View From Academia: The Principles of Just in Time/Lean and Reverse Logistics
By Joe Walden, The University of Kansas, School of Business, SCM
Business Schools have a set regime of classes that feed into a degree in a wide variety of career fields. It is common knowledge in the textbook writing world that there is a lag between new concepts and their appearance in a textbook. This is tied to how often the textbook is updated and the lead time for the revisions to clear editing and becoming available to the students. Is this model sustainable and does it contribute to the circular economy and future trends?
I recently converted my textbook from a hard copy edition to an Open Education Resource. In simple language: the textbook is free to the students and anyone else that wants to use it through the Scholar Works network. The beauty of this option is that 1) The students get the book for free; 2) there is no old textbook to be resold, thrown away because it has no value or recycled by the conscientious few; and 3) it can be updated at any time to add new concepts and trends to the textbook to ensure the students get the most up to date education.
What does this have to do with reverse logistics and the circular economy to students in Colleges and Schools of Business? Everything. It provides an example of a concern for the environment and wasted resources and paper used to print a book. At the same time, it ensures that concepts can be updated at any time eliminating the time lag between concept and appearance in the textbook. The Reverse Logistics Association website states: “Our goal is to educate and inform reverse logistics professionals globally and be the voice of the reverse industry.” Our goal as educators is to extent that professional education to our students.
The Ellen MacArthur Foundation website gives us these insights into the circular economy: “Looking beyond the current take-make-waste extractive industrial model, a circular economy aims to redefine growth, focusing on positive society-wide benefits. A circular economy is based on the principles of designing out waste and pollution, keeping products and materials in use, and regenerating natural systems.” How does this tie to the principles of Just in Time and Lean?
The term circular economy is thrown around a lot in business and in the press lately. Before we try to link the circular economy and sustainability to Just in Time, we need to define what the circular economy is or tries to accomplish so we are all on the same proverbial sheet of music. The Association for Supply Chain Management defines the circular economy as: An economic system intended to minimize waste and maximize the use of resources through a regenerative process achieved through long-lasting design, maintenance, repair, reuse, remanufacturing, refurbishing, recycling and upcycling.”
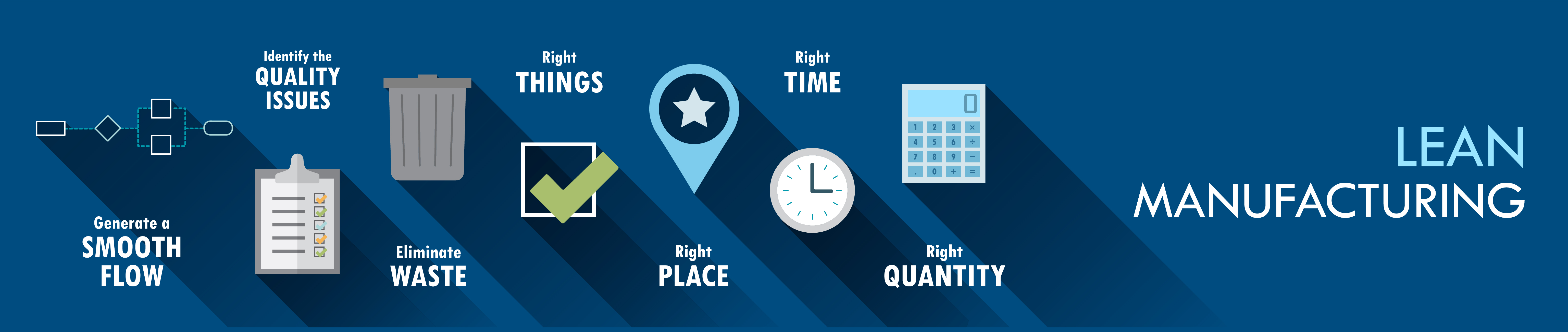
Just in Time, as we know it in the United States, is based on the writings of Taiichi Ohno and Shigeo Shingo and their discussions of the Toyota Production System. This gave us both Just in Time and Lean. The number one goal of both Lean and Just in Time is to eliminate waste. The goal of the circular economy is to eliminate waste.
