Business Benefits by Return Channels in Reverse Logistics Strategy
By José Antonio Valles R.,
Abstract
Products purchased by the customer, after being used and discarded, can be used as raw material in the manufacture of other products through reverse logistics strategies.
Returns may exist in the use of purchased products, generating the client return these to your supplier for repair or to be replaced by another. Such situations create a distribution chain from customer to supplier and manufacturer it generates benefits to the company.
Keywords: business benefits, return channels, reverse logistics strategy
Introduction
The management of the flows of products that have been used and discarded by the customer or end user, and which were developed for the various forms of products and materials used in industrial production processes. This situation affects the entire product life cycle, since being used and discarded quickly, may have caused shortages of some raw materials, not having rapid provisioning and can also produce concentrated in time of waste generated increases.
Reverse logistics is a form of logistics, where the flow of materials from the customer to the producer, is defined as the process of planning, implementation and control, efficiently, at optimal cost, is the flow of products from the point consumption to the point of origin, ie the manufacturer uses this process in order to recover the value of the materials or ensure proper disposal.
Reverse logistics considers the collection and transportation of used product from the end user to the producer, including the processing of products returned in new usable products. Manufacturer seeks the following objectives:
Collect used products in order to incorporate them into a new value chain.
Separate the components or materials of returned products.
Sort and / or mixing of components or materials to integrate a large volume and be able to carry an economic cost.
Carrying components or materials into intermediate treatment processes or retreat.
Give intermediate treatment, for example, washing, granulating, and filtration, to prepare materials for reprocessing processes.
Process to return the material for reuse, either repair, recycling or reconditioning. In the reverse logistics may involve various stakeholders, developing different functions that can be linked to direct flow.
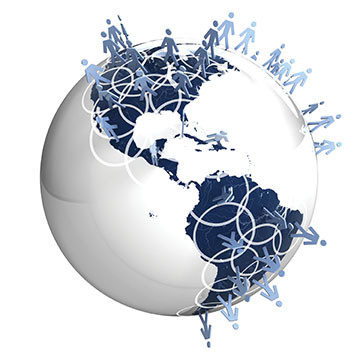
Development strategy
Return Channel has a function in reverse logistics, this is known as a return channel and is determined by products, the products are introduced to reverse logistics flow, and you can see the following string types return:
Quality products that the seller has removed from the catalogs.
Goods out of use where the producer puts its products in occupied spaces competitor’s products, this helps the seller since incurs no costs for changing supplier, for example, a clothing supplier clothing acquires its competitor and agreement with the seller who offers its product only.
Seasonal merchandise products that have reached their final sales period. Here the retailer can sell products at a discount or retrieve its value using the reverse logistics process.
Products with excess stock market returns, That is, there are quality products that the company has in excess but continues selling and moving products to other retailers or in stores in shelters sold.
Products with defects. The defects can be discovered by the vendor or the customer, a notice to the producer and according to agreements entered is compensated retailer or end consumer with a new product or refunds your money.
Falsely defective products. This situation happens when the client does not read the operation manual therefore considered that the product is defective to become inappropriate due not handle it properly.
Damaged or used products. They cannot be sold as new as they lost value.
Products under warranty. These should be replaced with well-functioning or repaired.
Products returned by the end user as they have consummated their use, in order to destroy them or give them a treat not to damage the environment.
Goods returned by the customer and that have been opened and / or used by it. They cannot be sold as top quality.
Packing and packaging. They are items that accompany the material for use and can be reused or discarded.
The main objective of reverse logistics is to determine how the company can benefit from products and packaging, from where you ended your life to where they can be processed, reused and recovered. In this sense, the ultimate destinations for company products are recovered and once the product has returned to decide, seek to maximize their value.
