Electric Vehicle (EV) Batteries – A Circular Economy Opportunity
By Maria Kelleher & Samantha Millette, Kelleher Environmental
EVs (electric vehicles) generally refers to three categories of EV: hybrids (HEV), plug-in hybrids (PHEV), and pure battery electric vehicles (BEV).
Some hybrids (particularly the Toyota Prius for example) use a nickel-metal hydride (NiMH) battery and weigh about 100 to 200 lbs, depending on the make and model.
Plug-in hybrids and full battery electric vehicles (such as a Tesla or Chevrolet Bolt) use a lithium-ion battery which is needed to provide the higher power and energy density requirements. Plug-in hybrid batteries generally weigh 200 to 400 lbs, and the battery for a fully electric vehicle such as a Tesla can weigh up to 1,000 lbs.
The number of EVs on the road is increasing rapidly and is expected to grow significantly in the coming years. About 690,000 EVs were sold in the U.S. in 2018 (327,000 hybrids; 122,000 plug-in hybrids and 239,000 fully electric vehicles). Future EV sales projections vary widely but generally, it is expected that about 8% or more of US auto sales may be EVs by 2025.
As the number of EVs on the road increases, more attention is being paid to how to manage the batteries in these vehicles when they reach end of life (EOL). The recycling and re-purposing of EV batteries help keep critical materials (such as cobalt, nickel, manganese, and lithium) in productive use for as long as possible, a core element of the circular economy. The rapid increase in EV deployment globally will put huge pressure on demand for all of these critical metals and minerals, and recovering them from used batteries is increasingly seen as essential to meet future demands.
Warranties on EV batteries are generally 8-10 years of 100,000km, however, recent experience and reports suggest that EV batteries last a lot longer than originally thought, and a range of 10-20 years is suggested for California.
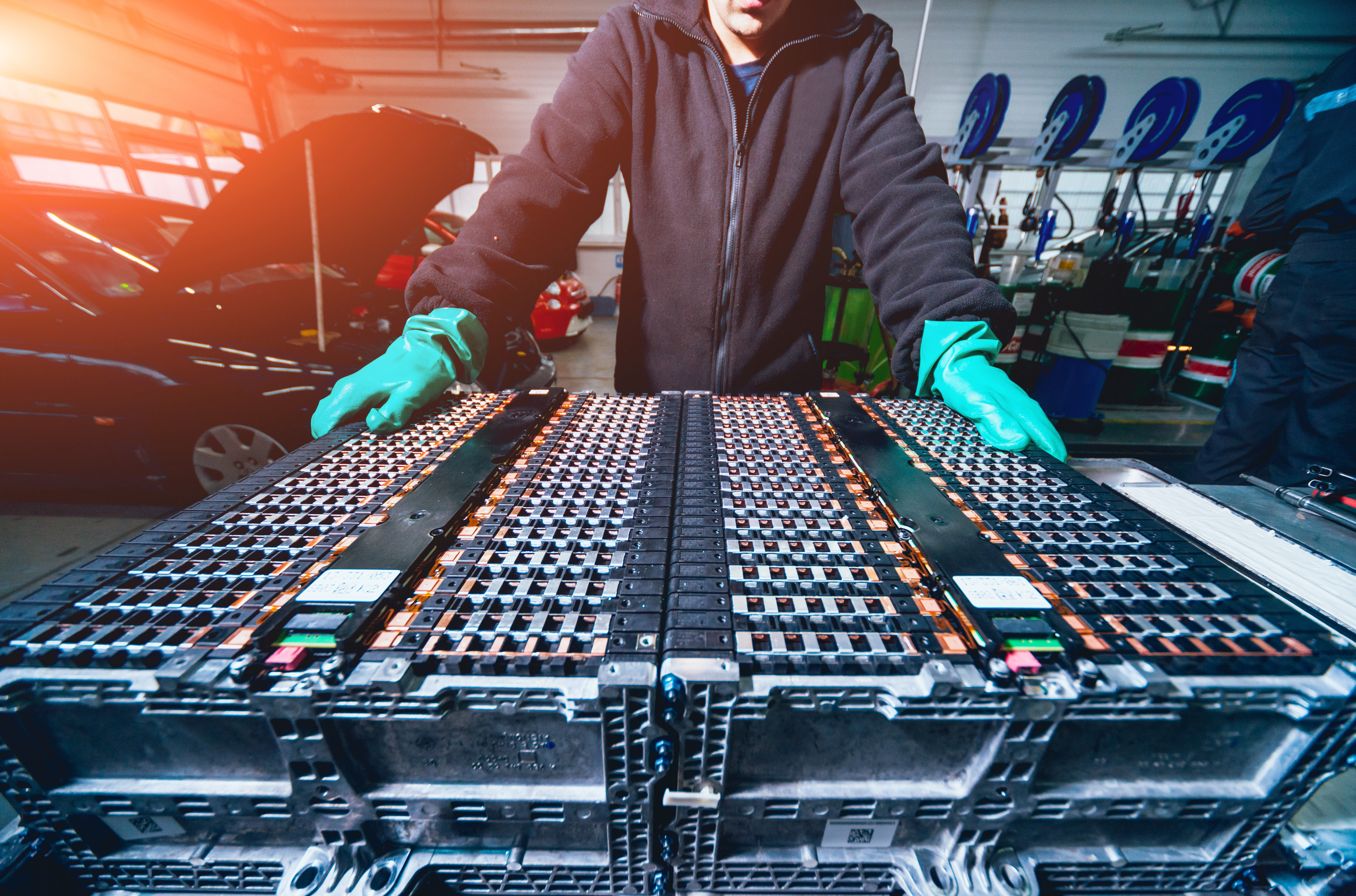
Some EV batteries will need end of life management through warranty or product failures before the 8-10 year window expected for most EV batteries, as well as through accidents and vehicle write-offs. While the numbers today are modest, they are expected to increase from significant numbers by 2030.
