Product Reworks and Overcoming Challenges with Cost and Complexity
By Jim Orrico, Dream to Product
Overview: Production mistakes are bound to happen. The problem is when the factory does not catch the mistake and a defective product lands in your warehouse. The high cost of shipping and lead times make returning the product to the factory is very costly and may cause losing customer orders. Reworking defective products in the USA is a great option, when the costs are manageable. In addition, certain defects require custom fixtures to fix and training of personnel. Jim will share specific rework experiences, solutions and insights that will help you calculate rework costs, tackle fixing complex defects, creating a quality plan and minimizing typical expenses.
Minimizing what parts are scrapped to save cost
A significant contribution to the overall cost of a rework are the materials being replaced. Scraping packaging materials and replacing with new tends to be a significant cost adder because these materials can be bulky and have to either be flown in from the overseas factory or purchased in lower volumes locally at a much higher price. Here are a couple of examples:
For a major power tool manufacturer, we were reworking a bulky tool with a large color printed box. A significant amount of glue was used to ensure box flaps remained closed. The glue caused permanent damage to the box when opening it. The cost for replacement boxes plus shipping from China was going to cost at least $3,000. We were able to save almost every box by using heat to soften the glue before opening the flaps. We created a custom box glue softening fixture with temperature controlled heating pads sold on Amazon for a total fixture materials cost of $170 (Reference Amazon.com, Keenovo silicone 400x400mm heated bed controller). This saved the customer a significant expense and helped the overall rework cost be more affordable.
For a high-end furniture brand, we were reworking one problem and quickly discovered another. There were stains on the stainless steel legs of the product. The stains were difficult to remove and not acceptable and would have resulted in scrapping 25% more product. We experimented and found the cleaner CLR removed stains on stainless steel that not even acetone could remove. This saved additional products from being scrapped; each product we saved had an MSRP of $600.
Utilizing low skill labor and temporary workforce challenges
