Symphonization: The True Path to Harmonious Supply Chain Social Compliance Management
By Avedis H. Seferian, WRAP (Worldwide Responsible Accredited Production)
Introduction
WRAP (Worldwide Responsible Accredited Production) is the world’s largest independent factory-based social compliance certification program for the sewn products (apparel, footwear, textiles) industry. In June 2020, WRAP published a whitepaper entitled Symphonization: The True Path to Harmonious Supply Chain Social Compliance Management, which introduced to the world the concept of “symphonization” – a new paradigm to address the challenge of audit fatigue by having brands and retailers recognize the handful of credible and independent organizations that do social compliance audits as a professional service and create a menu of options that features those programs, instead of insisting on their internal, proprietary social compliance programs. This article begins with some excerpts from the paper’s Foreword, then summarizes the paper itself before concluding with a “what’s next” section that considers some possible implications for the reverse logistics industry.
Foreword
Good music is not made up of just a single note. And a whole chorus singing that single note does nothing to improve it. Beautiful music is a result of many instruments, each making their own unique sounds, playing different notes, but doing so in harmony.
Harmony is what those of us with roles to play in modern supply chains have been seeking for the past two decades, particularly when it comes to social compliance audits. While still a relatively young arena, the proliferation of codes of conduct has been exponential. Almost all brands and retailers deploy one, and many have their own internal programs to monitor them. They sometimes work with (but can often be separate from) other for-profit service providers, as well as several independent non-profit entities that provide compliance monitoring solutions. As a result, the industry has been plagued by audit fatigue. Multiple attempts under multiple initiatives have been made to tackle this. However, that harmony we all agree is needed, and we all so earnestly seek continues to prove frustratingly elusive. Experience suggests the core underlying reason is a fundamental misapprehension of the term harmony, a misapprehension with two components.
The first can be called the single-note fallacy, which has already been alluded to. Previous attempts to harmonize have typically involved a call to coalesce around a “let’s all just do it this one way” banner, the implication being that a single player/entity or a single standard has the “right” answer, with its champions telling everyone to do it that way and no other. Harmonization, under this approach, means everyone singing the same single note. But however noble the intentions behind such efforts may be, as the adage goes, “there’s more than one way to skin a cat” (or, if you want to cast it in apparel terms, “there’s more than one way to knit a sweater”). It should come as no surprise, then, that the single-note approach to harmonization has not worked. Its history is riddled with one failed attempt following another, so much so that the very term “harmonization” has now come to be a loaded one, carrying a lot of negative baggage.
The second component of the misapprehension can be called the locus fallacy, because harmonization attempts, even though ostensibly being about supply chain management, have tended not to think of the supply chain holistically, but to treat it as having one end in opposition to the other. Even if some attempts have made it a point of involving representatives from across the supply chain, they operate on the assumption that the “rules” are set at the buyer (brand/retailer) end and go upstream from there. Nevertheless, the truth is the underlying challenge is one for the supply chain as a whole, and as another adage has it, “a chain is only as strong as its weakest link.”
Harmony remains the goal we all want to achieve. But our past experience is proof that we need to find a better way to get there. Over the past few years, there has been some progress regarding both components, but we are still largely stuck in our old ways of thinking. Along comes a pandemic that has upended the entire world and how we do things, and in the spirit of never wasting a crisis, we have at hand an opportunity to re-think how we’ve been approaching social compliance management, recognizing the shortcomings and inefficiencies in the old ways. This paper proposes a new paradigm for supply chain social compliance management, one with that true goal – harmony – but with a focus on what it is actually about, and not the misapprehensions inherent in the past harmonization attempts. Harmony has, by definition, got to be a holistic notion, looking at the supply chain collectively (a point of particular importance as social compliance efforts are now increasingly expanding beyond the first tier). Furthermore, harmony is not everyone doing the same thing; it is different things being done in concert.
Turning back to the image of an orchestra, we see that it is not multiple instruments playing the same note. It is different instruments, being played differently by different people, combining their different sounds into a symphony. The path to true harmony is not harmonization as it has come to be defined by our experiences of the past decade and a half. It is, instead, symphonization (yes, that is a made-up word, but that is what we need now – to make up a whole new approach since the old one has failed) –a new approach to social compliance in the post-pandemic world, one based on a handful of specialized, professional, independent organizations providing a menu-of-options for the supply chain as a whole instead of having duplicative proprietary programs.