Implementing the circular economy is one of the tenets of the Reverse Logistics Association. How do we eliminate waste in the circular economy using the wastes of Just in Time as a guide?
a. The waste of over-production. We have to forecast better the consumption of our products to prevent consuming resources that may not be needed and save those resources for future operations and products. Many of the components used in manufacturing are finite materials. Not producing excess products saves resources. At the same time, reusing components and materials through the circular process reduces wasting materials and components. This is just the opposite of the linear process or use-and-throw-away concept that has prevailed for decades. This starts at the initial phases of product design and process design. Can the product be made with recyclable materials and/or is it designed and made to be recycled rather than used and thrown away?
b. The waste of making defects. This impacts us all across the entire logistics and supply chain spectrum. Not only does this impact productivity and cost management, but it also impacts the circular economy. If the product has to be reworked, additional resources, materials, and energy is spent fixing something that should have been done right the first time. The waste of making defects also takes away from profitability. Making defects is tied to the training of our employees. Deming linked training and education to quality 60 years ago and yet we are still learning this lesson over and over. One of our needs in industry is to make sure our employees know what right looks like. Unfortunately, in some cases, we have done wrong for so long that wrong looks right. It may be time to walk the process again and document what we are doing and ask if there is a better way. Making defects also affects the reverse logistics process as we have to move the defective products back from the end-users to fix them or refurbish the products for sale in other channels. Better product design, better process design and quality control coupled with more quality training for employees will reduce the need to rework or return defective products and will result in fewer defective products finding their way to the landfills.
c. The waste of stocks. This is where the initial idea of zero inventories came from – although a bit erroneously as it does not mean no inventory. It does tie to the waste of overproduction. This waste of stocks results in products sitting on the shelves that do not sell. Now they to be returned for some credit adding to the already overburdened reverse logistics issues and depletes natural resources that could have been used for other products. If these overstock items were made from new materials that is a waste but even if they are made from components returned to the system through the circular economy, it is still a waste of materials and resources. And don’t forget the waste of having to inventory these excess stocks while they are collecting dust on the shelves.
d. The waste of waiting. At first glance, one would not consider this part of the wastes contributing to inefficiency or reduction of value for the circular economy. This waste may be a bit harder to quantify but, as the products are sitting in the reverse logistics pipeline waiting for disposition, there are components that could be returned to the system through the circular economy that may not be available to the manufacturing sector resulting in the consumption of new resources.
e. The waste of movement and the waste of transportation. These two are separate wastes in the Just in Time vernacular but for our discussion, we will link them together. Transportation assets are wasted when defects and warranty work products have to be moved through the reverse logistics pipeline. These transportation assets are becoming scarce. Using assets to move products unnecessary ties not just to defects but to the waste of stocks that we discussed earlier. Products that are excess to the needs of the end-users or retailers have to be moved backward in the supply chain. In addition to the waste of movement and transportation for these products is the waste of waiting – while in motion, these products are simply waiting to be processed and the circular components are not available for manufacturing to take advantage of and thus reducing the circular economy contribution to manufacturing.
As we continue to strive to adopt a circular economy, we need to keep in mind the need to walk the process and identify the wastes that are costing us money but not creating value in the circular economy. Just in Time is focused on continuous process improvement to eliminate waste. This same concept and methodology need to be adopted by industry to ensure that we eliminate those activities that are not contributing to the successful implementation of the circular economy and providing the sustainability benefits that come from reusing materials and components rather than simply throwing them away. The Reverse Logistics Association was founded with these ideas in mind and has continued to lead the way in the operations management field.
