Gain Control of Your Reverse Logistics Program with TL 9000
By Mike Childress, Brian Piechocki & Drew Dixon, PALCO
What is TL 9000?
Established in 1998, TL 9000 is an international quality management system (QMS) standard designed by QuEST Forum. TL 9000 is a specialization of the quality standard ISO 9001 and focuses on the information and communications technology (ICT) sector throughout the international telecommunications industry. It includes companies that provide ICT services all the way to equipment manufacturers. There are currently 84 adders in TL 9000, which are additional requirements to the ISO 9001 requirements. The latest revision was in 2015. A main function of this standard is tracking product defects. These defects are aggregated into a database managed by the University of Texas at Dallas – Institute for Data Analytics. This allows TL 9000 audited companies to benchmark their equipment and services against other members.i
TL 9000 AND REVERSE LOGISTICS QUALITY MANAGEMENT
High quality and reliability are primary requirements of enterprise hardware buyers. These buyers include organizations such as internet service providers, telecommunications service providers, and data center operators. They provide mission-critical services to innumerable businesses in a variety of industries, emergency and rescue services, and millions of citizens across the globe. Poor quality and unreliable hardware are simply unacceptable. Unexpected downtime is typically a minor inconvenience, but major catastrophes do occur. On one end of the spectrum, when networks or data centers fail, average people become extremely annoyed because they cannot stream Netflix. On the other end, lives can be lost if medical professionals or first responders cannot respond swiftly. Predictable reliability helps avoid these events.
Unfortunately, no product is 100% perfect. Failures occur. Components wear out or go bad prematurely. End user accidents happen. All these situations require a robust, quality-driven enterprise hardware reverse logistics and spares management program to maximize uptime and prevent disruption. This article seeks to explore the importance of quality standards to a reverse logistics program’s success with a focus on TL 9000.
Why is a quality standard like TL 9000 important? Through process controls, TL 9000 helps assure a company’s products and services consistently meet the needs, expectations, and requirements of their customers.
High-quality products and services are critical to customer experience, customer retention, and customer lifetime value. Seamless after-purchase services are just as important to customer loyalty and retention. There is no faster way to lose a corporate account than sending “DOA” units back into the field after a return. Rigorous quality standards ensure that any repaired or replacement units meet the same OEM specifications as new products. Consistency is the name of the game and a key driver to exceptional customer experiences.
If a customer experiences an issue with your product, it must be handled in an efficient manner. A reverse logistics firm specializes in this function by accepting returns, creating rapid repair/refurbishment processes, and returning the product to the customer in a timely manner.
Many OEMs provide advanced exchange to their customers instead of making them wait for their returned unit to be received, tested, repaired, and possibly declared beyond economical repair. An adequate “spares pool” is required to support this advanced exchange program. Typically, these spares pools are comprised of new units but also field units that have been returned by customers and repaired. Rigorous quality standards help ensure that repaired units within the spares pool are as dependable as brand-new units. The risk of sending multiple defective advanced exchange units is significantly reduced, reducing future reverse logistics costs and the chances of damaging customer relationships.
Thorough quality procedures document and identify recurring failures using failure analysis. This information is helpful to determine improvements to your product design or parts sourcing. A quality-driven failure analysis process may uncover issues that were not apparent during the manufacturing quality checks because the products did not have enough time to operate in the field. This could lead to decreased future failure rates and decreased returns costs.
