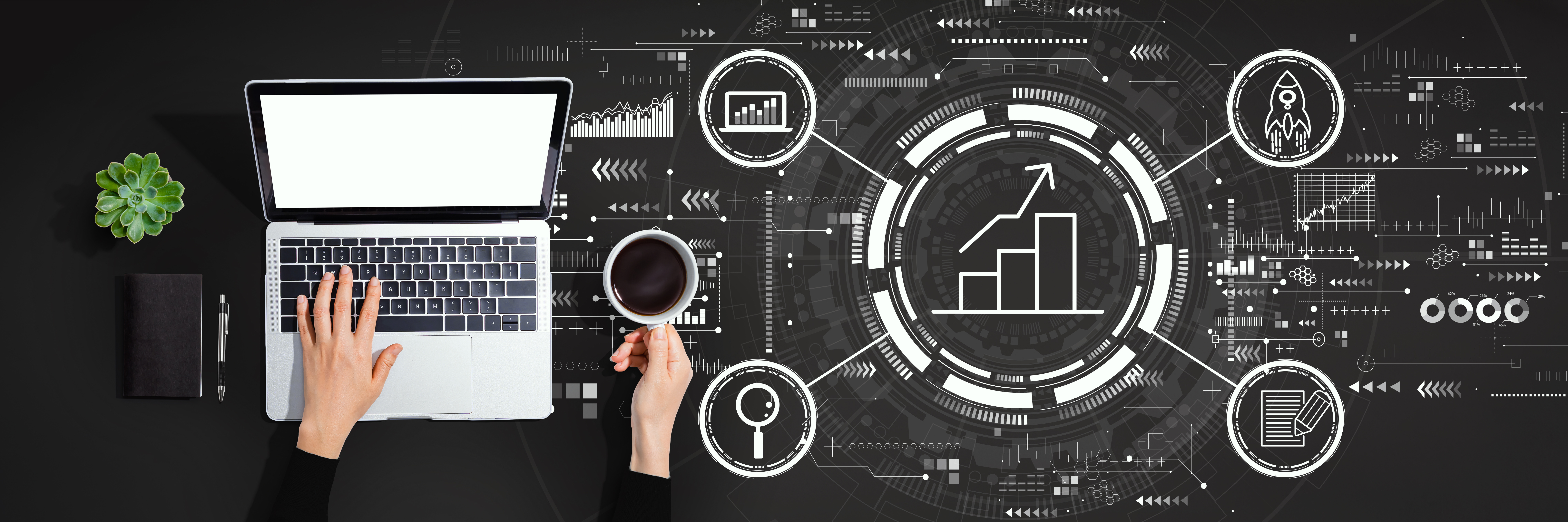
Jennifer FoxworthyJennifer Foxworthy is the Director of Business Development at Triage Partners, LCC for the Integrated Supply Chain division. Jenn has over 25 years experience in the logistics software space with the majority of that time focused on digital transformation initiatives in reverse logistics. Her passion for innovation and precise attention to detail are important for the accuracy and success of the solutions Triage delivers to its customers.