Creating Unique OEM Value from Returns
By Linda Li,
Taking care of the logistical, compliance and industrial issues of deploying technology take-back initiatives can be a considerable barrier for brands seeking to do better. Leaders in Reverse Supply Chain Management (RSCM) today are providing technology brands with much-needed solutions to complex issues, but are also helping them turn cost centers into profit centers by dismantling obsolete technologies and re-purposing valuable components into new devices.
In the past, OEMs established return networks mainly as an obligation. Their customers needed a way to deal with returns, and it fell upon the supplier to make it happen. Now, returns and a reverse supply chain approach has become an increasingly important vehicle to stimulate new sales. The future of RSCM strategies is looking to be very different.
Suppose you’re on a road trip in your electric car. The way things are today, you would stop at a network of charging stations along the way. In the not so distant future, I think you will be able to stop at battery swap stations. The manufacturer will include battery packs with the car, but the car owner won’t own the battery. The battery will become part of the automobile’s service lifecycle. Similarly, with smartphones and other devices, consumers may not even own the device in the future. Customers may use a phone for a year or two, and then return it back to the carrier, swapping the device for a new one.
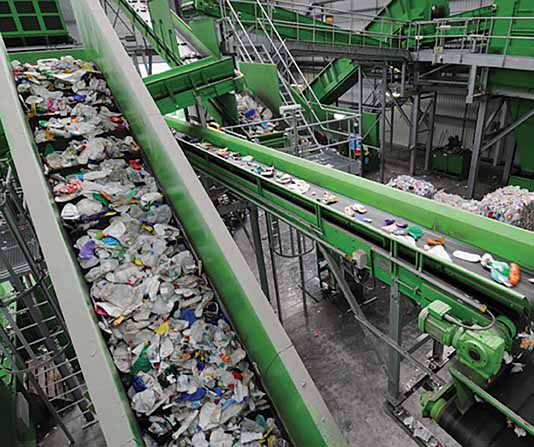
Instead of having to process the return or customer take-back as an end-of-life liability — something that the OEM is obligated to deal with — the return is becoming an integrated part of the value chain as an asset. This returned asset and its components are now essential for stimulating new product sales and increased customer loyalty. It’s important for OEMs to have a very streamlined, efficient, high-service-level return, take-back or after-market service platform.
Looming Opportunities
Historically speaking, post-consumer return, take-back, or after-market services are expensive because of the need to deal with individual pieces and transactions. Whereas, post-industrial reverse logistics are at the component and materials level, facilitating easier processing, but in North America, there is not a lot of post-industrial reverse supply chain capabilities, because the supply chains weren’t established. But this is changing. A lot of the OEMs are moving parts of their manufacturing, at least the high-end processes, back to North America and the U.S., in part, because of government incentives.
With the return of more manufacturing in the U.S., we’ll no doubt see a rise in demand for post-industrial reverse logistics and reverse supply chain services. There is an excellent opportunity for companies in integrating post-consumer and post-industrial reverse supply chain platforms together. This will provide a level of cost savings and efficiency that you typically would not get with just the post-consumer side.
The strength of an effective and profitable RSCM program lies in the depth of its engineering expertise. Engineers must consider the aftermarket value for devices, the primary market value for component parts such as screens, switches, and chips, as well as the recycling value of metals, and extract the usable elements for repurposed through a partner network. Remaining non-usable parts are disposed of via highly regulated, compliant systems.
Eliminating Parts Shortages
As with the tragic tsunami that hit Thailand in 2004, there can be drastic disruptions to the global supply chain. In the case of the Thailand disaster, the entire global supply of hard drives was disrupted for several months. Supply chain disruptions are very costly to an OEM, and even an entire market.
Imagine if OEMs instead had programs in place for harvesting components from older-generation devices. With a process where the device is properly de-manufactured, harvested components — such as hard drives — can be reuse and repurposed as a back-up supply for repairs and other uses, providing a level of protection against the fluctuation of global markets.