Reverse logistics allows the returned products part of various processes such as reusing, repairing, selling second hand, recycled or if renewal of defective parts. For each process, the manufacturer must consider efficient alternatives when designing products or processes these alternatives are:
Repair / Renovation. The repair is intended to return a product to function when it has been used by the customer, the business is the repair and replacement only if the damaged parts. This activity requires disassembling and reassembling the parts of the product, also considers the replacement of damaged parts replaced. The damaged parts are repaired as quickly as possible and become part of the inventory of parts. Instead, the renewal is intended to give a specific quality products used in this activity, all parts of a product are inspected and repaired or replaced; also combined with the renewal date to replace old modules and other parts technologically current technologies. Such is the case of household appliances, automobiles and equipment manufacturing.
Recycling / Reprocessing. They represent a set of activities designed to add value to the products during the transformation process so that they can be products that can be recycled or re manufacturing. Product recycling recovered materials contained in products returned by the disassembly of parts, classified and transformed into raw materials, which means new production processes. While reprocessing involves the disassembly of parts, classification, restoration and reassembly, these products manage quality standards as if they were new products, so the products used are completely disassembled and all parts are rigorously inspected. For example paper, glass, metals, some plastics, textiles and automotive oils.
Cannibalism. This is called the process to recover a small portion of the product that can be reused. Its purpose is to recover a small group of parts of products or components that can be reused. These activities involve the selective disassembly of used goods and inspect the parts that can be reused. As such parts that can be retrieved from a computer: fan, chips, monitors and keyboards.
Reuse. In this process the products returned can be reused after cleaning and inspect it may require less preparation, without being introduced into the manufacturing process. For example, elements of packaging products for shipment boxes, pallets, platforms or bottles. Benefits after-sales service.
The customer service refers to service that is provided to the customer for purchasing the product, the process begins when the client requests the seller receive attention: product defects, not knowing how to use it, or no longer require it. This situation generates an expense to provide the flow of customer product back to the manufacturer.
The costs and savings sales service considered the difference between the objectives of the manufacturer and seller. If a seller wants to return a product, the manufacturer and seller might disagree on the condition of the product, its value and the response time. The important thing is that both sides need to realize that they must maintain a mutually beneficial relationship, so it is appropriate that work together to reduce the number of returns and the speed of processing. In this sense the reverse logistics integrates the interests of the parties conducting activities, which are divided according to whether a product, packaging, and once a material has been returned to the company can choose one of several options that minimize processing costs and are described below: If the case of an intermediate company in the distribution channel, the product can be returned to your supplier for a full refund. If the product has not been used, it can be resold to another customer or if it can be sold through an outlet store stocks.
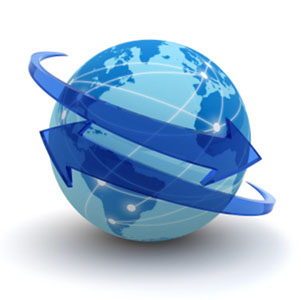
The returned product does not have the original quality to be sold, it can be supplied to a charity or exported to a less demanding foreign market. If the product cannot be sold in accordance with the above, then the company can increase the selling price significantly through refurbishment, renovation or reprocessing. If the manufacturer cannot accomplish the above, can contract a third party to whom or the material can be sold to a specialist for refurbishment, renovation or reprocessing company and then sell it for a second time as a rerun. If the item is in poor condition and cannot be reprocessed, the company disposes of the product at the lowest cost, which can be recovered and the rest is sent to a landfill. For packaging, the activities undertaken are similar to those of the product, considering the analysis of options to use, if not appropriate, evaluate alternatives renewal of packaging. If this is not possible, look for materials recovery and recycling.
Another option to sell the products, which for various reasons have not been sold through direct distribution and recover the costs of the supply chain, is the use of secondary markets. This situation involves the transfer of the product directly from the manufacturer to the secondary market company. The use of the secondary market occurs for any of the following reasons:
Changes in product packaging, generated by new designs or changes in the size of the product. An example of this is the food: drinks, processed foods, etc.. For product design, when it introduces a new product generates an inventory problem, as this may be followed by selling on the secondary market. Example is mobile phone accessories, such as chargers, and so on.
