In the face of increasing pressure to minimize waste and improve efficiency, the circular economy offers businesses a roadmap for developing smarter, more sustainable logistics practices. That’s not just good for the environment, it’s also good for business. Recent research from the National Retail Federation found that half of consumers are willing to pay more for sustainable products, and sustainability in the supply chain can support cost reductions, higher ROI, and increased brand value.
For the circular economy to successfully reduce environmental impact in supply chain management, businesses must look for ways to create lean processes and minimize waste at all stages of the product lifecycle. Technology systems play a key role in achieving this goal by collecting and analyzing material and process data to identify inefficiencies, product quality, process bottlenecks, and opportunities for improvement.
Understanding the Circular Economy
According to the Environmental Protection Agency (EPA), a circular economy extracts the highest value from an asset by keeping it in circulation for as long as possible, reducing waste, and improving efficiency. In logistics, this means creating a sustainable supply chain by extending the use of products and materials and recovering them for reuse or recycling at the end of their lifecycle.
Unlike the linear economy model, which flows in a straight line from raw material production to product disposal, the circular economy seeks to reduce environmental impact by minimizing waste and extending resource utility. Circular economy principles impact every stage of the product lifecycle including design, production, distribution, consumption, and product end-of-life.
Because the greatest opportunity for minimizing waste lies at the end of a product’s journey through the consumer landscape, reverse logistics is central to the circular economy. By prioritizing product repair, recycling, refurbishing, and other efforts to reduce environmental footprint, reverse logistics can capture additional value while meeting sustainability goals.
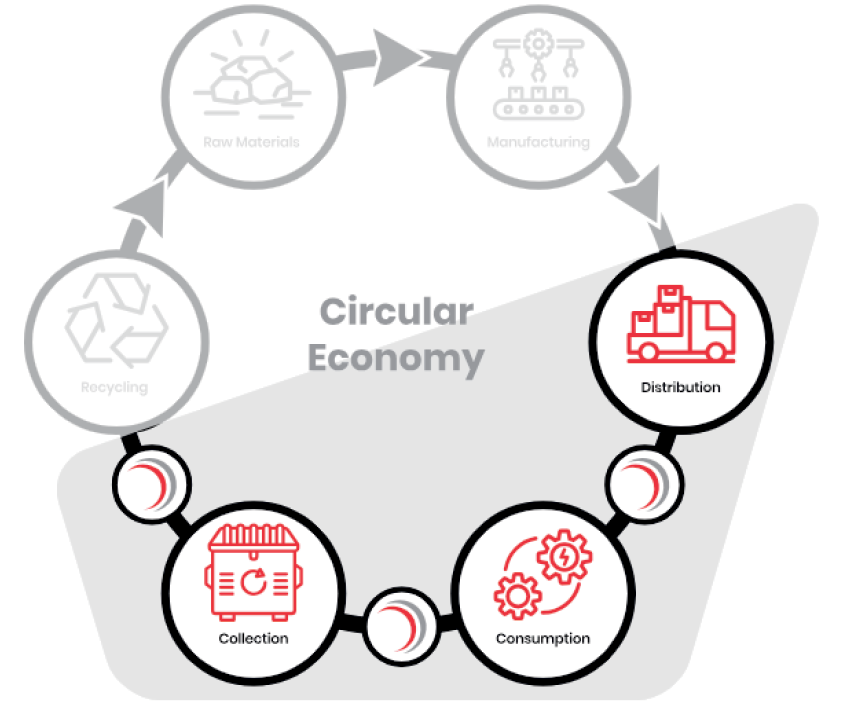
The Need for Specialized Systems
Sustainable reverse logistics operations require lean processes, efficient materials management, restorative or regenerative refurbishing processes, and a strategy to reduce or reuse waste. These goals can’t be achieved without systems that capture data, analyze it, and make it visible to managers and decision-makers. Intelligent systems support a successful transition to a circular economy with:
- Product Lifecycle Tracking - Tracking a product through every stage of its lifecycle provides critical data that can be used to evaluate sustainability during shipping, intake, repairs, refurbishment, resale, and waste management.