EV batteries are challenging and dangerous to handle at end of life, because they are very heavy, and cannot be lifted and moved without specialized equipment. Most important - EV batteries need to be fully discharged by trained staff before handling. They retain a significant electrical charge which can cause very strong electric shock and seriously injure a worker who has not received sufficient training on proper EV battery discharging and management.
Auto shredders today report that they are getting a few EV batteries now (mostly all hybrids), but the numbers are beginning to grow. The metal shredders apparently store the batteries for a while until a broker comes along and offers to take it off their hands, but the fate of the batteries after that happens is not clear. It is likely that the broker sells the battery on to someone who refurbishes them for the reuse market.
A study prepared for the American Petroleum Institute by Kelleher Environmental (with Millette Environmental and Gracestone) in 2019 estimated that about 525,000 EV batteries will reach end of life in the US by 2025 and over 1 million units will reach end of life by 2030 (based on EV sales data from 2000 to 2018 and sales projections to 2023). The table and figure from the study (presented below) show estimates of the number of batteries projected to reach end of life in the US from 2019 to 2030. The table and figure show that about 453,000 EV batteries are expected to reach end of life in 2021. Of this total, about 56% are lithium-ion batteries and 44% are nickel-metal hydride batteries. By 2022, when almost 550,000 EV batteries are expected to reach end of life with the number staying in that range until 2025. By 2030 over 1 million EV batteries are expected to reach EOL.
1 Table 1: Estimated EV Batteries Reaching EOL in the US, by Battery Chemistry (2019-2030)
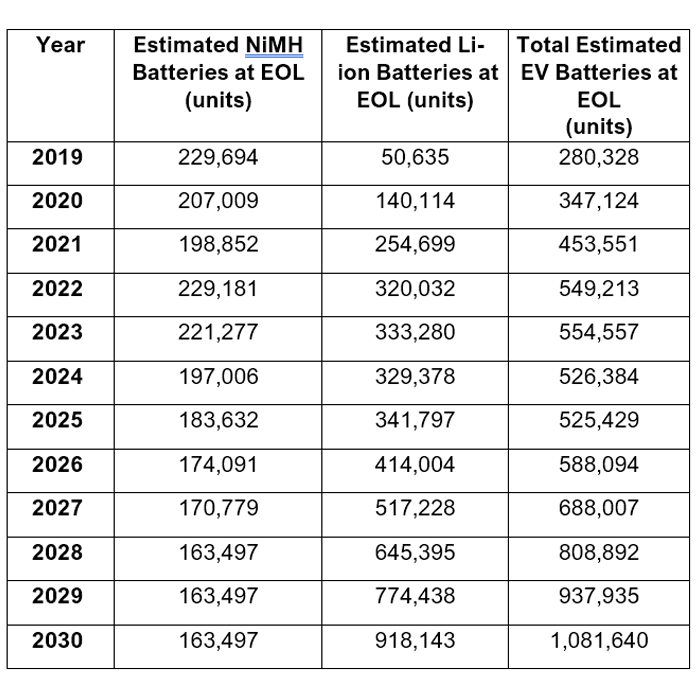
Options to manage EV batteries at end of life include reuse and recycling. While recycling is getting a lot of attention these days and is critical to recovering and preserving critical metals such as nickel, cobalt and manganese in these batteries, reuse is a preferred first option where viable, as it reduces the need to manufacture new batteries, extends the life of the EV batteries and cells and is more economically attractive compared to recycling at this time.
