Mobile Warehousing and Storage Helps Solve Unprecedented Supply Chain Disruptions
By Sarah Johnson, Milestone Equipment Leasing
The pandemic’s extraordinary impact on the nation’s supply chain has created a historic surge in E-commerce. This seismic change affected reverse logistics as the volume of returned goods skyrocketed, driving up demand for warehouse space to store the influx. However, available traditional warehouse space was quickly consumed, leaving a critical need. Many companies have turned to mobile warehousing and storage trailers as an affordable, flexible alternative to traditional warehousing to solve this challenge.
As 2020 finally draws to a close and we reflect on the year – one that has felt 10 years long – there seems to have been a timeline drawn in mid-March that no one will soon forget. I can only think to define it simply as the “pre-pandemic” period and the “pandemic” period we live in now.
As the “pandemic” period unfolded and we saw what was happening around us, it quickly became clear the nation’s supply chain would be impacted. What we did not know at the time was how unprecedented and ongoing the level of disruption would be felt throughout the country and world.
Almost immediately, disruptions rippled through every link in the supply chain. Shortages of toilet paper, hand sanitizer and countless other essential goods dogged retailers and manufacturers. For consumers who did not typically spend much time thinking about transportation and logistics, the empty store shelves were a shock most had not faced in their lifetimes.
Shifting how product was packaged and produced rapidly without making extensive investments was not possible for many of America’s manufacturers. Then there were complications in the final-mile delivery network as it was suddenly taxed. Unavailability of many goods continue to date due to breakdowns at various points within the supply chain.
The lack of essential goods available in stores was compounded by the closure of many retailers’ brick-and-mortar locations due to the pandemic. More and more people started ordering the things they needed online – many panic-buying an unusually large number of items – and this rapid shift to E-commerce had major implications. Put simply, the surge in online orders was equivalent to months of Black Friday volume with none of the fun to go with it.
Understanding that online returns are higher than in-store purchases, it was only a matter of time before the significant number of goods moving through E-commerce would make their way into the reverse logistics process. Countless consumers who received their purchases months after they ordered them sent back these items in droves, causing a skyrocketing return rate. Manufacturing, transportation, inventory, operations, and consumer behavior were all out of sync.
Over at brick-and-mortar businesses, a different yet equally challenging problem was unfolding. During the early stages of the pandemic, stores froze in time. Spring goods remained on shelves while summer and Fall merchandise piled up in stockrooms. This resulted in a surplus of goods that these businesses needed to find storage for immediately. However, available warehousing was limited, expensive and quickly taken, while building of new warehousing was unable to keep pace.
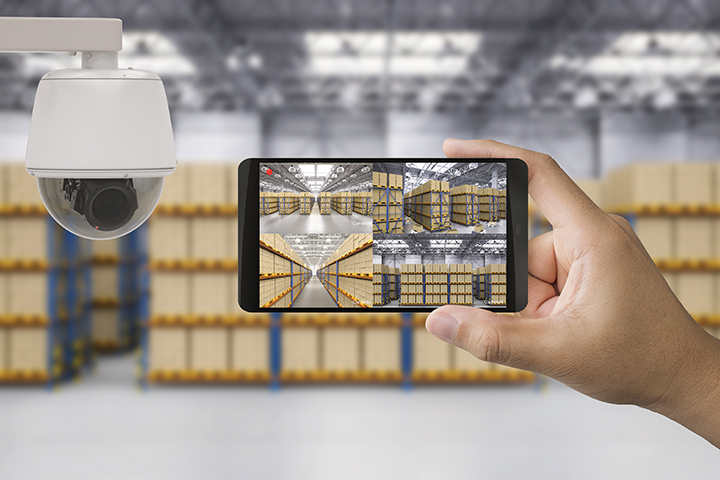
This created a critical need for fast, flexible, and affordable storage space during the pandemic. Many companies turned to an innovative and relatively new solution to meet this need: mobile warehousing and storage trailers. Companies that rent or lease these trailers for their reverse logistics needs found that this approach was beneficial in many ways:
- Obtaining mobile warehousing and storage trailers is more cost-effective than leasing warehouse space that may or may not be used and typically cost 50% less than the cost of traditional warehousing per square foot.
- Since mobile warehousing is delivered exactly when and where it is needed on-site and does not require long-term lease commitments, it allows companies to pivot quickly and put them in service to meet surges in demand to deliver these goods.
- Mobile warehousing and storage trailers give a company tremendous flexibility to store units at one location until they are needed at a different location without transferring of product into and back out of a storage facility is required.
- Mobile warehousing and storage trailers providers handle all maintenance and upkeep while all companies need to do is confirm availability of the trailer(s), sign the lease or rental agreement, show up at the lot, hook up and hit the road.
Thrift stores are an example of a business that especially benefited from mobile warehousing and storage trailers during the pandemic. With millions of people confined to their homes, 2020 became the ultimate spring-cleaning event. Although many were making donations, the thrift store outlets remained shuttered. When they finally reopened, items had piled up on the loading dock and needed to be stored on-site until they could be sorted and resold.
Because their retail fronts would remain closed for several more months and there was a lack of available warehouse space, thrift shops were looking for solutions. Mobile warehousing and storage trailers were the quickest and least expensive option because the trailers could be dropped off exactly when and where they were required. In markets where warehouse space was quickly dwindling and going for premium prices, there was a significant uptick in the use of these trailers.
Other industries that also realized a need for mobile storage during the pandemic included the big box home improvement stores. There was a backlog of returned items for home improvement projects at an unparalleled rate, causing companies to handle an increasing number of returns. Even before the pandemic, many were struggling to manage reverse logistics due to the Amazon “ship-on-demand” mentality.
As the pandemic shutdown situation continued to evolve over the summer, it brought a new set of complications. China had transitioned back to business as usual, and manufacturing plants were ramping up again. As goods came off the lines, freight was loaded onto ships and arrived in ports around the world. The pandemic caused peak season to occur two months early; however, brick and mortar stores remained closed, leaving the goods frozen once again.
A single retailer exemplified the issues many were confronting from this development. Its fall shipment of high-end athletic shoes arrived at a port from China; however, stores in the U.S. were still shut down. The cost to store the shoes on a shipping container was very high, so the company began looking for other options and its third-party logistics (3PL) provider chose mobile warehousing and storage trailers, which solved this issue while creating significant cost savings.
So, what comes next in our nation’s supply chain during the current “pandemic” period and, hopefully “post-pandemic” period? I anticipate disruptions to continue well into the future as supply chains undergo a transition as we better understand how the pandemic affects the flow of goods. Already some retailers are staging “pandemic pallets” to ensure availability of goods as equipment and resources will continue to be in short supply.
On the solutions side, logistics leaders are watching new technology in tracking and cargo visualization that will enable companies to maximize every square inch of useable space. Businesses will continue to adapt as employees slowly go back to work and a growing number of shoppers return to stores. Mobile warehousing and storage trailers will continue to be a valuable resource for to meet both storage and demand.
Sarah JohnsonSarah Johnson is executive vice president of Mobile Warehousing & Storage (MW&S) for Milestone Equipment Holdings, one of the largest and fastest-growing transportation equipment lessors in the U.S. Milestone operates a diverse fleet of over 91,000 trailers, chassis and containers through its nationwide network of 70 locations. For more information on MW&S and other transportation equipment solutions from Milestone, please contact us at 866-706-1144 or customer.service@milecorp.com, or visit www.milecorp.com.