- Reverse Logistics Management - Reverse logistics workflows should be designed to improve efficiency, increase resiliency, and manage costs. Optimizing these processes empowers companies to reduce delays, manage returned inventory more efficiently, and streamline operations.
- Resource Optimization - Global resource scarcity has created an urgent need for materials recycling, sustainable processes, and efficient waste management. This starts with identifying problem areas and looking for opportunities to reduce, reuse, and recycle at every stage.
- Data Analytics - Data analytics is the engine that drives improvements in the previous three areas. Organizations need clear, accurate data that can be accessed in real-time to pinpoint problems and meet targets.
Key Systems Supporting the Circular Economy
From managing inventory and tracking materials to optimizing transportation and automating workflows, technology systems provide the foundation for sustainable practices. These systems support the circular economy and enable businesses to meet their sustainability goals while enhancing operational performance.
- Enterprise Resource Planning (ERP) Systems - Bring business operations together into one centralized system and integrate processes across departments. An ERP system manages inventory tracking, process automation, data management and visibility, demand forecasting, and more to ensure the effective use of resources.
- Warehouse Management Systems (WMS) - Streamline end-to-end warehouse operations including inventory management, resource planning, labor management, shipping and receiving, and cost control. Identify areas of concern and identify ways to automate or eliminate process bottlenecks.
- Transportation Management Systems (TMS) - Manage product delivery routes, boost transportation efficiency, and simplify freight tracking to reduce environmental impact. With real-time data visibility, a TMS helps businesses plan and optimize the transportation aspects of reverse logistics operations.
- Specialized Workflow Management Systems - Workflow management systems increase efficiency and reduce waste by automating processes, documenting and enforcing process adherence, and boosting data visibility. They integrate with other systems such as an ERP or WMS to facilitate faster, more effective decision-making.
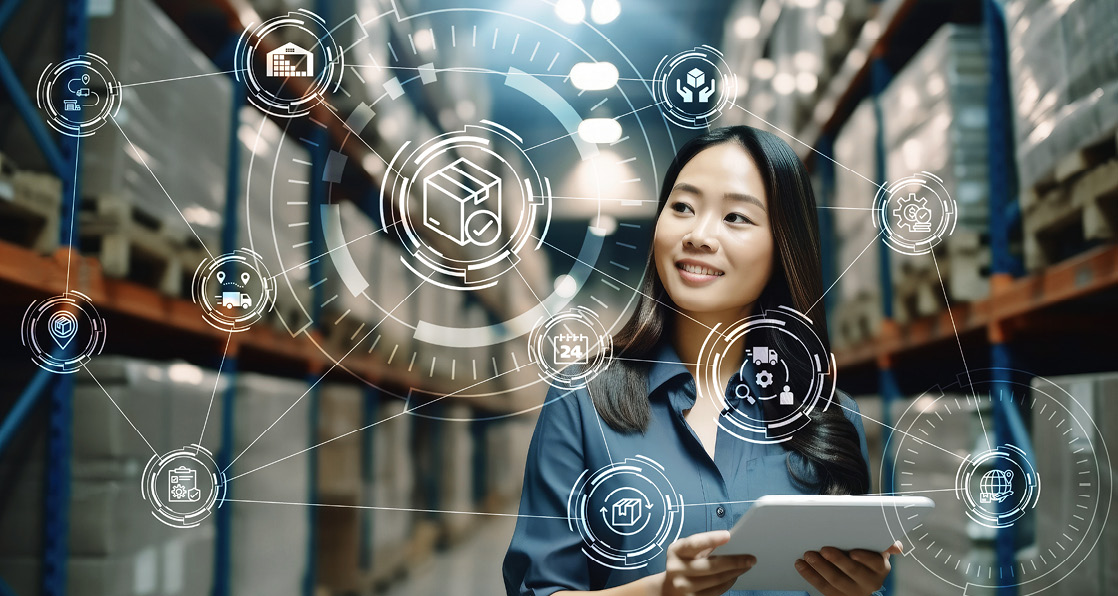
How Systems Boost Value in Reverse Logistics
Reverse logistics plays a central role in achieving the sustainability goals of the circular economy by finding ways to minimize waste and optimize resources. In pursuit of those goals, the right technology systems make it possible to collect, measure, analyze, and track materials and process data.
