Reinventing Technology Product Life Cycle
By Bernard Kiernan, Intel
Per the World Economic Forum an estimated 57.4 million tons of electronic waste was discarded in 2021, which outweighs the Great Wall of China1. Managing electronic waste (e-waste) is a critical sustainability challenge we face at a global level. Customers, investors and employees expect resilient, responsible supply chains across the entire product lifecycle. There are also growing governmental regulations on reuse, repairability and waste reduction across the globe making e-waste, and product lifecycle management not just a ‘nice to have’ but a requirement. By applying circular economy principles, Intel has been able to achieve overall recovery rates on returns above 50%, $30M in added value in just one year, and <1% landfill rate on global product returns.
In addition to the environmental benefits of reduced waste to landfill and CO2 emissions, circular economy strategies bring significant financial benefits through supply chain cost saving and new revenue streams. For example, Intel deployed programs to recover, test and repurpose product for resale on secondary markets which enabled new revenue and extended product life.
Today, many supply chains are facing constraint challenges. The introduction of circular flows into the supply line can help insulate organizations from some of these challenges. Intel implemented new recovery and repackaging capabilities to replenish warranty spares inventories for constrained products thus increasing spares stock availability to support customer warranty claims.
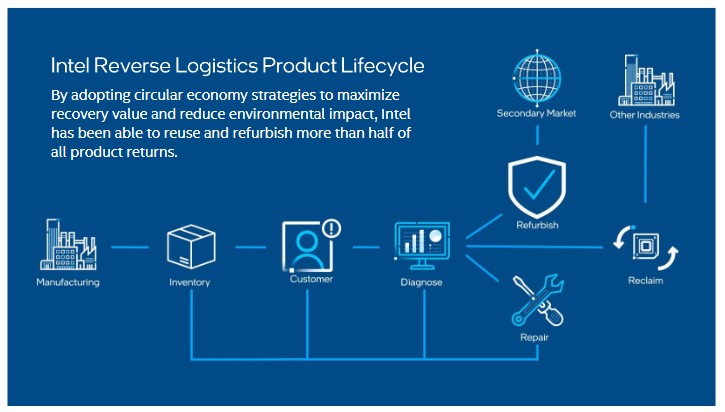
While implementing circularity may seem daunting, going through the following steps will help identify opportunities to reuse and extend a products useful life:
- Map out the product’s lifecycle
- Identify the decisions points that will extend a product’s useful life
- Engage with suppliers and customers on troubleshooting product issues and recovery options
- List out what influences decisions to extend a product’s useful life
Some questions to consider when going through the process of reinventing the product lifecycle:
- Can we help customers diagnose the issue and if a return is needed, what specifically needs to be returned?
- When products and parts are returned, how do we maximize their value and extend their useful life?
- What capabilities are required to allow preferred options such as reuse, repurposed or recovery to be pursued?
- Supply lines needed to support servicing and recovery at regional level, i.e. spare parts availability for repair and sub-assembly exchange?
- The highest value decision may not be the same as the last time it will be influenced by customer needs, market demand, location, existing inventory levels, costs, etc. which can change over time. It’s important to ask, what data and IT systems are required to make the best decision?
By taking an integrated approach across the organization, circular economy principles can be incorporated into the following areas:
- Products design: think about the selection and use of recyclable materials in both the product and its packaging. In addition, design the product for ease of service and repair
- Enabling product recovery capabilities at local service centers where feasible or at centralized locations depending on capital and resource investments requirements
- Timely availability of spare parts to support local recovery options
- Extending product life through business models such as offering extended warranty options and utilizing secondary market sales channels
If product cannot not be repurposed, repaired, or recovered, then as a last option route to materials reclaim processes so the materials can be circulated back into the manufacture of new products thus avoiding landfill and creating a more sustainable future.
Read more about Intel’s circular economy work here.
References:
1https://www.weforum.org/agenda/2021/10/2021-years-e-waste-outweigh-great-wall-of-china/#:~:text=In%202021%2C%20human%20beings%20will,the%20world’s%20heaviest%20human%20construction
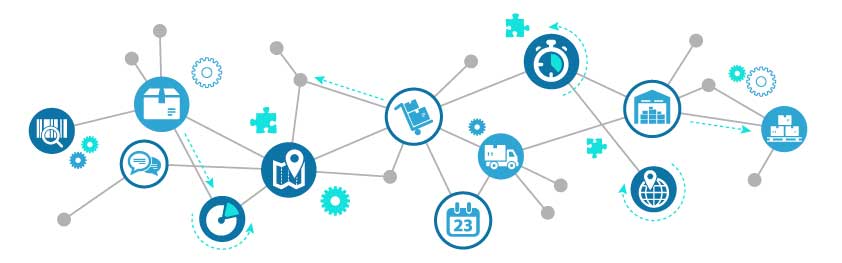
Bernard KiernanBernard Kiernan has been with Intel Corporation for over 27 years in a variety of roles from Quality Management, Services Management, Project and Program Management. Most of this time has been in the Reverse Logistics organization in the design, deployment and management of Reverse Logistics solutions across Intel’s broad spectrum of products. He has also a Circular Economy program across Intel's supply chain which has delivered significant improvement is asset recovery rates, reduced over 70 metric tons of e-waste and $75M in value from cost saving and revenue.