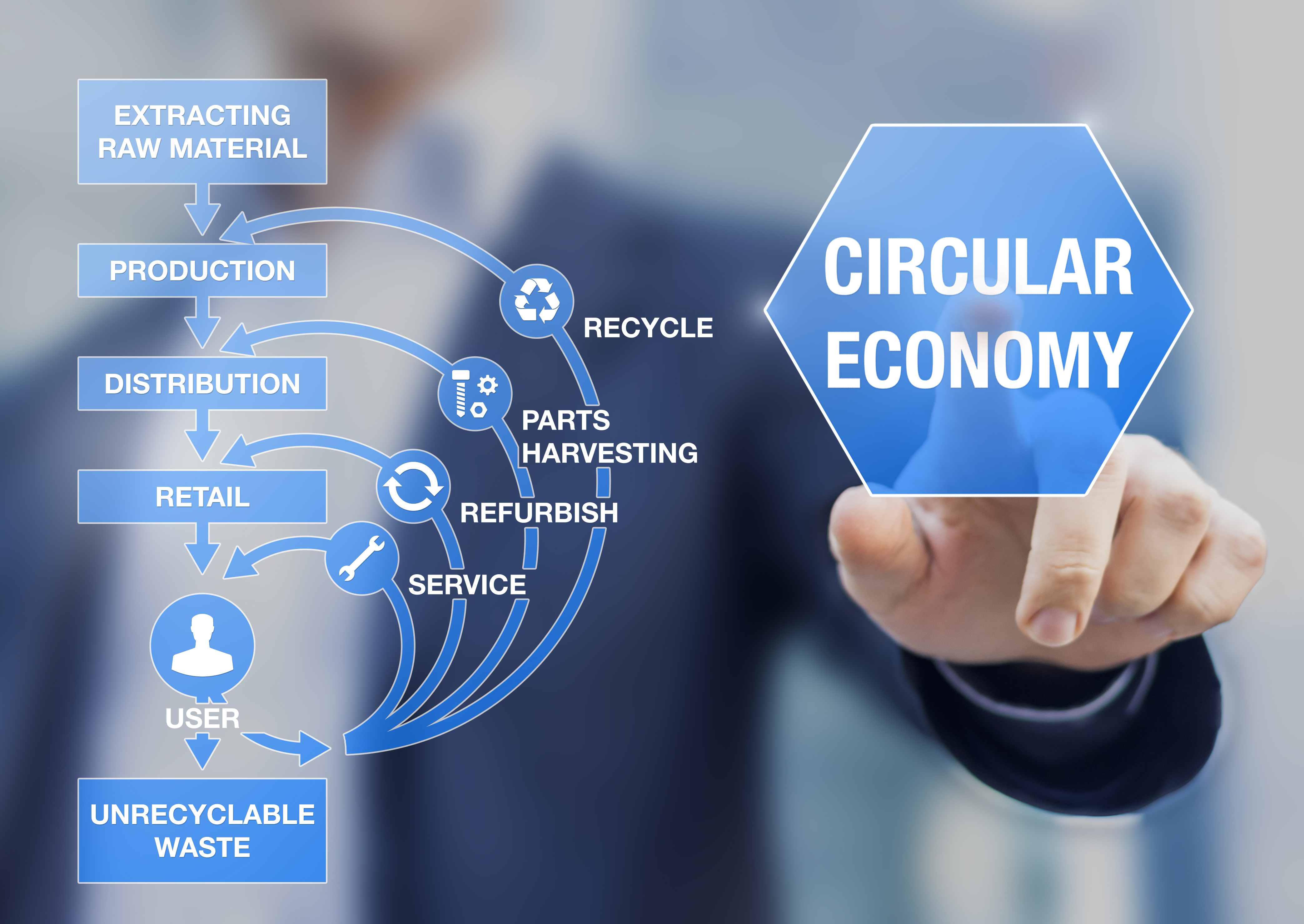
Joe WaldenJoe Walden has 40+ years in warehousing, distribution, operations and supply chain management. A new text book on supply chain management and operations management was released this summer. In addition to operational supply chain experience, Joe also teaches graduate and undergraduate classes in Operations Management for the University of Kansas. https://business.ku.edu/joe-walden