Global Distributor and Service Provider Design Innovative Reverse Logistics Solutions
By Dennis Ayo, Executive Vice President, Triage Partners & Jay Fraze, Dir. of Supply Chain Mgmt Services, Tech Data GLM, TD SYNNEX
Tech Data and Triage Partners have collaborated since 2017, designing innovative solutions to assist their technology customers’ reverse logistics challenges. Tech Data is a leading provider of global supply chain services to a wide range of electronic manufacturers and resellers. The company places a constant focus on both scaling to the changing needs of existing customers and building solutions for prospective opportunities. Tech Data has built partnerships with companies like Triage to execute these plans quickly and cost-effectively.
Triage is able to launch custom processes by utilizing their proprietary software and sourcing a specialized and skilled workforce. Both parties have seen success using this approach to scope customer requirements and launch a program utilizing combined resources. The two following case studies illustrate how thinking outside the box has driven valuable solutions for our customers.
Service Parts Inspection and Acceptable Quality Limit (AQL) Service
Tech Data is the exclusive global distributor of service parts for a global technology original equipment manufacturer’s (OEM) product line. The OEM service parts are shipped from the OEM’s contract manufacturer in Asia to Tech Data’s Fort Worth logistics center for distribution to its authorized warranty repair providers throughout North America, APAC and EMEA. The OEM invests in last time buy of service parts to ensure they have adequate inventory to support their customers throughout the life of the product. As part of the OEM’s Total Quality Management System (TQMS), they desired to perform a post-production inspection of sample lot sizes of service parts based on defined AQL metrics.
The parts inspection process defined by the parties included (but was not limited to) data capture, visual and functional test work instructions, product receiving, sample lot size movement to inspection lab, quarantine and other processes.
Tech Data and the OEM set up a climate-controlled parts inspection lab inside Tech Data’s Fort Worth distribution center to mitigate unnecessary movement of parts. The OEM provided visual and functional test work instructions and fixtures so parts would be properly tested to manufacturer specifications. Based on the specific part inspection criteria, if the lot passes visual and/or functional test, parts can be returned to inventory immediately. If the part inspection fails AQL sample lot size based on OEM instructions, parts are quarantined until a disposition/resolution is agreed upon by the OEM and manufacturing provider.
Triage modified its WipIT™ system to meet Tech Data product movement requirements in the distribution center as well as the OEM’s visual and functional test work instructions. The system captures the purchase order for the specified part(s), part number, part description and receipt quantity. Additionally, the system calculates part sample size quantity based on OEM-assigned AQL level to the receipt quantity, which then generates a request to Tech Data for the appropriate quantity to be moved to inspection lab.
Parts are inspected both visually and functionally based on OEM criteria, test procedures and work instructions, and visual aids are integrated into the workflow control system to ensure processes and procedures are met.
Triage WipIT™ captures record for each part that is inspected and tested, any failure reasons/codes and photos of any visual defects found during the process. Furthermore, Triage WipIT™ calculates specific cumulative results of lot size quantities for a given period based on OEM quality guidelines.
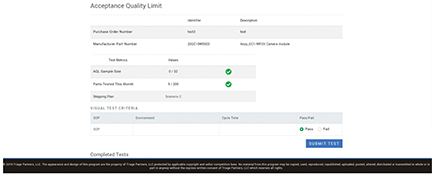
Triage notifies Tech Data and the OEM when product is ready for processing into finished goods inventory and provides all reports and backup data of all part inspections based on an agreed upon schedule. Parts that fail a sample lot size are moved to a quarantine area until disposition can be resolved.
By providing a service parts inspection with AQL standard process within the distribution center, parts can be inspected and tested upon receipt. If defects are found, they can be identified and corrected at the front end of the procurement and manufacturing cycle, eliminating potential costs and customer satisfaction issues in the future.
Product Returns Processed Rapidly in the Distribution Center
Tech Data is a key 3PL distributor for a global imaging company. Products are distributed to many different resellers: sub-distributors serving the channel, big box retailers, independent dealers and eCommerce providers. Products are returned for various reasons, and it is critical that returns are processed rapidly with the highest levels of quality possible.
The objective was to design a reverse logistics solution to process returns within the distribution center to mitigate product value leakage, but there were many challenges.
Returned product is inspected and tested based on the customer’s specifications. The disposition of inspected or tested products acceptable for sale is based on either customer-defined classifications (Class 2, 3, etc.) or if the product needs to be scrapped or sent to a repair vendor. With over 300 different kitting configurations, there is a materials management challenge in ensuring that appropriate levels of stock are available to complete the returns process and move product into a sellable good.
To enable processing returns rapidly, a system had to be deployed that could complement Tech Data’s ERP/warehouse management system and ensure appropriate inspection and tests were performed, failure data was captured, appropriate classifications were assigned and acceptable sellable product was kitted and packaged with the appropriate items based on the customer criteria. Additionally, the system had to provide visibility of product in work-in-progress status so Tech Data could track material movement within the warehouse and the stage at which a unit was being processed.
Triage designed the cloud-based workflow control system to identify source of return, track all inspection and test processes, capture labor content for each unit processed and manage complex material usage requirements, ensuring kitting and packaging inventory was available to complete the returns process.
Today, product returns are processed in less than three business days of receipt, and units acceptable for sale maintain maximum value.
Tech Data and Triage continue to work together to identify their customers’ reverse logistics challenges and provide flexible and innovative solutions.
Triage Partners is a certified minority business enterprise and has been recognized by its customers as an innovative business partner. If you would like more information about Triage Partners, please contact Dennis Ayo via email at dayo@triage-partners.com.
Tech Data, Global Lifecycle Management (GLM) is a provider of specialized solutions within Tech Data. GLM gives technology companies the freedom to focus on the road ahead by providing end-to-end customer and product lifecycle management services. Leveraging our team of experts, global logistics network and over 40 years’ experience, we design solutions to release precious capital from our customers’ businesses so they can focus on investing in their transformation journey. Start your journey at www.servicesbytechdata.com, reach out to us at GLM@techdata.com or follow us on LinkedIn.
Dennis Ayo, Executive Vice President, Triage Partners & Jay Fraze, Dir. of Supply Chain Mgmt Services, Tech Data GLM