Next Best Practices - Real-Time Data to Unlock Optimization
By Sebastian Titze, BEUMER Corporation
Ever-evolving purchasing decisions, market volatility, global crises and disruptions have substantially impacted peak season and operational efficiencies to create a new normal unlikely to be quelled for the foreseeable future. Labor shortages which correlate with required increases in labor wages, increased fuel costs as import/export is impacted by the war in Ukraine and inflation seeing one of its highest increases in over 17 years, have required businesses to re-evaluate efficiencies to ensure profitability. These challenges have been seen across the industry from CEP to fashion. Fashion fulfillment companies are facing a barrage of challenges today, such as the deluge of returns. However, it always comes down to: how can they be more efficient; how can they improve performance?
Growth in e-commerce represents a massive opportunity to the CEP industry, but also comes with its own set of challenges. Distribution centers must make adjustments to thrive in an era of soaring e-commerce. One of the best and most cost-effective ways to keep up is digitalization.
As countless operators seek to best prepare for peak seasonality amidst this changing environment, the focus on integrating new, cutting-edge technologies requires forethought and historical indexing to form strategic plans. Additionally, purchasing behaviors have substantially changed with e-commerce. With the exponential reliance on e-commerce and increase in per capita expendable income, end users’ behavior has adapted to purchasing multiple items and returning the ones that are not a “perfect fit” for them. To ensure you successfully mitigate the effects of peak seasonality and disruptions, an integrated logistics information system can be implemented to augment your automation and avoid availability bias.
Innovations in AI, the Internet of Things, automation and advanced analytics seem more commonplace each day. DHL’s Logistics Trend Radar tracks these innovations and many more as the industry collectively evolves practices to improve practices with each new iteration of technological advancements. Recognizing these innovations, it is nothing new to collect, analyze and utilize data to predict future events and returns. Statistical systems have long been standard inclusions in systems. What has fundamentally changed the way you can make enlightened decisions is the ability to capture data in real time and then make immediate decisions based