Repair and Refurbishment Processes and Differences
By Mateusz Lorczak, NKS-GROUP SP. Z O.O.
Repair is the act of making a product function work properly again after a failure. This mostly is done to avoid buying a new product. On top of that most modern world manufacturers provide limited warranty for their products. This includes as a standard practice repairing the products to its full functionality. Repair differs from refurbishment in that the repair usually doesn't include smaller-components to be exchanged in the repaired product. When doing repair we are trying to avoid replacing covers or coating of the product (unless those are causing problems with functions of the device).
For instance, when a car's radiator fan breaks, the repair shop would repair it by replacing the faulty fan with a spare one rather than replacing the entire radiator. Repair process doesn’t look at the cosmetic condition of repaired products, unless as mentioned earlier they are causing functional failures. Getting back to the example of a car if the car is scratched, standard in warranty repair is not covering removal of the scratches. A well-known approach of extending lifespan of products with preventive maintenance is very popular - especially in manufacturing sites and processes where failure of equipment or devices can cause serious delays in production. The predictive maintenance is then highlighting elements of the devices that are getting worn out with repair recommendations before the equipment malfunctions.
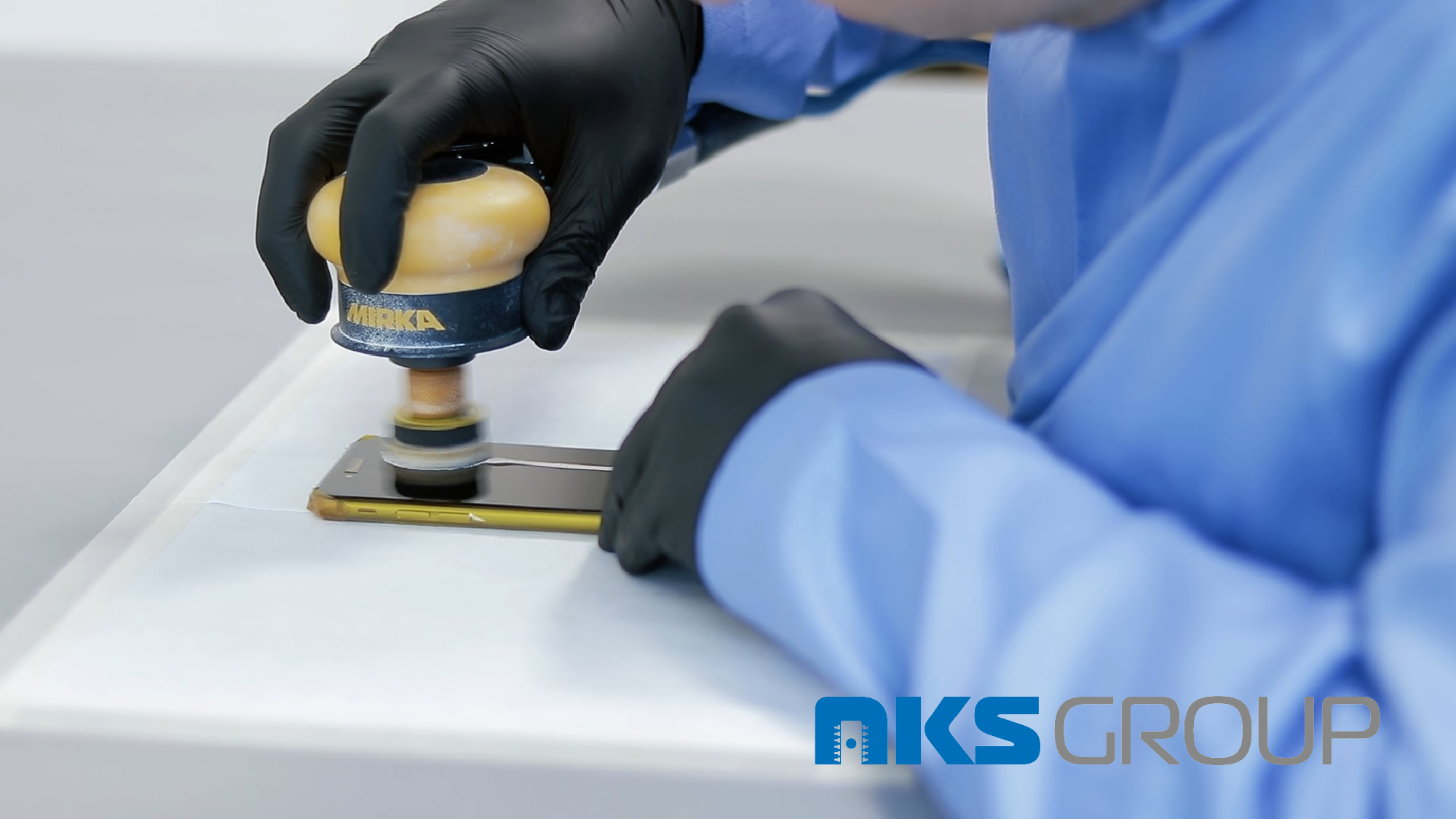
Refurbishment on the other hand is a process of restoring an object or structure by replacing worn parts (typically with brand-new or as-new ones), restoring the surfaces with polishing or applying new paint/materials on coating. This process usually occurs when a manufacturer or retailer is having a stock of returned goods or goods that were worn out during storage or presentation to customers. One specific type of refurbishment might be an upgrade, when the products are re-configured with different parameters, for example we increase the size of the storage drive in the computer or change the color of the covers in our mobile phones. From experience it’s visible that in house repair and re-paint activities are helping to reduce the cost of refurbishment significantly. Looking at the shortages in the market for spare parts and increased lead times this can be a game changer.