Complex products are typically made on an assembly line with custom fixtures helping individual steps to be done efficiently by different people of varying skill levels. Reworking a product outside the original assembly facility poses challenges with the skill required. Communication with the original assembly facility gives the benefit of learning an efficient way to rework a product. Sometimes the design for fixtures can be shared and replicated without spending time designing new fixtures. Breaking down product disassembly and reassembly into component steps typically helps reduce the skill required because component steps are easier to train and remember. Work instructions should be written with pictures when possible and training conducted with the entire rework team.
Referencing the power tool rework, it required 5 different screw torques. We created color coded containers to put specific fasteners in and used the same color coding for each torque tool for reassembly. Utilizing fool proof tools like color coding can help a low/no skill worker be successful.
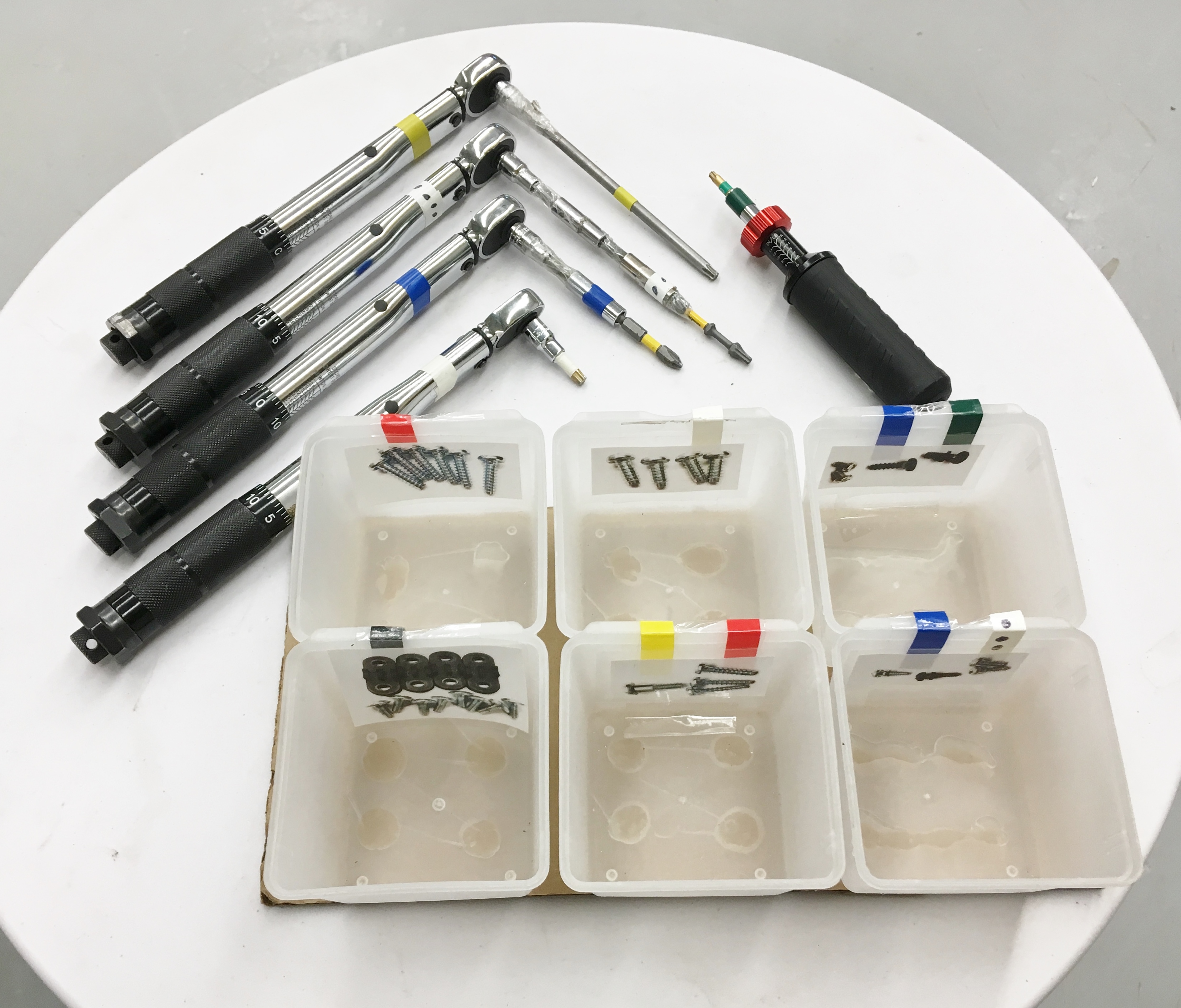
Oftentimes temporary workers ("temps") are used to help staff short term projects like a rework. Temps pose a challenge because there is no preexisting loyalty or track record indicating work ethic. Call-offs happen more frequently and randomly with temps. This instability with the workforce can cause significant delays to the timeline for a rework. Cross training helps reduce risk of a disruption with call-offs. The rework can continue with similar efficiency, even if the daily capacity is reduced.
Calculating rework cost
Calculating an accurate cost of a rework before it starts is extremely challenging. The customer always needs to know the cost ahead of time because they are making a rework versus scrap decision. The component steps to complete a rework need to be determined at the time the cost is being calculated. This allows time studies to be done with customer supplied samples. Beware of who is doing the time study. Initial time measurements tend to be optimistic because only one or a few products are being done by someone likely to have higher skill than the people ultimately doing the rework. Being transparent with the customer is critical because cost increases can happen for legitimate reasons. An example is a complex baby product we recently reworked. The customer kept requesting additional quality checks to be done, all of which added to the rework time. The additional time and cost was calculated and explained. The customer approved a cost increase because we showed how the time study was affected and shared our labor costs.