on that collected data. No longer are operations reacting solely to data from the prior month or even prior week. Rather, the data you collect can be used in real time in tandem with historical trend analysis to proactively maintain throughput and optimal efficiency throughout your operation. However, data use is far too often limited to decisions impacting customers and end consumers, rather than examining sortation/material handling data points. According to my colleague Anders Lildballe, BEUMER Group’s Lead Software Product Architect, countless facilities utilize only 60–70% of their capacity.
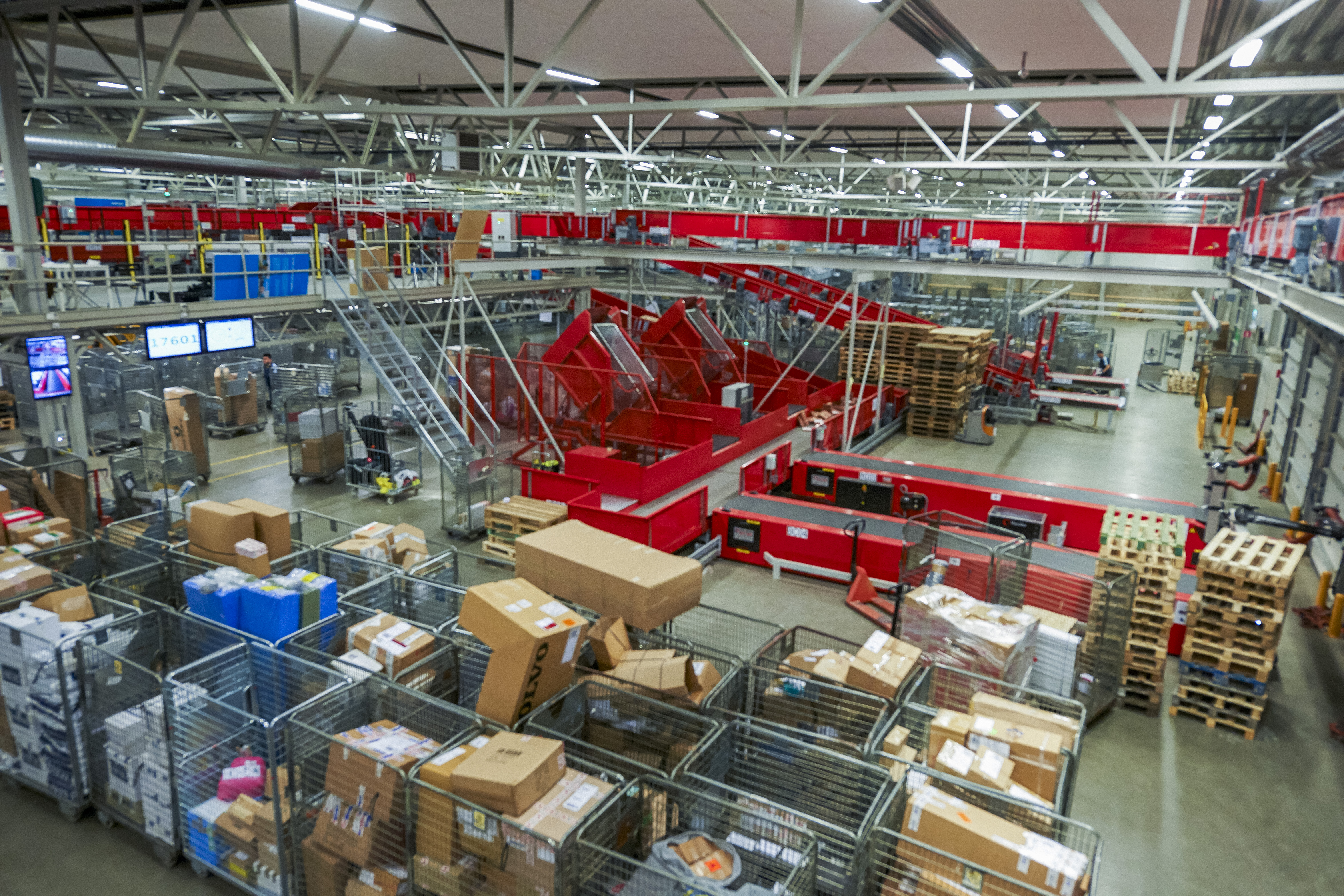
Billions of data points can be utilized to examining sortation/material handling to proactively maintain throughput.
SET THE FOUNDATION
Digitalization represents the process of collecting enormous amounts of information from distribution hubs – equipment and operations included – which is then stored as data. Understanding and working with this data is an extremely valuable tool for improving the throughput of a distribution center. Digitalization and automation are catalysts for efficiency in countless organizations. While BEUMER does support operations that have integrated fully autonomous solutions throughout their facility, we recognize many small- to mid-size operations are either financially unable to fully automate or are not fully aware of how they can begin automatizing in ways that enable efficiencies and future automation growth. Regardless of your position as an industry leader or a smaller plant, there are automation solutions available that allow you to reclaim floor space by transforming overhead space into a powerful omnichannel sort-and-return solution or to install equipment designed to extend your handling mix to handle the widest possible range of items while maintaining the scalability to be reconfigured for future growth with minimal downtime. In addition to the optimization benefits automation provides, it also unlocks enhanced proactive decision-making through real-time data analysis. Further, valuable data points exist in sorters, scanners, scales, chutes and conveyors throughout your facility.
Recognizing differing aptitudes and resources for digitalization and automation, we rank operations on a scale from manual operations to full digitalization. Regardless of rank, the goal of a Logistics System is to condense the potentially billions of data points to unearth issues that must be resolved or opportunities to achieve greater efficiency.
