When a Systems Designer Walks into the Warehouse
By Peta Goldberg as mentored by Anthony Goldberg, Antel Solutions Pty Ltd
It is a strange thing, to find affinity with a sphere of practice that looks at first entirely different to your own. I learned this as a freshly minted communication designer who was asked to walk into a warehouse with no tools but a pen and paper. I was there to witness and scope a standard operating procedure for a new kind of Reverse Logistics program, particularly focused on the Fast-Moving Consumer Goods (FMCG) backdoor management. I thought this would be simple, if perhaps out of my scope as a task. And yet I found myself fascinated by what I saw curious to know more. Logistics at its core reflected back at me my own practice, what I did and believed in as a Designer. What I witnessed there, ignited a curiosity for systems and their design, structures, and management of action and activity.
Logistics and Systems Design have something in common, they are at their core a means of enacting movement. Whether this is of goods being moved and managed or nudging the actions and attention of audiences both lead to incentives and solution-based thinking. Many in my own field of Art and Design are left slightly befuddled by my excitement over Logistics and its Reverse practices because the way we engineer and problem-solve has a kinship that is not always seen. What I have learned in my brief time shadowing and working on curating processes and the dissemination of data and information in this field, is that Design and Strategy matter in Reverse Logistics. As I engaged more and was introduced to Logistic processes through the tasks I was given, I became more curious about this relationship. It started by understanding how production and commodification do not always do enough to produce healthy, sustainable, and responsible supply models - this challenges Reverse Logistics practices on a day-to-day basis. When one realizes that a product’s potential can affect any landscape for better or worse, it is not just ethical, but extremely practical and business savvy to consider the life cycle impact of this in a supply chain system.
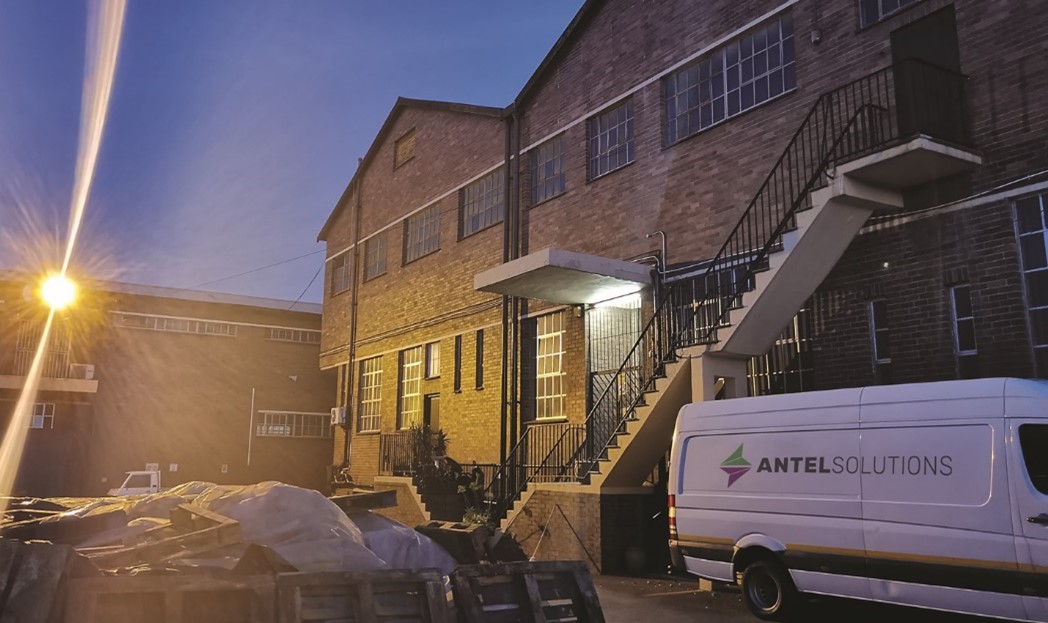
Critical engagement in the Design world is growingly using its role to emphasize person-first philosophies (such as user and human-centered design) as a means of dedicating its practices to sustainability and social responsibility. This is important as it is the user who must understand the impact of the decisions they choose and as well as the capabilities of systems that engage them. This reflects the nature of supply chain and Logistics cycles where those that engage these systems must understand the intent and goals of the systems they partake in, to curate supply and returns. Through the correct lens, Logistics can create practices that allow one to locate and reform systems with high environmental costs (whether this takes place during the act of production to unseen circumstances of the product) or costly negative social impact such as poor service delivery.