With this data, businesses can design dynamic workflows that get the most value from key processes, including:
- Returns management - Ensure a smooth returns process with shipment tracking and scheduling, process optimization, and increased visibility.
- Inventory management - Manage supply and demand needs more efficiently to reduce delays.
- Screening and testing - Screen products for functionality issues, product condition, and defective parts to streamline repairs and accelerate the returns process.
- Product disposition & grading - Assess and categorize products for disposal, return, resale, or recycling.
- Parts inspection (AQL/QC) - Track parts inspection processes and completed actions for greater efficiency.
- Repairs - Restore value with more efficient repairs management and process visibility.
- Unsold goods handling - Streamline returns, recycling, or disposal of unsold goods with detailed records on which products don’t sell, where they are coming from, how and where they are stored, and where they are in the process.
- End-of-life product management - Establish process workflows for recycling or disposal when a product has reached the end of its lifecycle.

Key Components of Effective Reverse Logistics Systems
Within the reverse logistics cycle, each process presents opportunities for greater efficiency. Technology systems capture and enhance those opportunities by integrating data and technology to ensure compliance, measure performance, and predict demand. To reduce environmental impact and make the best possible use of every resource, systems should facilitate:
- Centralized Returns Management - Managing returns in a centralized system supports cost reductions, better analytics, enhanced customer service, and real-time inventory management. This results in more efficient, cost-effective processes and happier customers.
- Advanced Technology Integration - Integrating systems (for example, an ERP, WMS, and workflow management system) breaks down data silos and improves decision-making. By bringing data from multiple systems into a single source of truth, organizations can make better decisions and more accurate projections. Integrated data is also critical as a steppingstone to future technology, including AI use cases.
- Efficient Inventory Management - To facilitate efficient returns, businesses need to know exactly which parts and products they have in stock. They also need to predict usage so they can trigger reorders before stock is depleted. Better visibility into process and materials data makes it easier to manage inventory, even with unpredictable returns volume.
- Eco-friendly Disposal Options - Eco-friendly disposal starts in the product design stage. Designing products for repair and with eco-friendly materials facilitates post-consumption refurbishment or recycling. Additional considerations include sustainable packaging, energy-saving operations, efficient transportation, and choosing partners who prioritize sustainability in waste removal and disposal.
Example: Dynamic Workflow Management Systems in Reverse Logistics
Managing the intricacies of reverse logistics can be costly and time-consuming, and they often cause clogs in the supply chain. Complex workflows and manual methods require extensive training time for new employees and may cause workflow bottlenecks, process delays, and inefficiencies. These niche workflows, although small, are often the impediments that hinder a circular economy. A workflow management system like WipIT from Triage Partners solves these problems with:
- A dynamic workflow engine - Instead of waiting weeks for a developer to reconfigure workflows, operation managers can make changes in minutes directly in the system. This makes it easy to optimize workflows, make changes without disrupting productivity, and capture and standardize niche operational data.
- Integration capabilities - Integrating with other systems brings all data together, increases visibility, and supports better decision-making. By integrating data across operations, businesses can gain visibility around throughput, replacement parts usage, inventory, test and failure reasons, and more.
- Real-time data capture - When data is available in real time, managers can make in-the-moment decisions in response to changes or problems. Real-time data also makes it easier to keep customers informed about the status of their return and to resolve process bottlenecks and delays.
- Scalability - Standardized processes and centralized operations management make it possible to quickly and easily scale and deploy globally.