Combining those two operations into one - with Repair for devices done with Refurbished spare parts - will have a significant role in our rightful route of Circular Economy. Most of the carbon footprint and GHG emissions are already done when products are manufactured. If we are to exchange the faulty products with new products, it causes more damage to the environment than Repair and Refurbishment.
Typically manufacturers are providing a 12 months limited consumer warranty. There are exceptions to this rule, and also different regional legislation might be forcing manufacturers or retailers to extend the warranty length for example in European Union countries there is an obligation for manufacturers or retailers to provide 24 months warranty support to end consumers. If the product you purchased as consumer turns out to be faulty — or doesn't look or work as advertised — within the 2 years of the legal guarantee, you are entitled to get free repair of the product, replacement of the product, get price reduction on product or even cancel the contract and receive reimbursement for the full value of product.
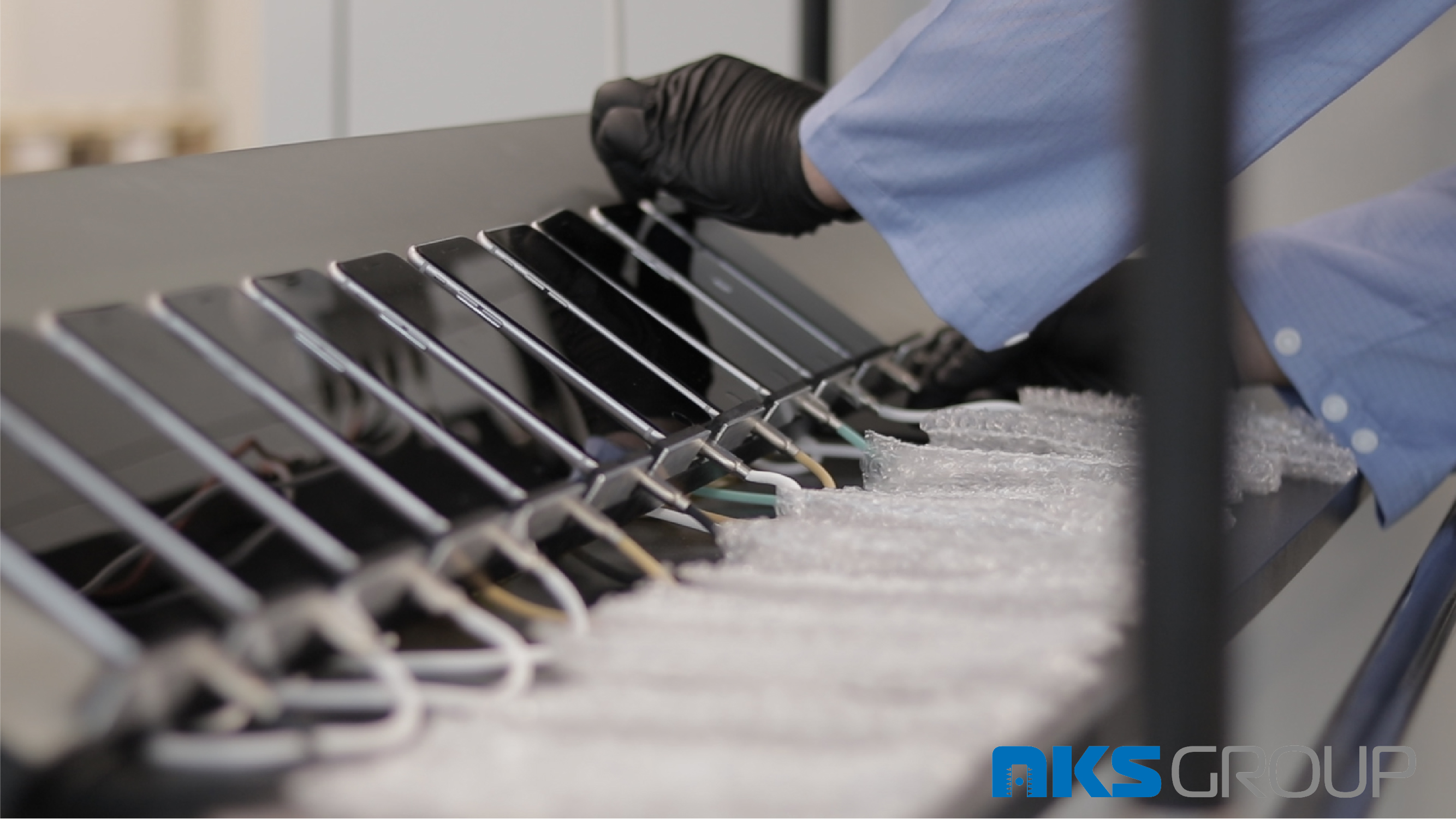
Additionally there is a need for manufacturers or retailers to ensure access to spare parts in case the products need to be repaired. Series of proposed Ecodesign regulations for sustainable products are expanding the manufacturers and retailers responsibilities. The new regulation will improve EU products’ circularity, energy performance and other environmental sustainability aspects.