Summary of the Paper
Thirty years ago, as a result of industry exposés and a desire to quickly respond to worker rights abuses, many brands and retailers implemented new codes of conduct for their vendors, establishing baseline levels of workplace standards. Over time, the number of codes of conduct grew, and supply chain efficiency suffered, as manufacturers were subjected to multiple compliance audits by many different business partners. Realizing this unintended consequence, the industry began several attempts to develop one single social compliance standard under the umbrella of harmonization. These attempts, though well-meaning, were doomed to failure, and everyone continued using their own approach, resulting in no fewer manufacturing facility interruptions due to audits. The reasons behind those failures come down to the unrealistic expectation that a single solution will work for all and the non-recognition that the problem is one that involves the supply chain in its entirety. The struggles that supply chains endured during the first half of 2020 due to the global pandemic provide an opportunity to re-set our thinking and move beyond the limits of past initiatives. Instead of seeking harmony via the old mechanism of harmonization where the goal was to have everyone sing a single note, let us do so via a new approach, called symphonization, where we do not impose a one-size-fits-all mindset, but instead go with a menu-of-options approach, focusing on existing market options that best fit our entire supply chain needs. Symphonization is the path forward and envisions the supply chain as an orchestra of partners – a collection of instruments playing different notes, featuring unique performances, and making beautiful music in harmony.
The bottom line is that the previous way of doing things has not delivered the desired results. Seeking a one-stop solution for all social compliance needs and/or limiting solutions to only in-house resources is not sustainable. The supply chain of the future will need to be more flexible in order to be more resilient. Taking this approach may alleviate the stress and volatility resulting from global/regional/national/local events. In times of fear and uncertainty, there can be a false allure to solutions that reduce options and reduce variation. We need to resist this temptation and recognize the value of the menu-of-options approach at the heart of symphonization. This new approach to supply chain social compliance management will allow brands and retailers to be more efficient in the pre-competitive phase and thereby focus their resources on differentiating their products in the competitive market, all while driving toward better production capability and social compliance standards.
This begins by recognizing we are all linked together as a supply chain, and as the saying goes, the chain is only as strong as its weakest link. Insisting on doing things just our way to keep our particular link strong is self-serving and pointless. A single link does not matter alone; the whole chain needs to be strong.
The necessary steps to achieve this vision are for each stakeholder to accept a system they will be able to live with, rather than insisting on the one they would die for. It is all about responsible and well-coordinated business practices and increased traceability, transparency, and accountability across the entire ecosystem.
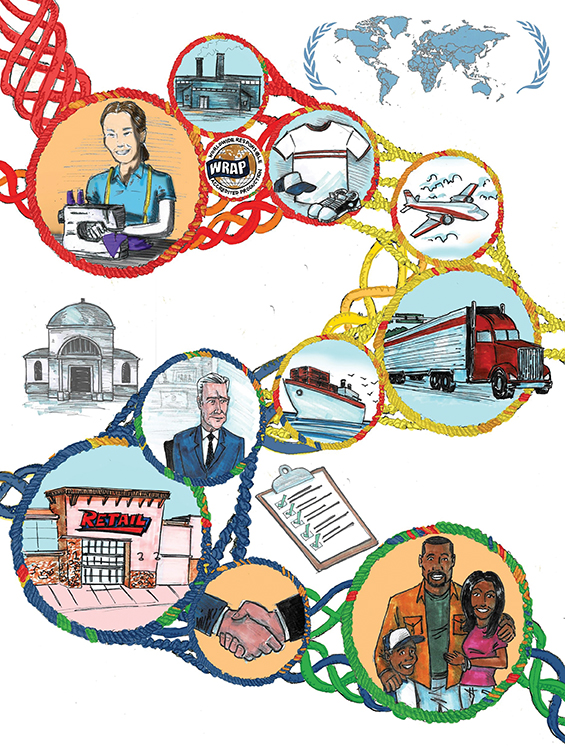
Recognizing that buyers are ultimately held responsible for their supply chain, symphonization also lends to an increase in the credibility factor. Buyers using their own programs are both judge and jury of which factories to partner with, ultimately acting as the fox that guards the henhouse. It is in the best interest of buyers to outsource the auditing of factories and use objective evidence-based reports to determine if factories are socially/environmentally compliant enough to place an order. Buyers will benefit significantly from the flexibility that symphonization will afford them by increasing the tools at their disposal to manage social compliance in their supply chains, including vastly enhancing their ability to go deeper into their supply chain. The abandonment of a proprietary compliance program should not be seen as a lessening of control, but rather as a means to free resources locked up in pre-competitive aspects to be used for competitive differentiation via brand-mission specific activities. By focusing more on the relationship building between them and their suppliers, buyers will be far better positioned to drive behavior on the issues that speak to the ethos of the company and make a difference to their standing in the marketplace. They can also thereby better understand their role with regards to the impact of their purchasing practices on maintaining social compliance in their supply chains.