Expect the unexpected
There is only so much information that can be known before a rework starts. Often, the OEM does not know every single detail on how the product was assembled and other defects the factory may not have notified them about. Looking back at the many reworks we have done over the years, at least 50% of them had an additional defect not previously known or a known defect affecting a much higher percentage of the inventory. Referencing the baby product rework, there was a known secondary defect that the customer originally thought had an occurrence of maybe 5%. The instructions were to quarantine and scrap all units with that defect. After reworking the first few hundred units, we discovered the percentage of inventory with the defect was more like 40%. This would have resulted in scrapping $500,000 worth of inventory, a financially devastating loss. We suggested that the new hardware being used to fix the primary defect had unexpected features that were much less affected by the secondary defect (a happy accident). We designed and built a custom test fixture that impacted the product and proved that the secondary defect no longer caused a safety issue…saving the customer from loss.
Quality Plans and work instructions
Reworking a product opens up liability for both the OEM customer and the company performing the rework. Documenting the rework process and getting approvals before the rework begins is critical to address the risks. Dream to Product is an ISO 9001 certified company and documenting everything we do is part of our process. Generic quality plans are available online, but we would be happy to share our template. Please feel free to contact us.
Reworking is creative problem solving
No matter how many product reworks we do, every rework poses its own set of challenges and surprises. Creative problem solving is an important skill to figure out how to fix a problem economically. It is important to gather as many technical details about the product’s design as possible and speak with the original assembly factory. Although the factory may have caused the problem, they are still the experts and likely have good ideas on how to fix the problem. Tapping your in-house design team to help strategize a rework is also a great resource, if you have it. Alternatively, reach out to a company that has experience with reworks to get their thoughts, even if you don’t end up hiring them for the rework.
Our team at Dream to Product is excellent at strategizing and executing cost effective reworks. Our problem solving skills are rooted in design engineering and manufacturing of new products for our OEM customers. We have leveraged these product design and manufacturing skills to solve rework challenges, big and small.
Sustainable impact
As any member of RLA already knows, fixing a product instead of scrapping it has a net positive environmental impact. Considering the energy and resources consumed to make a product, the best thing we can do is keep using that product. Dream to Product has helped keep well over half a million pounds of product from going into a landfill. Our team is passionate about sustainability and the circular economy and we are proud of our rework accomplishments.
https://dreamtoproduct.com/rework-repair/
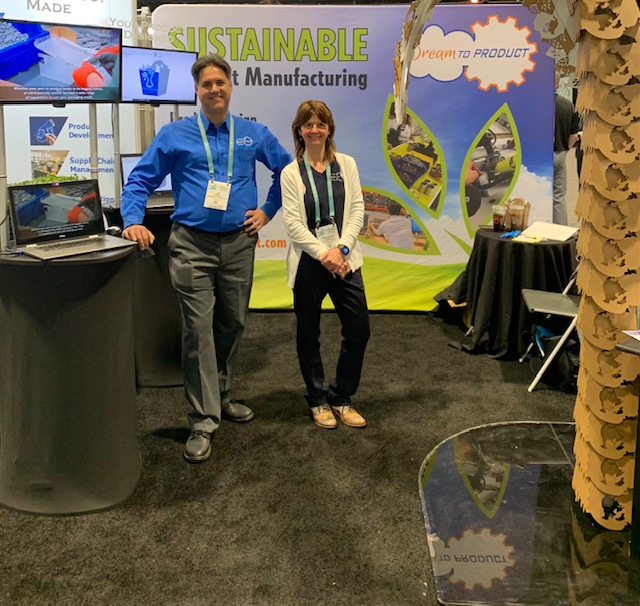
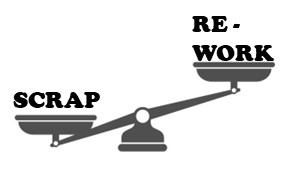
Jim OrricoJim has a mechanical engineering degree with 25 years of experience in new product development, manufacturing and supply chain development. He has launched innovative products for world class OEMs in industries including: medical device, housewares, office, cell phone, bicycle, fitness, power tool, LED lighting, hydroponic and water filtration. Dream to Product provides new product design, sustainable package design, manufacturing and rework services. Jim and his team love solving problems for their customers.