Integrating Design as part of your business model becomes a reflective process, where all levels of one’s supply chain and systems are preconceived and validated by the impact it has on the people who use it and the landscape it engages. When one curates a business model and production in this way, all possible avenues and actions are measured in their ability to benefit your business, the consumer and environmental landscape as well as, and most important of all - brand equity. I believe this is what makes Reverse Logistics so unique in terms of design thinking, the very essence of the practice must constantly engineer and creatively problem solve within large infrastructures that can be unforgiving. The power of Reverse Logistics is in the salve of circularity, but sometimes a forgotten resource and instigator of change that is ripe that of people and their ability to be a part of the system.
Working in the unique landscape of Johannesburg, the largest urban hub of South Africa, Reverse Logistics is a necessity but too often seen as an inconvenient result of Forward Logistics. We deal with an economy and social infrastructure that sees divides amongst classes as well as access to technology. Despite this, it is a bright and exciting landscape for Logistics because the potential to innovate is everywhere. Systems blossom out of needs, but when one takes the time to care and cultivate these activities and practices, wealth and gains can be twofold. There are a few dedicated businesses that deal with the practices of Reverse Logistics in our landscape, but from our current experience, it is rare to dedicate one’s business solely to the FMCG industry. This is an industry that is a behemoth of networks, well-worn warehousing practices, and an array of issues that are site and product-specific. Creating a singular system or technology simply is not enough for groundwork and upliftments. We needed something that would impact the in-store landscape while fitting into activities of warehousing staff all the while still meeting the client and store needs.
Reverse Logistics is seeing a rhizomatic growth in how technology is being applied and cultivated to amplify its activities. But at its lowest barrier, technology should not be for technology’s sake. It must hinge as the solution to the site-specific needs of its users. This is where ‘Design as Strategy’ can become core to ways in which Reverse Logistics is practiced. In our specific landscape, technology comes with the complex caveats of being both an instigator of innovation but also a potential gatekeeper of much-needed accessibility when held in exclusivity.
It is important to mention that when we began our journey into Reverse Logistics practice, we had acknowledged that our system (at the time, whatever it turned into) would have to work in an already functioning Logistics ecosystem. We knew that its mechanisms had to be adaptable to support both the client and the product. We wanted a process that was flexible enough that it could be used in any kind of situation – from typical good collections (uplifts) to store-level data collection if and when needed. Also, we wanted to engineer a process that could intuitively guide and be easily learned by anyone which we realized later, opened up the potential scope of employment opportunities. Our system thus had a skeleton: It must process exchanges, collect all points of data, and most of all guide its user through the process.
Our perceived experience saw that when engaging with many multinationals it was found that Reverse Logistics was a requisite practice that hardly anyone tackled or knew how to address successfully. As we can acknowledge (in contrast to Forward procedures) Reverse Logistics in the FMCG landscape, is messy, irregular, and comes with unique challenges. The shifting of one’s procedures to Reverse processes have produced many creative or carefully considered solutions, but what has been a constant, is the need for focused attention on systems and information output. The processes of Logistics groundwork are essential but what it produces that is truly valuable, is the information it generates. It became an interesting niche framework and the market need to provide people with immediate information about the product. An example of its impact can be seen in an issue around customer claims, where, in our landscape, it is integral data to the supply chain process but accessing it was frustrating and exasperatingly difficult to get. Another is how stakeholders in this space had to deal with issues around quality and control of brand equity. The processes and managing needs here were all available in theory but nobody knew how to implement them in practice.