By utilizing the menu-of-options approach at the heart of symphonization, buyers can move beyond the pre-competitive audit and go the extra mile on whatever issue may be most relevant to them in the competitive market. This will lead to improved supply chain management relations with the exact partners they desire.
The challenges we have had to endure these past few months have crystalized the value of symphonization. In the past, we were able to afford acting in our independent ways. The current state of the world has forced us to recognize that for the luxury it was and to see that that kind of inefficiency is no longer affordable. Now we truly see the necessity (not just the value) of doing things collaboratively. This pandemic presents an opportunity to re-set the supply chain social compliance management paradigm – moving away from duplicative proprietary programs to an approach involving a handful of specialized, professional, independent organizations providing a menu-of-options for the supply chain as a whole.
What’s Next & Implications for Reverse Logistics Industry
Symphonization allows each supply chain participant to begin playing music at their current level of social compliance and responsible sourcing understanding. As such, there is no specific first (or next) step – you simply begin with where you are and develop the appropriate menu of options (or list of specific resources) for what you are trying to achieve to be responsible sourcing partners or other actors within a supply chain.
The reverse logistics industry has developed a whole network of solutions over the course of its evolution to increase efficiency in handling product returns by looking at things like on-time delivery, efficiency of reverse shipments, and supporting movement by brands to on-line distribution. Given that the industry is not as consumer-facing as the retail space it services, its role historically with regards to social compliance issues has been relatively limited. But with the advent of increased transparency and modern consumer advocacy, that is changing rapidly and the importance of engaging on issues of responsible sourcing and sustainability is becoming clearer. WRAP is proposing that the industry uses symphonization as its approach to addressing this need. For the reverse logistics industry as a whole and any individual company in it – WRAP can meet you where you are now and offer the right set of expert resources to meet your needs or complement your services with additional resources as you grow in knowledge or expand to new markets.
Avedis H. SeferianAvedis H. Seferian, President & CEO, Worldwide Responsible Accredited Production (WRAP)
Avedis H. Seferian joined WRAP in 2004 and became its President and CEO in 2012. He has extensive knowledge of social responsibility issues within the highly complex worldwide supply chains of the apparel, textile and footwear sectors. A recognized expert in the area of social compliance and responsible sourcing, he often speaks on topics in this field at different forums around the world and has contributed to many leading trade publications and news outlets. Mr. Seferian is the Chairman of the Executive Board (and a member of the Stakeholder Board) of the Association of Professional Social Compliance Auditors (APSCA) and sits on the Impartiality Committees of several audit organizations; he also served on the Board of Advisors of the Alliance for Bangladesh Worker Safety.
Mr. Seferian began his career working for a business research and development organization before migrating over to legal research. Prior to joining WRAP, he was with a small law firm in Washington, DC. Mr. Seferian has also taught in various capacities in the business and legal arenas, including as an adjunct professor at the University of Maryland University College. He speaks five languages, has lived in four countries and holds three degrees from three continents - a Bachelor’s in Economics from St. Stephen’s College, Delhi University in India; an MBA from the American University of Armenia; and a Juris Doctor from the Georgetown University Law Center in the United States, where he was a Law Fellow and made the Dean’s List.
Mr. Seferian is a member of the American Bar Association and the Virginia State Bar. He resides in Fairfax, Virginia with his wife and their 2 sons.