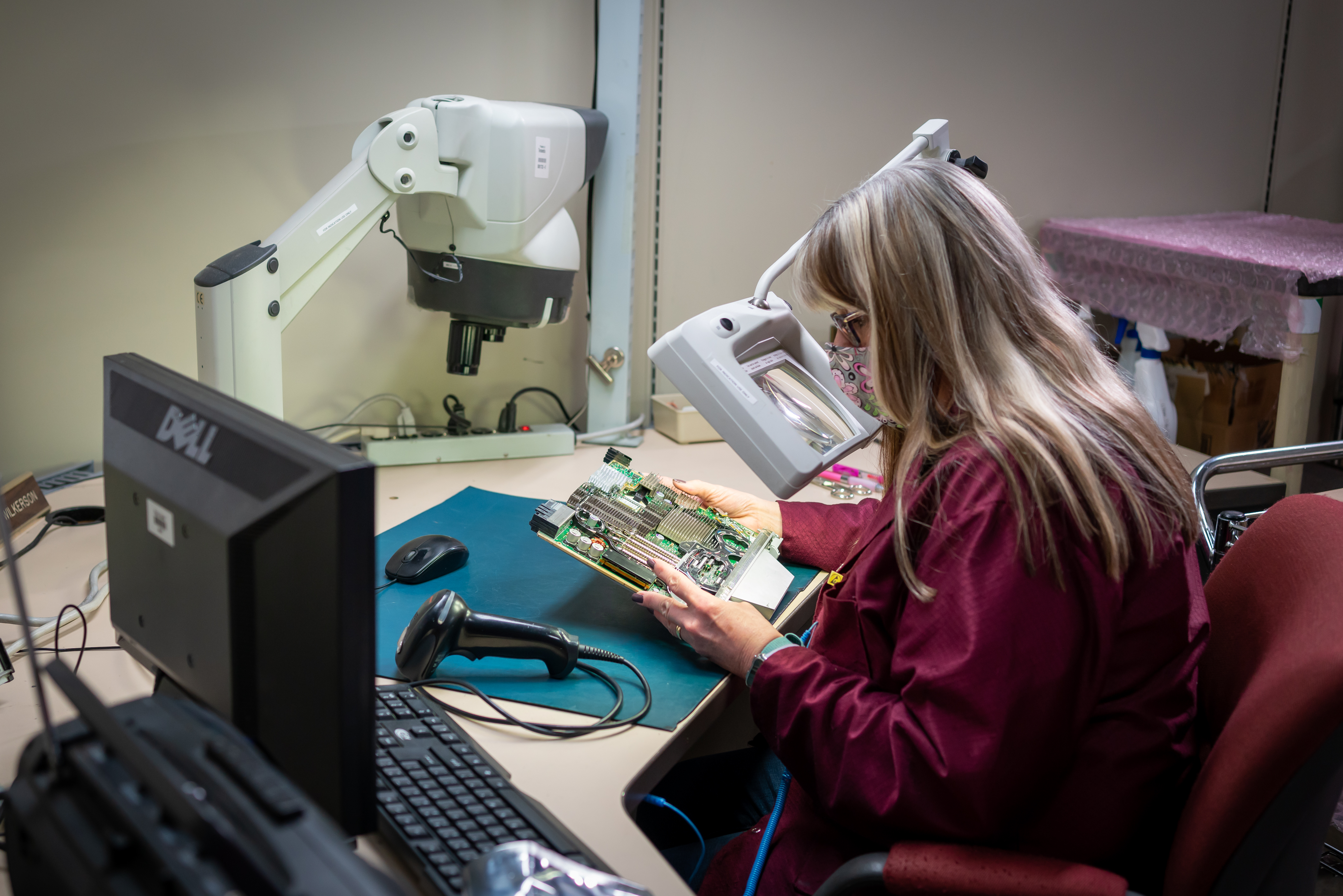
We’ve established that a comprehensive QMS is vital to customer experience, but why is TL 9000 superior to others for enterprise hardware reverse logistics programs?
After the telecom industry was deregulated, inconsistent quality standards reportedly cost the telecommunications industry between $10 and $15 billion.ii In response, an industry consortium of major partners and competitors created the TL 9000 QMS in 1998. This consortium dubbed themselves QuEST Forum (now TIA QuEST Forum). QuEST Forum augmented the ISO 9001 specifications with “adders” to better reflect the stringent quality requirements for international telecommunications supply chains. Today, TL 9000 positions itself as the QMS system for the broader information and communications (ICT) sector since the lines dividing internet service providers and telecommunications service providers continue to blur.iii TL 9000 is widely considered the “gold standard” for Quality Management within the ICT industry. It is valued and recognized by the “who’s who” of the industry including Dell, AT&T, Cisco, ADTRAN, Hewlett Packard Enterprise, Verizon, Samsung, and more.iv
One word describes why TL 9000 is highly beneficial to enterprise hardware reverse logistics programs: Control. Whether you’re a 3rd party provider or an internal reverse logistics program, TL 9000 provides the framework to maintain complete control over your processes.
Another benefit of TL 9000 is mandatory data submission for benchmarking. Manufacturers and suppliers are required to anonymously submit their data to University of Texas at Dallas to be benchmarked against their peers.