Reuse of EV Batteries
When an EV battery is no longer suitable for use in an EV, it still retains up to 80% of its charge and can be useful in many applications. The battery cells or packs, and even the battery management system (BMS) can be reused or reconditioned and sold into a secondary battery market.
Each EV battery has been exposed to different charging and discharging conditions during its use in a vehicle and therefore should be individually assessed to determine a suitable reuse application. This process involves diagnostic and screening tests to correctly identify the EV battery chemistries and designs.
Refurbishing EV batteries for reuse starts with partial disassembly of the battery pack. The state of health (SOH) of each cell and pack is tested and cells that are no longer working are identified and sent for recycling. Spiers New Technologies (SNT) of Oklahoma City is currently the largest company involved in EV battery reuse in the U.S. In addition to reconditioning batteries for clients such as Nissan, General Motors, and Ford, SNT also uses EV batteries to construct a number of products such as “watt towers,” which are a smart energy storage solution that can be the primary power source for residential and commercial applications. BigBattery is another major player in the US EV battery reuse business. With four facilities located in the US, Asia, and Europe, the company converts used EV batteries into new battery packs for emergency, portable and solar applications to provide power to houses in remote communities.
Recycling Lithium Ion EV Batteries – Cathode to Cathode or Direct Recycling
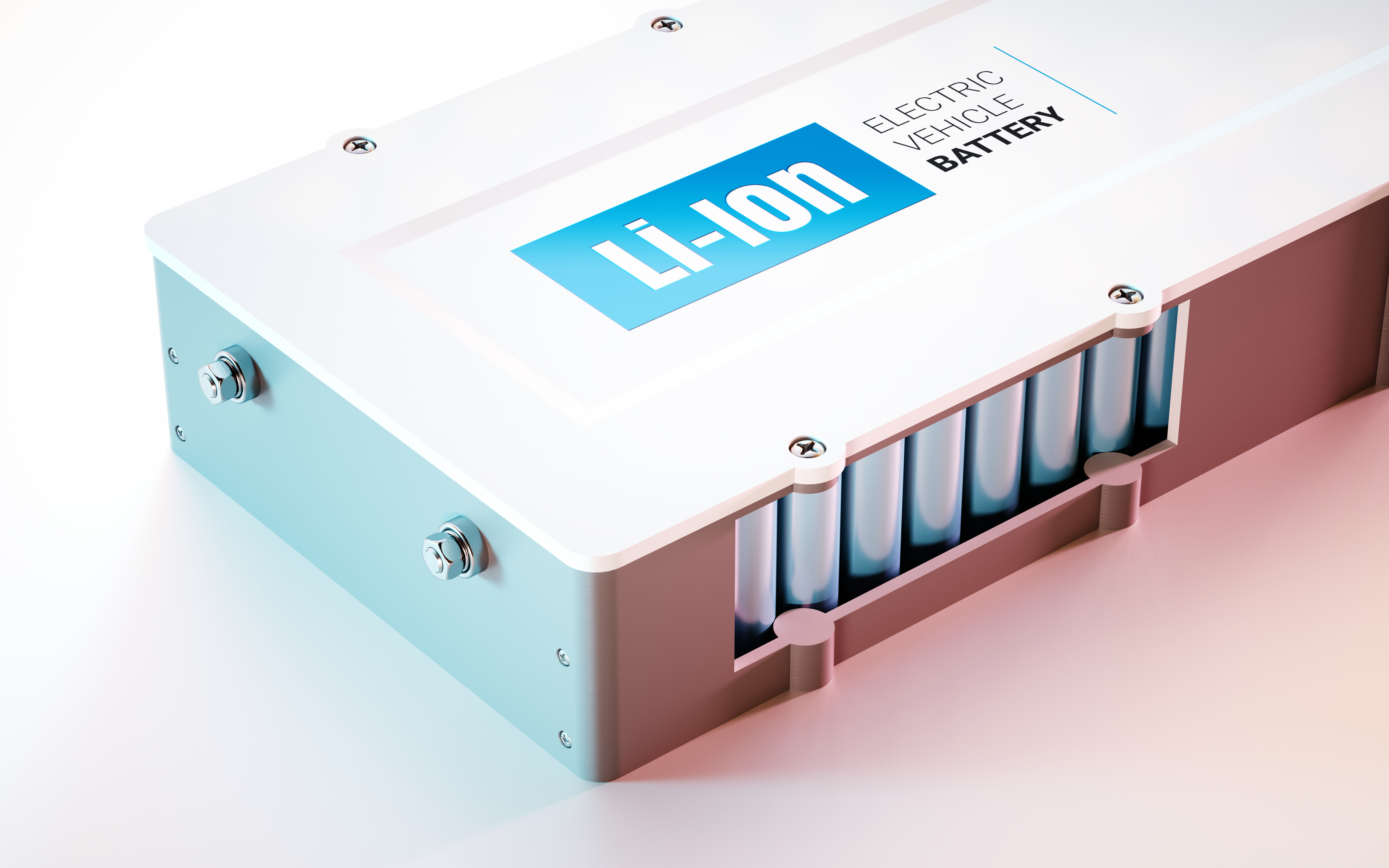
Lithium-ion batteries can be recycled by traditional recyclers such as Retriev who prepare the EV battery components and send various streams to large smelters to recover metals such as nickel, manganese, copper, and cobalt using pyrometallurgical (heat-based) processes.