Order cancellation, this situation generates excess inventory as the manufacturer is interested in recovering the cost of investment, sold to the secondary market at a lower price. For example apparel: school uniforms, sportswear and so on.
Low volume sales, caused by mismatches in forecasting product sales, this is preferable to sell the product in the secondary market to keep unsold. Examples are seasonal products: coats, food, drinks, etc.
Strategy proposal
There are ways to generate savings and increase benefit s by implementing reverse logistics strategy, which are listed below: Curbing returned or defective merchandise not guaranteed. This implies the risk of absorbing material which may be defective, damaged or unwanted, to attract customers and increase sales at the same time pressuring vendors and thus have satisfied customers for servicing.
Reduced cycle time. This is achieved by implementing the CEDI a process to assess whether a product is defective returns may be reused or renewed or sent to landfill required.
Having information systems adapted to the requirements of the production company and links to sellers or retailers.
Having centralized return centers, these places has dedicated processing facilities for the rapid and efficient handling of returned products. In a centralized system returned products are taken to a central facility where they are sorted, processed and then transported to your next destination. It has the advantage of forming large volumes of processed products, in addition to having trained for the classification of staff returned products, the advantages of these facilities are simplifying sales processes, improvements in supplier relationships, better control on inventory of returned products, reduced administrative costs, reduced storage costs and reducing costs sent to landfills. Returns zero. In this strategy program the producer and the distributor do not allow product return by the supply chain. The producer announced to its customers that no refunds once the order is placed and, as a sales strategy, gives discounts when ordering. In other cases, the returns generated will be destroyed or disposed by other means.
Negotiation. In this activity, the price of traded goods returned without any reference of the real costs and benefits granted by the reverse flow of material. Sometimes the negotiations conducted specialized third parties to transfer the material returned to its original source.
Financial management. Companies are required to have internal accounting processes that integrate reverse logistics operations. The main concern is to identify the financial structure of reverse logistics system, and the manner in which the product is introduced to return the accounting operations of the company. Sometimes the costs of product returns are charged to the sales department and the sales staff is penalized for returns, it will try to quickly introduce the product without seeking the most appropriate way to retrieve its value.
img4
- Outsourcing. It consists of the outsourcing companies to do the reverse product flow, are characterized by external providers and specialists in handling and reprocessing renewal.
The benefits considered by the difference between the objectives of the manufacturer and seller. If a seller wants to return a product, the manufacturer and seller must agree on the condition of the product, its value and the response time.
Conclusion
The important thing is that sides, client and company need to realize a mutually benefit relationship and considered the difference between the objectives of the manufacturer and seller. If a seller wants to return a product, the manufacturer and seller must agree on the condition of the product, its value and the response time by a correct strategy.
Bibliography
1. Romero, J. A. V. Patino, M., & Cross, T. (2013). Implementation of public policies in reverse logistics. Project ‘Ciudad Jardín Bicentenario’ Edo Nezahualcóyotl. of Mexico. www.rlmagazine.com/RLMagazine_Edition_49.pdf - Reverse Logistics Magazine, (187).
Norman, L., & Sumner, W. (2006). The Sixth Hidden Costs of Reverse Logistics. Reverse Logistics Magazine. Harrington, R. (2006). Reverse logistics: Customer satisfaction, environment key to success in the 21st century. Reverse Logistics Magazine, 14-15. October 16, 2013 ... Electronic Components, INC.
Jose Luis Villalvazo, HP .... Marco Antonio Bendin, Correios ..... Authors: José Antonio Valles Romero. www.rlmagazine.com/RLMagazine_Edition_56.pdf
José Antonio Valles R.José Antonio Valles R., PhD in Logistics and Transport, Master of Engineering, Civil Engineering, Member of the National Researchers System SNI-CONACYT, National Logistics Award, granted by the SCT, CEO AVYASA Logistics, www.avyasa.com, México.D.F., director@avyasa.com, avallesdoc@gmail.com