This strategy could turn reverse logistics or reverse supply chain into a profit center, it represents real money savings. The parts harvested from older-generation devices, have already been paid for, they don’t need to be paid for again, just pay for the service to harvest them out of the device. If a company were to smelt the entire motherboard from an older-generation product, there would be little to no financial recovery, depending on the precious metal commodities market. But if an SSD is harvested and reused, for example, that’s a gain of about $20 U.S.
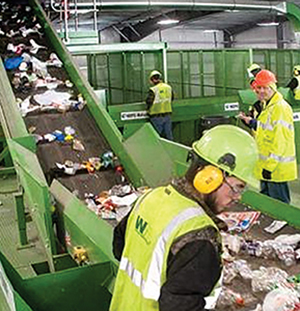
Reverse Logistics in an IoT World
Because IoT devices are so highly integrated — not your traditional PC or laptop — they are very small and difficult, if not impossible, to take apart. If the device is broken or defective, the whole thing has to be taken back.
When it comes to properly managing a reverse supply chain or reverse logistic service for IoT devices, it’s important to note that most IoT device manufacturers are smaller OEMs, perhaps even start-ups, and it’s costly for manufacturers of this size to design and deploy their own RSCM programs. It is not economical nor efficient for small OEMs to build their own reverse logistic network. I’d strongly suggest that smaller OEMs partner with established RSCM providers and leverage their knowledge, experience and existing, omni-channel take back platform.
A good RSCM partnership will allow the IoT device OEM to focus on what they do best — designing innovative products and getting them out the door — while also delivering a return service that their customers demand, and fulfilling compliance obligations.
The Circular Economy
Rather than return devices directly to their raw material state, a proactive approach to both Post Industrial Recycling (PIR) and Post-Consumer Recycling (PCR) efforts called closed-loop reverse supply chain management, can dramatically increase the value of end-of-life technology.
Traditionally, electronics and high-tech manufacturers have used conventional recycling methods as a means to dispose of end-of life technology. These methods of recycling are called cradle-to-grave or downcycling where the process degrades the quality of materials over time, eventually resulting in waste. This process, while effective for returning technology to its raw material state, is extremely environmentally taxing and can be a burden on the bottom line.
Closed-loop recycling reduces the demands for raw materials to produce a new product by using cradle-to-cradle or reusable materials harvested from end-of-life assets/surplus inventory and strategically introducing them into the forward supply chain.
img4
RSCM and Brand Value
OEMs are releasing new products at a faster rate than any other time in history and older models are subsequently reaching the end of their life at a much quicker rate. On average, between five and seven percent of a typical OEMs annual shipment volume becomes obsolete before it is sold or reaches the consumer. Through RSCM, OEM’s can harvest parts and components from these obsolete assets and excess inventory and inject them into the manufacturing networks of new products—eliminating waste reducing manufacturing costs.
The leading technology brands on the planet win by providing their customers with a brand experience that extends beyond hardware, UX and support, but also extends to what happens once the product needs to be replaced and recycled.
Well planned RSCM programs provide confidence to the brands and the consumer that the product will be taken care of in the most responsible way possible and that valuable components will not simply be destroyed or sent to landfill, but re-used in a progressive and intelligent way.
Strong RSCM programs enable all companies to deepen their customer relationships, strengthen their organizational and culture initiatives, maintain the highest levels of compliance and even turn a profit. It’s a win-win for the brand, the customer and the environment.
Linda LiAn expert in the field of green supply chain management, Linda Li has more than 10 years of experience in M&A strategy and corporate development in clean tech and TMT. As executive director and Chief Strategy Officer at Li Tong Group, Li pioneered the company’s world-leading, closed-loop recovery solution for mobile devices. She is also responsible for devising the company’s corporate growth strategies and leading global initiatives and implementations. Prior to her current appointment, she held senior positions in Fortune 100 electronics OEMs as well as in management consulting and private equity. Li earned a Master of Engineering in supply chain management from the Massachusetts Institute of Technology/ZLOG and a B.A.Sc. in biomedical engineering from the University of Toronto.