New players are entering the EV battery recycling market to recover the battery cathode materials directly from the batteries through hydrometallurgical (liquid-based) processes which are less energy-intensive, and potentially produce an output material with a much higher value. This approach is referred to as “cathode to cathode” or direct recycling.
Li-Cycle is the best known and most advanced of these companies and recently opened a facility in Rochester, NY as part of their “hub and spoke” plan. The Li-Cycle Spoke 2 facility at Eastman Business Park (EBP) in Rochester, New York was fully operational by early December 2020 and produces up to 5,000 tonnes/year of an intermediate mixed battery material product (known in the industry as ‘black mass’) from all types of spent lithium-ion batteries. Their Spoke 1 facility in Kingston, Ontario produces an additional 5,000 tonnes/year of black mass.
Li-Cycle’s patented technologies are reported to be able to achieve recoveries of at least 95% of all materials found in lithium-ion batteries through an innovative, zero-waste process. This compares to the industry norm of less than 50% recovery. The company processes all types of lithium-ion batteries regardless of their previous application, chemistry, or state of charge.
Both Spokes will supply black mass to Li-Cycle’s future Hub, which will be constructed at Eastman Business Park in Rochester by 2022. Other companies working on lithium-ion battery recycling include American Manganese Inc., Neometals, and others.
Regulatory Developments
It is always worth noting what leading-edge jurisdictions do in terms of regulatory approaches to EV batteries to get a sense of what may be coming down the pipeline.
The EU released a new Battery Directive in mid-December, 2020 which significantly increases the management requirement on EV batteries, including tracking the battery through it first life in an EV, possibly a second life in for instance an energy storage application or as a refurbished battery, and eventually to recycling. By 2025 each EV battery in the EU will require the equivalent of a “battery passport” where the full life cycle of the battery is known.
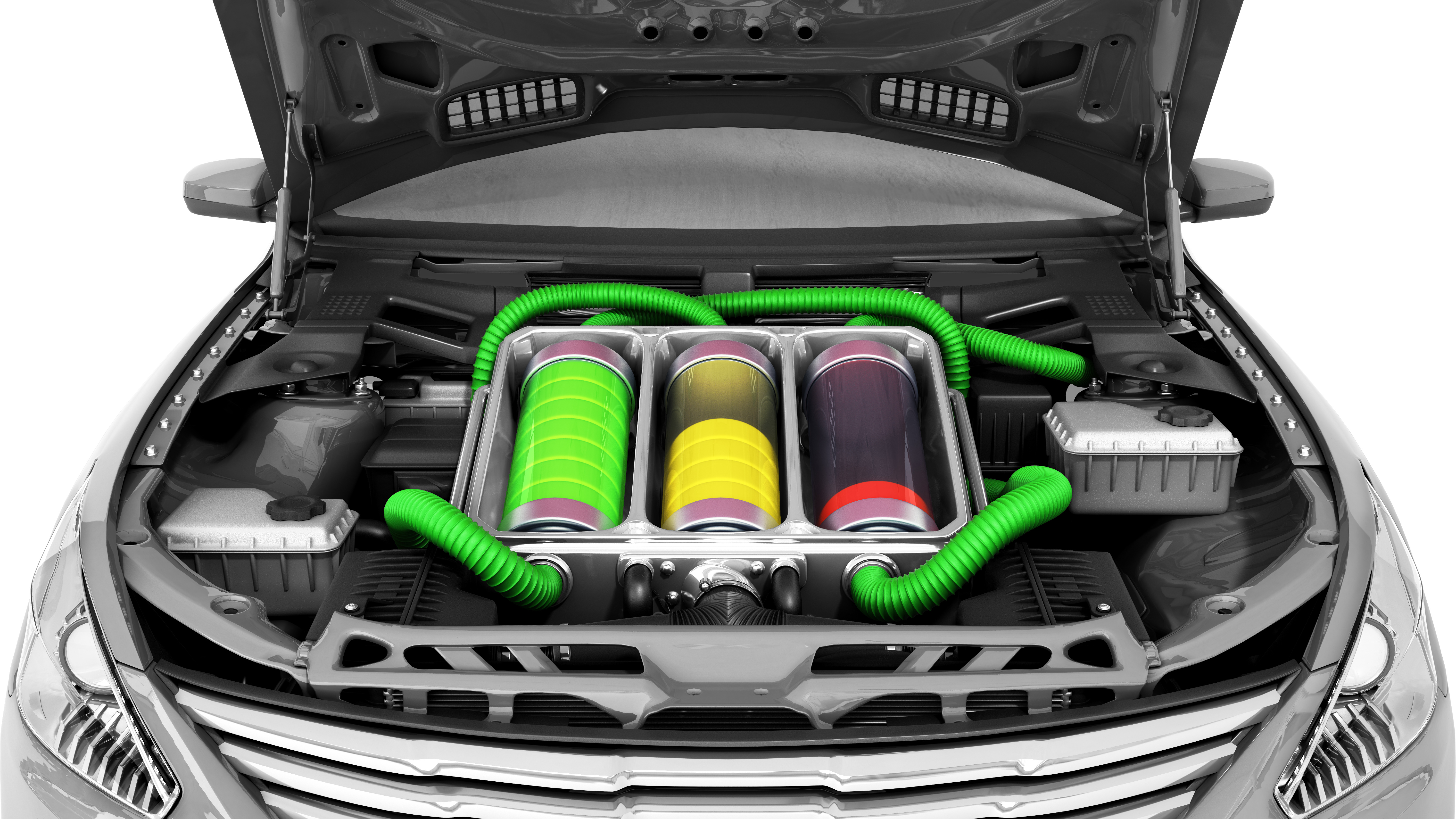