What if the product is already out of its warranty period? We can then use the manufacturers or retailers repair network - those usually are done in the same repair centres that the warranty repairs are done in, but we need to expect it’s going to be charged (including freight cost if it’s applicable). We might also expect costs when trying to repair products that were damaged by accident - like the broken screen on our phone. In that event the customer induced damage is almost always chargeable. An insurance or extended warranty might be the best option for us in case we do not want to carry the risks of paying additional for repair of our products. Manufacturers and retailers are offering variou extended warranty options, as well as in cooperation with insurance companies they might propose you an insurance plan for your devices and their repair options in case failures or damages in the future.
Having all this information in mind we can rightfully assume that larger scale repair operations are insourced by the manufacturers or outsourced and contracted within the B2B service. The B2B contract is then between manufacturers or retailers and third party service providers that perform repair services. Those repair partners can be also responsible for making collections and customer interaction, if it's a part of the whole process design. The third party then acts in the name of the manufacturer or retailer to provide repair services to end customers. Central distribution of spare parts to repair centres helps the control of material flow and planning of materials like spare parts for repair.
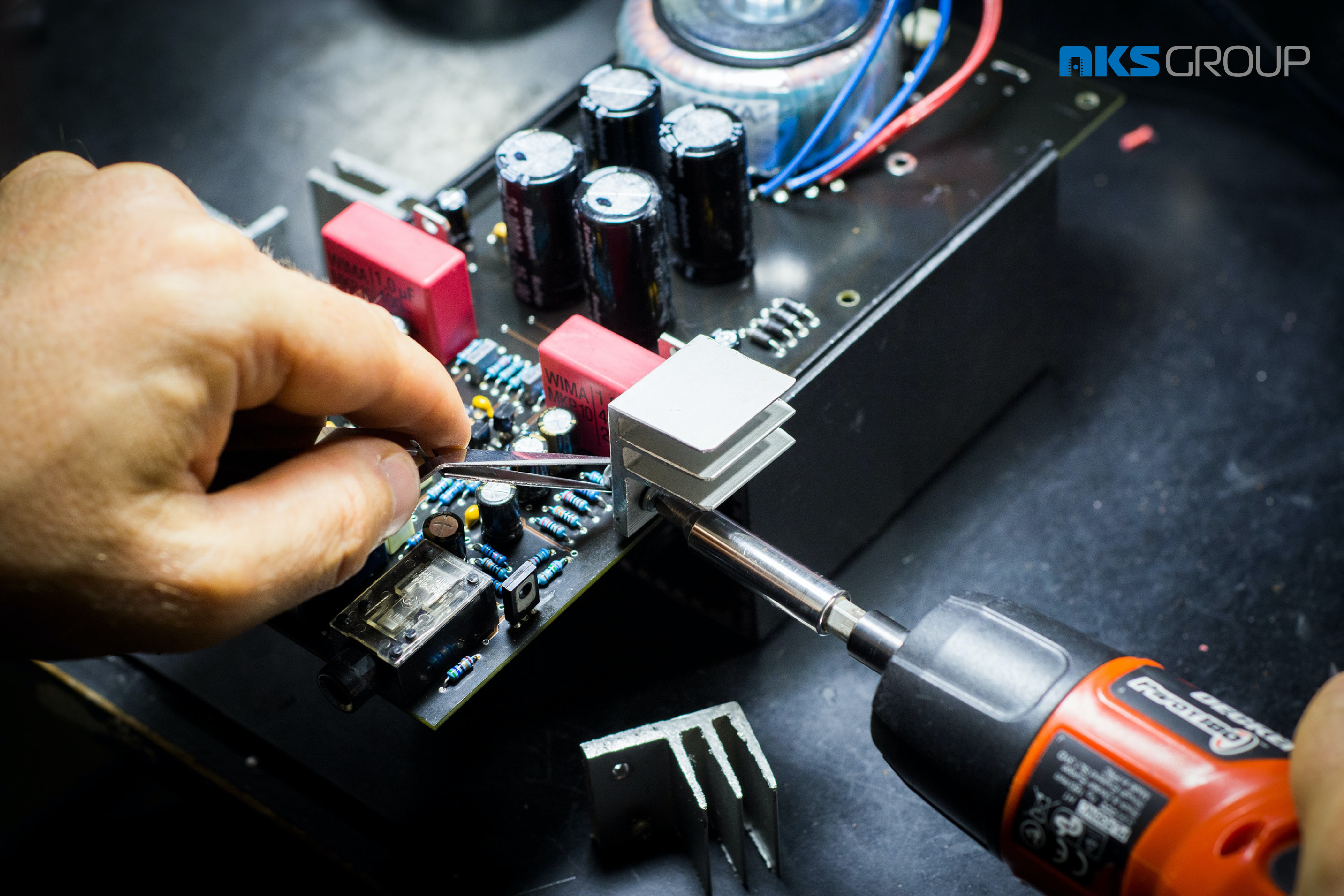
On top of the B2B side of the Repair activities happening in the market, there are a lot of “repair shops” offering services to end users - especially to those whose warranty period has ended. Those service points offer good prices on repair activities but might be limited with spare parts availability. In recent years also there is a high movement on options for consumers to perform repairs by themselves. As long as you have the right technical skills and access to spare parts you are able to perform the repair by yourself. These types of activities are a good reflection of the Right To Repair movement across the world, where organisations are fighting with manufacturers to have access to repair manuals, spare parts and possibility to repair the products by themselves with better design of products allowing the repair operation.
We can celebrate the International Repair Day on every third Saturday of October - this year it’s 15th October! The International Repair Day was established back in 2017 to highlight the importance of repairs. In 2018 the International Repair Day celebration focused on the #RightToRepair movement and its main objectives - access to information and resources needed for repair, need for products to be more durable and repairable.
So why does the market for repairing versus refurbishing items generate so much debate? The debate on whether to repair or refurbish items typically arises when an obsolete object needs to be replaced. For instance, some people don't want to replace an old TV with a newer model but do want to replace an old car with a newer one.
From an ethical perspective, repairing versus refurbishing an item involves minimizing negative consequences while maximizing positive outcomes. For instance, repairing an item may destroy original components. At the same time it’s helping to avoid replacing them with fake and counterfeit products. Therefore, those who value authenticity would most likely repair rather than refurbish their items when preserving originals is key.