Implementing a dynamic workflow management system increases the flexibility and sustainability of reverse logistics operations by reducing waste and improving resource utility. Real-time data visibility pinpoints opportunities for enhancing efficiency and increasing transparency, resulting in cost savings and higher ROI.
Case Study: Logistics Industry
Problem: A global 3PL faced challenges with the diminishing value of technology products that were shipped to repair depots and eventually returned to distribution centers. Unnecessary touch points and transportation costs impacted value to customers as well as productivity. Because their WMS did not support product, process, and operator accountability for complex workflow management, the company could not adequately track and measure labor and process outcomes.
Solution: The company partnered with Triage to gain deeper insight into process metrics using WipIT, a SaaS solution built for workflow management. Triage integrated WipIT with the company’s WMS to improve flexibility, scalability, and business intelligence around inspection, test and failure reasons, upgrades (revisions), serial numbers, labor productivity, replacement parts usage, and kitting materials.
Results: The 3PL increased the retention rate of returned products in the distribution center, reduced processing time by eliminating touch points, and realized cost savings. They also created a scalable model to standardize systems and expansions globally.
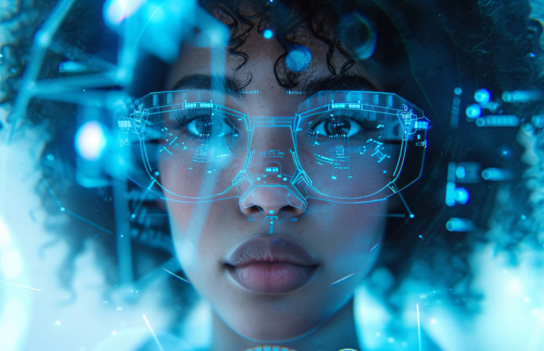
The Future of Systems in the Circular Economy
Reverse logistics is the key to reducing environmental impact and achieving sustainability in the supply chain. Whether a product is refurbished, its parts are reused or recycled, or it is responsibly disposed of, the right systems empower businesses to draw out the greatest possible value and benefit both for customers and for the environment.
As technology evolves, future systems will provide even greater support for the circular economy by increasing automation, collaboration, and analytics capabilities. In the future, we will see new value-add opportunities through:
- AI and Machine Learning - AI and machine learning have already transformed the way businesses interact with data, and will continue to create additional value in the future. The advent of generative AI also offers an unexplored landscape of potential applications for optimizing processes and minimizing waste.
- Internet of Things (IoT) - The Internet of Things is bringing us closer to a seamlessly integrated warehouse that extracts data from every process. Smart warehouses and tools like voice-activated picking machines and self-guided vehicles hold the potential to improve efficiency, reduce error, and optimize the customer experience through more sophisticated analytics.
- Blockchain Technology - Blockchain offers real-time tracking of physical products and locations, enhanced security, and process transparency. As it is implemented more widely, it will facilitate increasingly efficient circular economy practices such as product traceability, materials tracking, and waste management.
Ultimately, the evolution of technology systems will support better processes built on data-driven insights, not guesswork. These tools will simplify complexities, increase transparency, and identify greater opportunities to reduce, reuse, refurbish, and recycle throughout reverse logistics operations.
Conclusion
Sustainability is not an option for companies aiming to thrive in a resource-constrained environment. The circular economy is a strategic imperative, and the path forward requires innovative business technology that can pave the way for a more sustainable future. As the demand for eco-friendly solutions grows, specialized systems provide the infrastructure needed to reduce waste, enhance efficiency, and maximize the value of products and materials in reverse logistics operations.
As the Director, Business Development, Chris is focused on growing revenue and enhancing customer experience. Chris has more than 25 years in operations, customer and supplier management, and sales with Samsung, BlackBerry, ServiceCentral and 3rd-party service providers. Chris served on multiple CTIA RLSQ committees setting standards for the repair and refurbishment of pre-owned devices and is an active RLA.org member. When not working, you can find Chris enjoying the outdoors and spending time with his family.