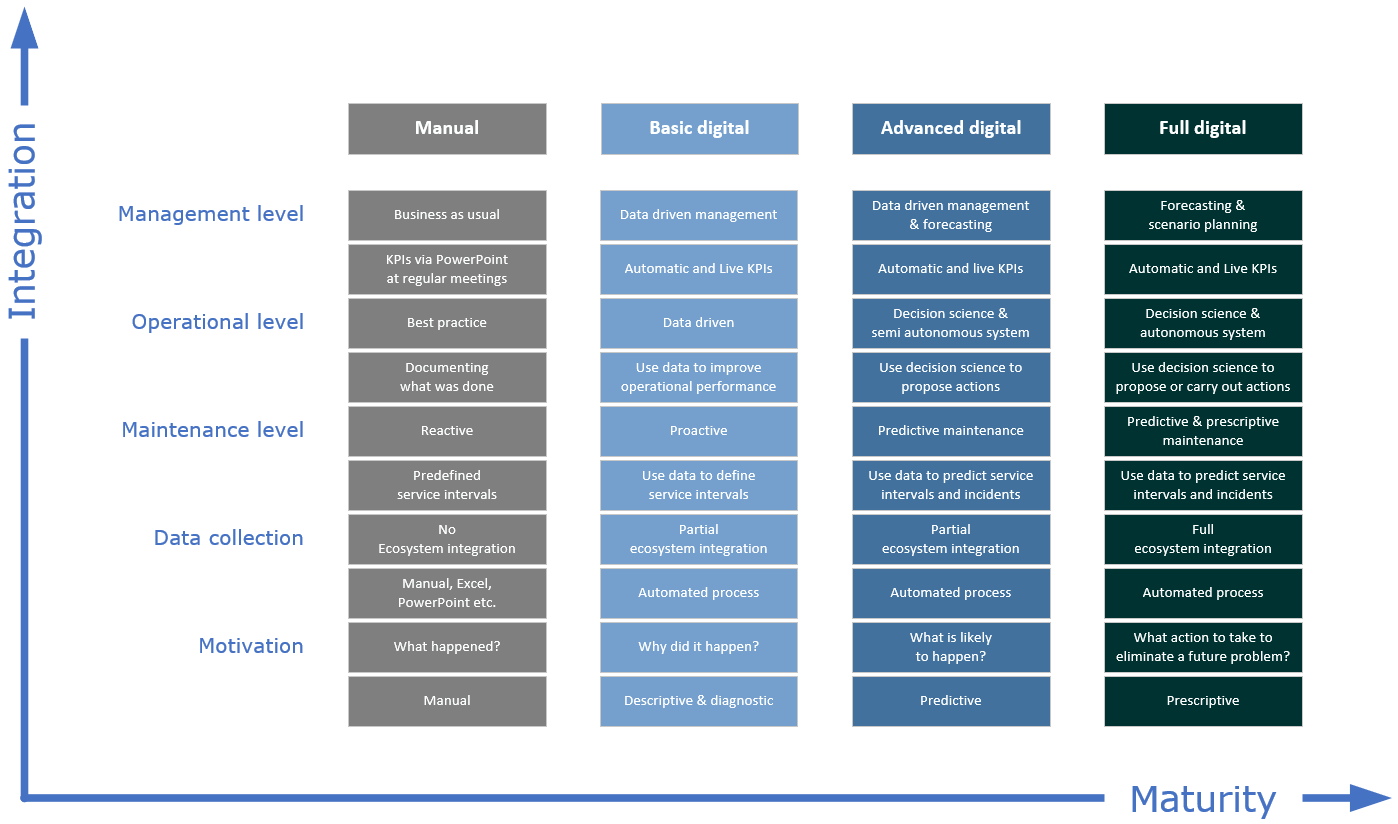
Operations are ranked on a scale from manual operations to full digitalization based on their digital integration and maturity.
COMPLEX SYSTEMS MADE SIMPLE
Yes, Logistics System can be complicated. However, the processes within the system are straightforward. We must induct something, then get it out of the system in the most efficient way. Instead of strictly making decisions based on intuition or observations, the system presents facts that allow you to understand exactly what is happening throughout your process. Many have known that, before a Logistics System was in place, you would be forced to accept that your operation was impacted by events that you could not identify as a contributing factor. Now, the data brings to light the event and its impact so that you can counteract the event immediately.
Traditionally, operations had “islands of automation” where a machine in one corner of the building could not communicate with a machine in the opposite corner of the building without a human to be the interface between the two. With today’s automation, it requires that machines communicate with each other at high levels. It also requires that, when humans are interacting with a machine, they operate it well. The real-time data collected not only reports on how the machines communicate, but also how well the operator is performing their tasks with increasingly complex machines. This allows your operation to align in all areas of the warehouse.
FIELD PROVEN
From providing operation support at many levels, like basic machine controls to computing complex statistics, logistics systems integrate with warehouse management systems and subsystems. BEUMER’s Logistics System utilizes Software Suite, whose task is simple: It must enable monitoring and control of the material handling system to ensure optimum availability and efficiency at all times. Each of the control modules in the Software Suite is based on the robust, field-proven IT architecture which has been continually evolved over the past 20 years. The software provides control of the material flow from the moment that it enters the system until it is ready for dispatch.