People and staff on the ground, who could affect the Reverse processes we needed, had the potential to become our biggest manageable asset. This was viable with time, training, and a guiding structure to assist those performing the most appropriate, decided-upon methodology in a Logistics space. Thus, we invested in mobile and digital technology to be able to pick up, structure, and provide this information to and through them. What was so valuable in having conversations around technology at the most accessible level, was that it gave users a foundation to how the technology worked (as there would be some background knowledge on mobile usability). As well, immediate accessibility was made simpler as it relied on technological systems that were embedded in a smartphone itself. This accessibility, by the nature of how we use the devices in our day-to-day lives, meant data input could be immediate and be made a part of the warehouse’s best practice. By cementing the procedure in the cultures of the warehouse space, it would become more common and this could lead to better quality management of all Logistics practices. Changing the way that information was managed at the ground level of the landscape meant that we could direct information to where it needed to go immediately. This meant we could give the correct stakeholders access to their information in real-time with little error.
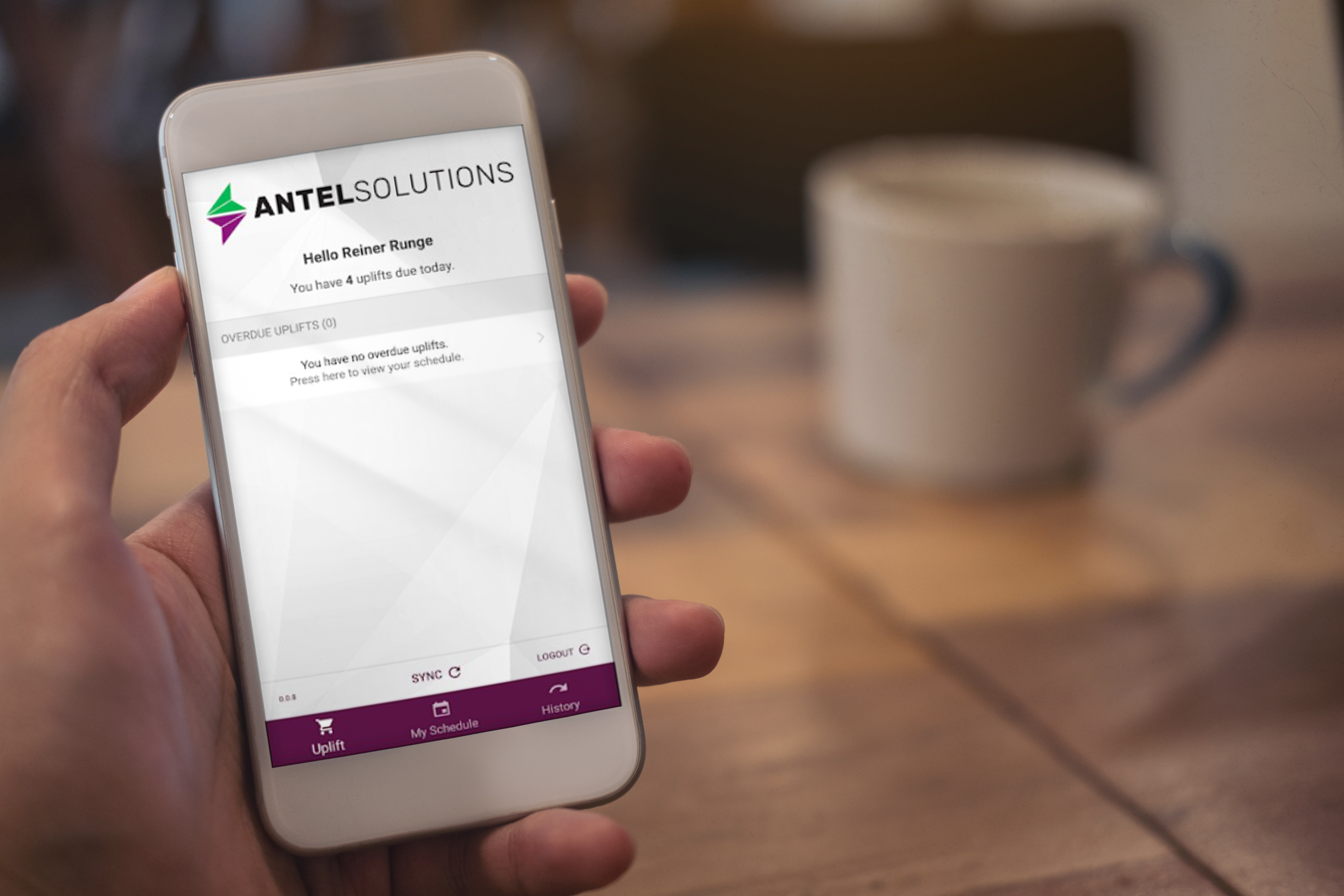
When carrying out the wireframing for the development of the app the following points were paramount in our specification and requirements. They were immediate information flow back, visual records of the customer claim, visual representation of the condition of the stock as well as GPS technology to tell the customer exactly where the uplift and the claim exchange were done. The app although simple in intentions is continually iterated and added to, dependent on the principal’s (our client and the manager of the distribution and disposal of the product) product needs. In this way, we can cultivate particular and product-specific processes for each situation. We will continue to iterate the process of the app to meet new technological and accessibility standards. We will make sure we are held to the most professional standards and keep our solutions careful and creatively best for each unique situation. A further iteration of the app has been the add-on of a track and trace facility. This has resulted in a stock system showing us exactly where all stock is at all times and giving us the ability to know what stock we have.
After some time using the app it became very evident to us that the collection of data in the Reverse Logistics processes carried out here could be used elsewhere. To date we have used it to explore and assist in promotional auditing, product recalls (showing the condition of the stock in-store), and any other activity that required urgent feedback to the manufacturer or brand owner. In this way, they can take immediate action and rectify any situation that can threaten brand equity. This kind of immediate feedback has other technological and data implications. Having the ability to analyze and report on this kind of data flow back could create the basis for artificial intelligence learning. This could be foundational in predicting activities around products, around stores as well as primary knowledge on kinds of products that have reoccurring events of damages resulting in returns.