The California Lithium-ion Car Battery Recycling Advisory Group was created in 2019 in response to Assembly Bill 2832 (Dahle, 2018), to advise the Legislature on policies pertaining to the recovery and recycling of lithium-ion vehicle batteries sold with motor vehicles in the state. It is being led by the California Environmental Protection Agency (CalEPA), the Department of Toxic Substances Control (DTSC), and the Department for Resources Recycling and Recovery (CalRecycle). Members include representatives from the environmental community, auto dismantlers, public and private representatives involved in the manufacturing, collection, processing and recycling of EV batteries, and other interested parties. The advisory group will continue its work in 2021 and is expected to report back to the legislature in 2022.
Challenges with EV Battery End of Life Management
Currently, one of the biggest challenges to EV battery reuse and recycling is the logistics of getting small numbers of heavy EV batteries, which require trained staff to manage, moved from locations throughout the country to centralized locations for assessment and processing.
It is expected that this challenge will be resolved over time as the numbers of EOL EV batteries increase and scale can be reached.
1 American Petroleum Institute Research Study on Reuse and Recycling of Batteries Employed in Electric Vehicles. Report prepared by Kelleher Environmental in association with Millette Environmental and Gracestone Inc. Available at: https://www.api.org/~/media/Files/Oil-and-Natural-Gas/Fuels/Kelleher%20Final%20EV%20Battery%20Reuse%20and%20Recycling%20Report%20to%20API%2018Sept2019.pdf
Maria Kelleher & Samantha MilletteMaria Kelleher is principal of Kelleher Environmental (www.kelleherenvironmental.com), an environmental consulting company which is based in Toronto, Canada. Ms Kelleher has a Masters in Environmental Engineering and formed Kelleher Environmental in 2002. The company specializes in environmental research; recycling, circular economy and green energy policy development and evaluation, and green energy and climate change issues. Clients include national and state/provincial governments; industry associations and not for profit corporations operating in the circular economy.
Samantha Millette is principal of Millette Environmental (www.milletteenvironmental.com) based in Timmins, Ontario and provides environmental research support to a wide range of government and private sector clients.