Harold F. Dodge, a pioneer in statistical quality control, once said, “You cannot inspect quality into a product.”v Rigorous quality standards are necessary to maintain complete control over product reliability. If you are relying on inspection alone, it is too late.vi For Enterprise Hardware, TL 9000 is a powerful tool to consistently produce high quality repaired and refurbished products.
BENEFITS OF TL 9000 FOR ENTERPRISE HARDWARE REVERSE LOGISTICS PROGRAMS
As mentioned, a company cannot inspect quality into a product. This would only be as effective as the inspectors at the end of the line and would not prevent these defects from occurring. Therefore, many companies have switched from quality control and chosen quality assurance as a better way to ensure fewer product failures. Quality is built VIthe product when designing and servicing it. It is not easy or cheap to find benchmark metrics to evaluate a company’s quality assurance program. The auditors from TL 9000 and TIA QuEST Forum review and process results from many companies that operate in the telecommunications industry. This allows a company to analyze the results of other companies’ audits and make necessary adjustments to operations that can help improve quality for short and long term.
Training is a crucial aspect of belonging to TIA QuEST Forum and complying with the standards that TL 9000 upholds. All interested parties involved with the implementation of TL 9000 are trained on the concepts of the standard. All employee training records are kept in a centrally located area or by department. Testing and calibration records are also retained for compliance purposes. This includes how the product was tested, who tested it, what equipment was being used to test, and if the equipment was calibrated. A comprehensive calibration program is a must. This helps a company by creating a tried-and-true process to ensure quality in a product and makes sure that the control process for the end-product is reliable.viii
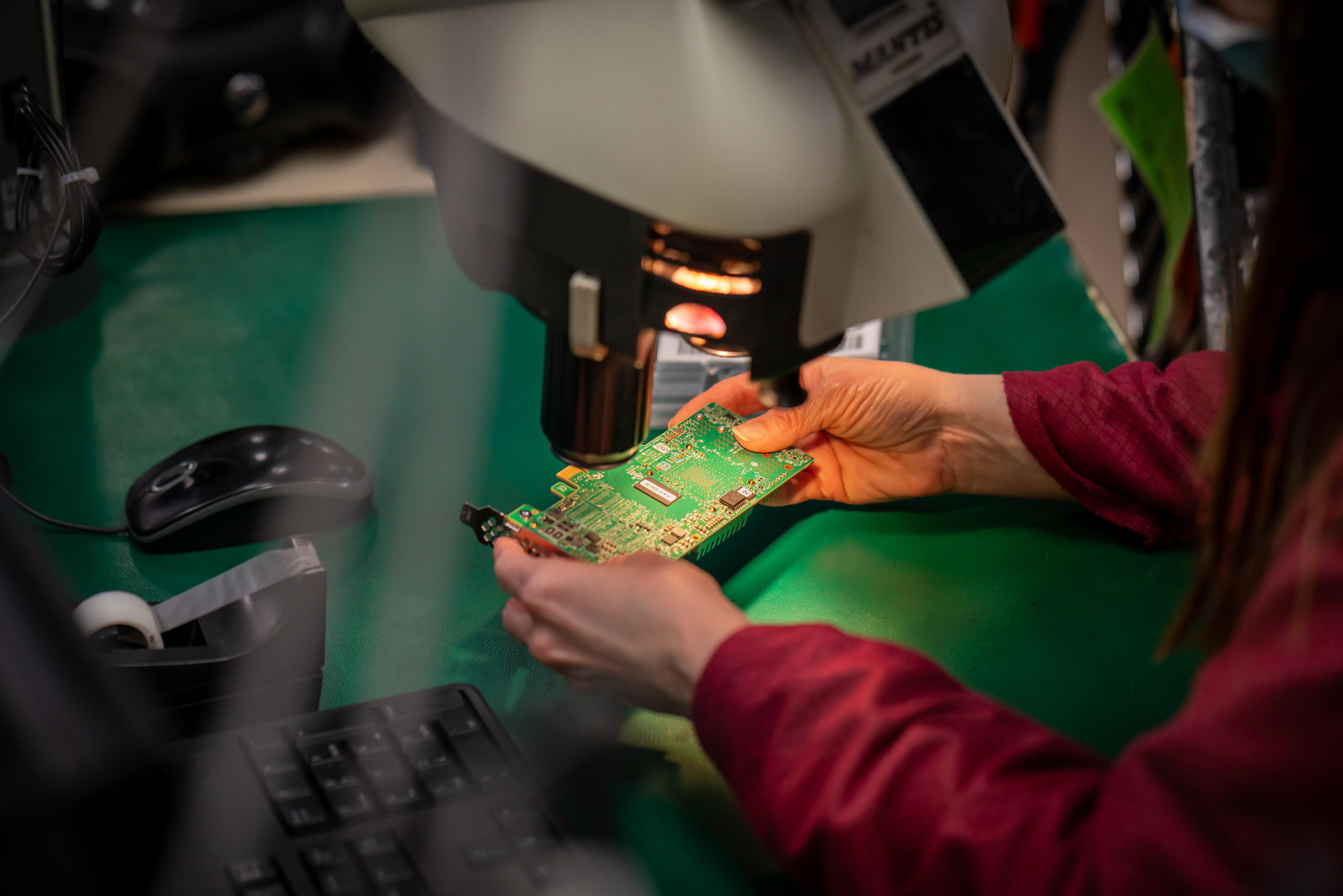
Electrostatic discharge (ESD) awareness and training is crucial to any company operating in the electronics industry. It is invisible but can significantly damage a component during any stage of its lifecycle. An electronic component could be affected by ESD and still pass quality inspections but could go on to have a shorter lifespan in the field, damaging your brand. TL 9000 requires all relevant employees to complete ESD training.ix
Overall, TL 9000 is a beneficial resource to help a company maintain the quality of its products and services. Allowing another set of eyes (third-party certification) to come in and streamline operations can result in higher quality products and service. Even though TL 9000 was originally designed for the telecommunications industry, any enterprise hardware reverse logistics program can benefit from the disciplines of the QMS.