Principal feedback to date has been that the information has been enlightening, valuable, and practical, especially for use on a day-to-day basis. It has also allowed our clients to identify product and packaging issues much earlier in the process than they would have been able to do in the past. Additionally, it has also given them an idea of what stock is around the country at any given time and this is especially useful to understand what product is reaching expiry dates, being recalled, and generally not meeting their image as a brand owner. It also gives them the ability to report back to their customers on delinquent activities from specific customers’ outlets. Also, it can catch potential product failures which have nothing to do with the quality of the product originally supplied from the factories.
We are proud of what we have accomplished in terms of service delivery. In my very first experience of backdoor, warehouse operations, I learned some curiously fascinating truths about designing active systems and standard operating procedures. When one looks at a process from an ‘aerial’ viewpoint, we can see all the required nodes of action to create a standard operating procedure. We assume that certain functions need to or will take place; for a transaction of returns, processed or damaged goods to exchange hands. But what we do not see, when we are separated from ground procedures are the cultures of these practices, the social exchanges, and securities in place we must preconceive to make sure that the system works. The warehouse is a place of surprisingly delicate social exchange that we must be cognizant of, as well as the technicalities of securing the needed data that comes from the exchange and movement of goods. Technology may be important in the advancement and role of Reverse Logistics practices, but getting people to invest and work with the system should and will always come first.
Technology has become the backbone of what we do: it has increased our own sustainability and responsibility in services we provide and thus the responsibility of the principal to their customers and consumers. We did this by understanding the landscape at all levels first and building a process that strengthens the foundation of these practices. The importance of cultivating a strategy in your technology matters, as it has the potential to uplift the very processes that make our practices so integral to the Logistics landscape.

Peta Goldberg as mentored by Anthony GoldbergAfter 27 years in the forward Logistics Industry, Anthony Goldberg started Antel Solutions as a way of bringing to the fore the essentialness of Reverse Logistics Practices. This was a concern as it was beyond the scope of the transport and logistics offering currently in play. Peta Goldberg divides her time between lecturing part-time at the University of Witswatersrand, Johannesburg, and the writing, scoping, and managing communications at Antel Solutions.