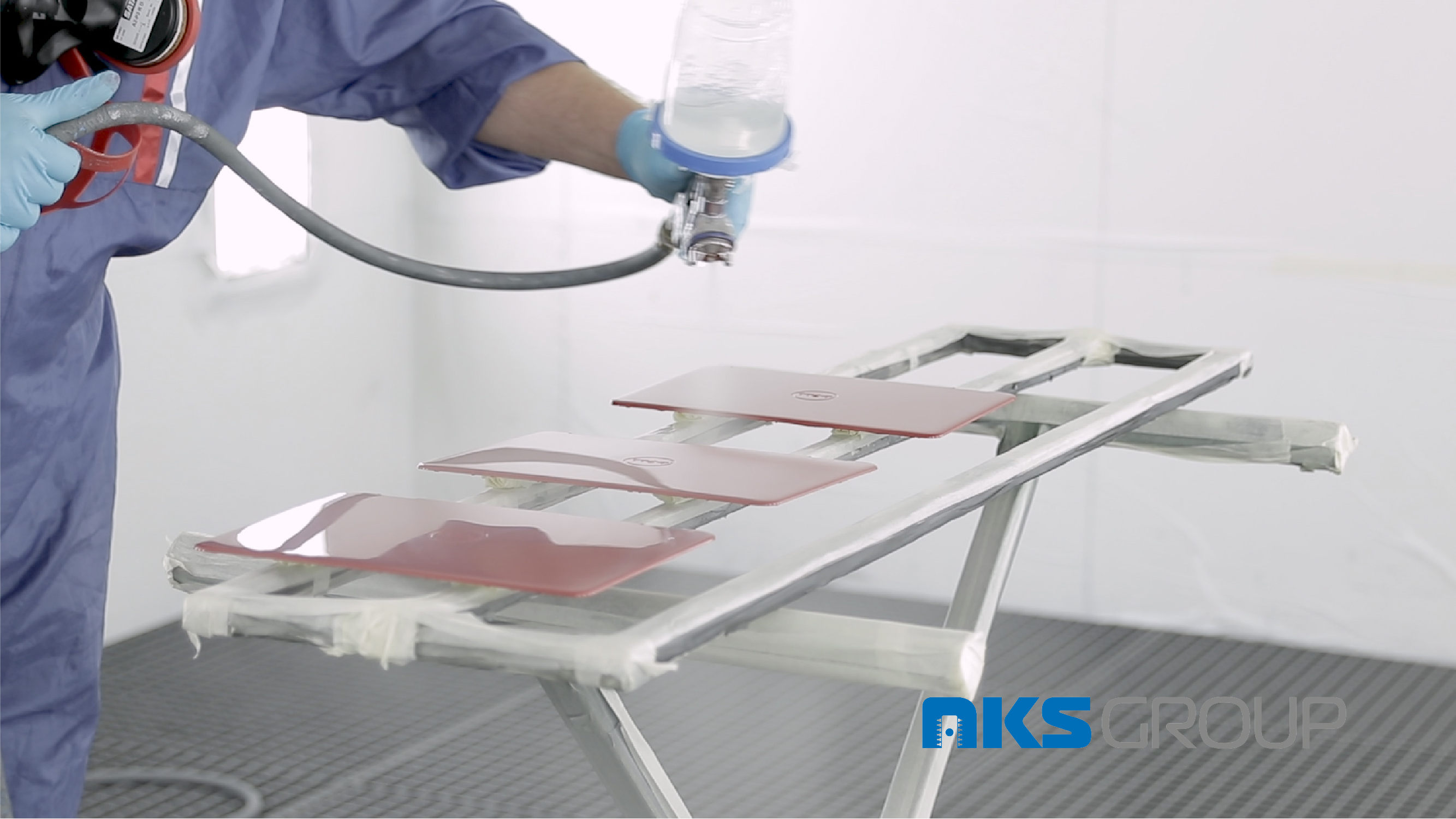
All the details bring us then to what is happening with products that are repaired and refurbished. Still the majority of the repairs done in B2B contracts are due to the obligation of limited warranty for products sold to end consumers. We can then clearly say that the item repaired is getting returned back to the same customer. This fact supports the rule of not repairing cosmetic failures, as it is exactly the same person who receives back the product after repair, so cosmetic condition is well known to them. In case of refurbishment - those products usually end up back on the market sold in stationary shops or online eCommerce offerings. The condition of the products should be marked as “Refurbished” or “As new”. History shows that often products after refurbishment are showing better durability as their testing process involves stress testing (also called burn-in).
Products repaired and refurbished are then two of many sources for products that are present in the secondary market. Whenever you have used a product that is functional you can resell it, recovering partial value of it. This doesn’t include goods like art when in time you might actually recover more value then you initially placed in the product, but it works like that for example for electronics, where when you want to exchange your product for a newer version you might resell the previous one in the secondary market. Secondary market is present in many forms, from online auctions, notice boards, friends and family contacts to end to end operations like manufacturer outlets or liquidation services sales. The choice is yours to use whatever channel is suitable for you.
Selecting the right partner for your repair, refurbishment and resell operations might have an impact not only to your financials but also to your impact on the environment. Keeping the products back in the life cycle is helping reduce waste and make more products ending up in landfills.
Mateusz LorczakMateusz Lorczak – NKS Group Poland sp. z o. o. an electronics screening and repair processes team member with 15 years of experience in process design and operational execution, customer interaction services and freight logistic support. Recently extending the interest in ERP and CRM systems from front-end and back-end Recycling and self-repair enthusiasts that always try to look "under the hood" of his devices, to find out how they actually work.