Sources
i https://en.wikipedia.org/wiki/TL_9000
ii https://web.archive.org/web/20140714221107/http://www.ospmag.com/issue/article/Whats-TL-9000
iii https://www.cisco.com/c/en/us/about/approach-quality/tl-9000.html
iv https://tiaonline.org/what-we-do/tia-quest-forum/participants/
v https://en.wikipedia.org/wiki/Harold_F._Dodge
vi https://deming.org/inspection-is-too-late-the-quality-good-or-bad-is-already-in-the-product/
vii TL 9000 Release 3.0: A Guide to Measuring Excellence in Telecommunications Second Edition. Sanford Liebesman, Alka Jarvis, and Ashok V. Dandekar. Pg. 146
viii https://tl9000.org/alerts/qa/requirements.html
ix TL 9000 Release 3.0: A Guide to Measuring Excellence in Telecommunications Second Edition. Sanford Liebesman, Alka Jarvis, and Ashok V. Dandekar. Pg. 30
Mike Childress, Brian Piechocki & Drew DixonMike Childress - Mike is Vice President of Quality and
Operations at PALCO, responsible for
worldwide development, improvement,
implementation, and maintenance of ISO/
TL Management Systems registrations.
He leads client and supplier qualifications as well as social
and environmental health and safety programs at PALCO.
He is an active member of the TIA QuEST Forum and helped
shape the future of TL 9000 Quality Management System with
the development of its requirements and measurements
handbooks. Prior to joining PALCO, Mike spent 20 years in key
positions with Intergraph Corporation and GTE Communication
Systems. He served as the key interface with clients from
around the world in the resolution of quality issues.
Brian Piechocki - Brian is PALCO’s Director of Business
Development & Strategy and is responsible
for PALCO’s go-to-market strategy. Brian
rejoined PALCO after a five-year tenure at
Cognizant (NASDAQ: CTSH) where he held
various roles spanning multiple verticals including Life
Sciences, Retail, and Manufacturing. Brian brings a unique
perspective shaped by his exposure to multiple industries, mix
of client-facing and internal roles, and focus on identifying
market trends. He is passionate about translating PALCO’s
strengths into solutions that solve companies’ complex returns
management and sustainability challenges. Brian holds a
Bachelor of Science in Business Administration from Boston
University and a Master of Business Administration from the
George Washington University.
Drew Dixon - Drew is the Marketing Coordinator and
Human Resources Assistant at PALCO, where
he is responsible for: heading marketing
campaigns, content creation, recruiting,
employee relations, and corporate social
responsibility. Drew joined PALCO after completing an internship
program at the company in the summer of 2021. Graduating
from the University of Alabama in Huntsville in 2021 with a
Bachelor of Science in Business Marketing, Drew brings a fresh
point of view into the world of Reverse Logistics.