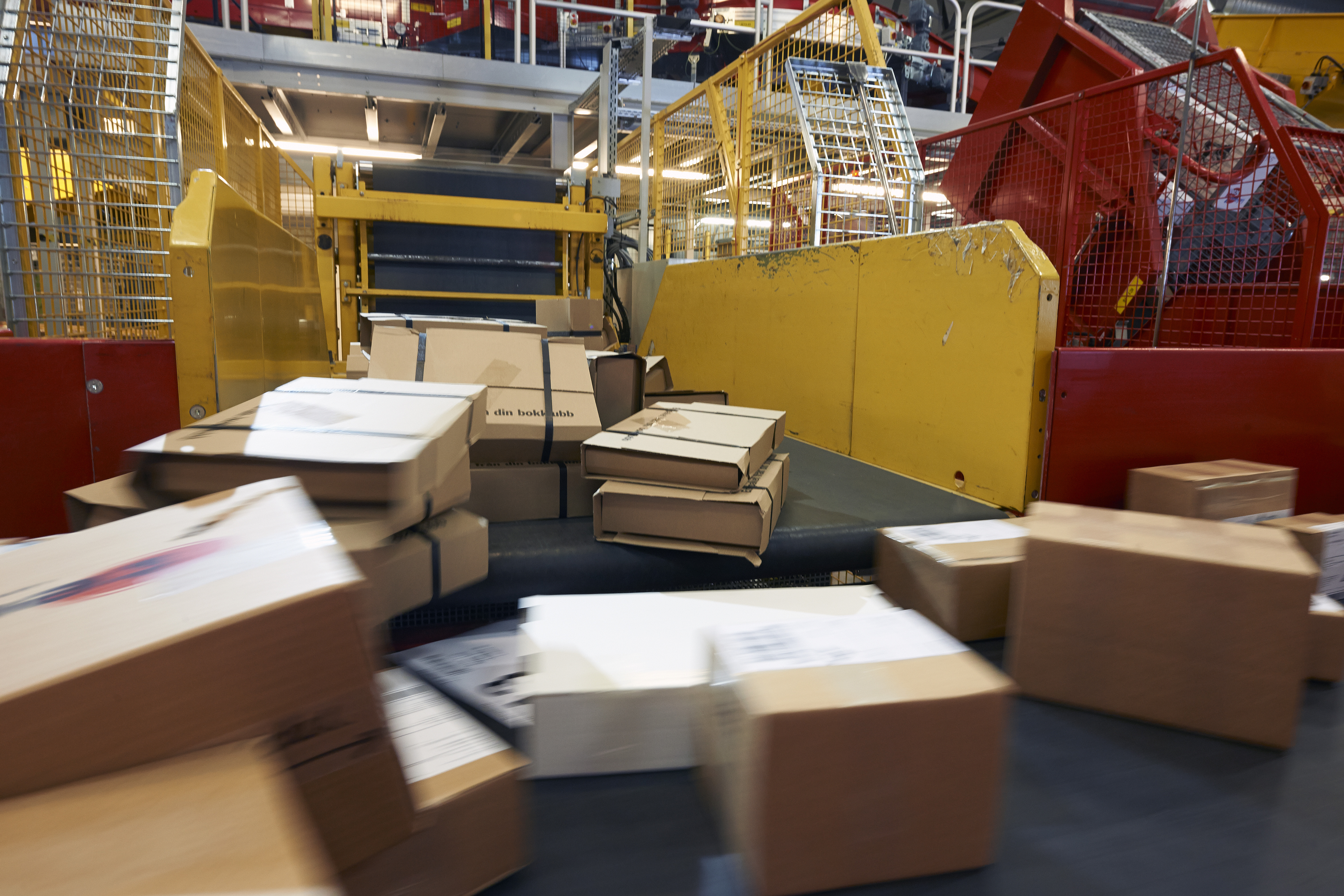
BEUMER’s Logistics System utilizes Software Suite to enable monitoring and control of the material handling system.
TALENT ASSISTANCE
Today’s dynamic labor market, which continues to fluctuate, has made it much more difficult for companies to find skilled workers who can operate such complex machinery. Logistics Systems empower skilled associates to determine where potential backlogs may occur to preemptively respond and mitigate potential downtime. By using real-time data, managers are able to make determinations about efficiency, machine communication and operator performance while utilizing staff who may not be as skilled with the equipment.
HOTLINE SUPPORT
Let us assume you now have adopted a Logistics System and are actively analyzing and responding to events to maintain efficiency. What else does the Logistics System offer you? BEUMER currently streams data from 160 sites, which creates the terabytes of data that have honed our ability to analyze why something happened, could happen and predict a future event. Hotline engineers bring a minimum of four years of field experience commissioning systems and expert experience in electrical, mechanical and software issues. Engineers are available to provide performance monitoring, remote optimization, OS patching, Profibus monitoring and virus protection. It is no surprise to anyone that cyber attacks continue to increase, and hackers continue to seek any vulnerability to shutter your organization for ransom. Engineers are able to see abnormalities and vulnerabilities in your operation to allow your team to proactively respond and keep malefactors at bay.
It is vital to note that the information being collected is only machine and non-personal data. However, this data is the secret ingredient to some operations, which means that data must be protected as if it were personal data. From collecting, analyzing, enriching and reporting on the data, BEUMER prioritizes information security at every step to ensure you the peace of mind you deserve from an industry-leading partner.
FUTURE FOCUS
Future innovations almost inevitably point to self-learning machines that utilize the real-time data to self-optimize into the system. Currently, we are encouraging operations to move from responsive to predictive operations. The future will be shifting from predictive to prescriptive operations where machines operate at their full capacity with ease. Additionally, the future includes greater opportunity for greater integration with third-party data that allows for optimizations from sourcing materials to last-mile delivery. PostNord has successfully reduced mileage by utilizing data to create last-minute, automated route detours to avoid congested roadways.
“Before our digitalization program, we operated as many CEP companies continue to do—with forecasting and planning contained within silos, on spreadsheets and without automatic data entry or analysis,” said Christian Østergaard, Lead Visionary & Senior Group Strategist at PostNord. “This meant multiple iterations, a ton of data at risk of being manually mishandled and a lack of cohesion between our sections.”
Post Nord began by inputting years of data, then mapping the data to predict parcel volume for optimal planning. The next step was to build the models which review business constraints to AI flows, where volume forecasts, schedules and plans can be created through AI distribution modeling.
According to Østergaard, “Through our digitalization efforts, we’ve become much better at predicting volumes and workflows. The solutions are so user-friendly for our employees that they are eliminating wasted time. Our processes are constantly improved and optimized, which helps us save significant costs while also helping us achieve our sustainability goals by reducing mileage.”
SOURCES
- BEUMER Group. “PostNord Unlocks the Potential of Data to Empower Its Business.” Courier, Express, and Parcel Knowledge Hub, https://knowledge.beumergroup.com/cep/data-to-empower-business.
- “Logistics Trend Radar. Delivering Insight Today. Creating Value Tomorrow.” DHL, https://www.dhl.com/global-en/home/insights-and-innovation/insights/logistics-trend-radar.html.
- Rockeman, Olivia. “US Inflation Quickens to 9.1%, Amping Up Fed Pressure to Go Big.” Bloomberg.com, Bloomberg, 13 July 2022, https://www.bloomberg.com/news/articles/2022-07-13/us-inflation-accelerates-to-9-1-once-again-exceeding-forecasts#:~:text=US%20CPI%20June%202022%3A%20Inflation,Once%20Again%20Exceeding%20Forecasts%20%2D%20Bloomberg.
Sebastian TitzeSebastian Titze, Director, IT and Digital Transformation – North America at BEUMER Group, has nearly ten years of automation and material handling experience. He is responsible for regional IT operations, service delivery and service level quality, and service cost performance. Additionally, he’s focused on developing and delivering high-impact performance improvement initiatives in operational and strategic information technology, information systems, and business workflow- and process-centric digital transformation.
As a key member of the BEUMER Group IT leadership network, Sebastian contributes to the definition of BEUMER Group-wide objectives and strategy for information technology, information systems, internal digital transformation and digital workplace innovation. Sebastian joined BEUMER Group as Marketing Manager in 2015, after previously completing two internships with the company.
With MHI, Sebastian is a Member of the Advisory Roundtable, Chairman of the Conveyor and Sortation Systems Group, Chairman of the Advisory Board of the Young Professionals Network and Director of the Material Handling Education Foundation, Inc. (MHEFI). Graduating from his studies in 2015, he holds two Master’s degrees in International Business Administration, with majors in Strategy and Innovation, as well as International Business & Enterprise.
ABOUT BEUMER Corporation
BEUMER Corporation, headquartered in Somerset, NJ, is the wholly owned U.S. subsidiary of Beckum, Germany-based BEUMER Group. Founded in 1977, BEUMER Corporation is an industry leader in the design and manufacture of material handling, automation and intralogistics systems, operating four U.S. business lines: Conveying & Loading, Packaging & Palletizing, Sortation & Distribution and Airport Baggage Handling. BEUMER Corporation offers a complete range of design/build services, including engineering and systems design, project management, installation and commissioning, and customer support. For more information, visit www.beumer.com.