Innovative Ways to Pick-up a Return
By Gordon More, IDS Internet Dispatch Services Ltd
Stating the obvious: Reverse Logistics starts at the point of picking up the return. This means how you pick-up affects every other action further down the chain. In this article I will discuss the innovative ways Returns are being picked up to help reduce costs, increase customer satisfaction and provide superior documentation.
Reverse Logistics? “A complete supply chain dedicated to the reverse flow of products and materials for the purpose of returns, repair, remanufacture, and/or recycling.”
– Reverse Logistics Association
But first, if you are not offering Reverse Logistics, you are missing out.
Worldwide, the Reverse Logistics market value is expected to reach $603.90 billion by 2025; that’s up from a value of $415.2 Billion in 2017. The main driving forces behind the growth of this market are the expansion of e-commerce, more stringent government regulations, the pharmaceutical industry and the rising tide of e-waste (Reverse Logistics Market by Return Type (Recalls, Commercial Returns, Repairable Returns, End-of-use Returns, and End-of-life Returns) and End User (E-commerce, Automotive, Pharmaceutical, Consumer Electronic, and Others): Global Opportunity Analysis and Industry Forecast, 2018 – 2025)
If that’s still not enough to sway you, with governments tightening up regulations on pharmaceuticals and tobacco, the increased flow of high value e-waste and the legalization of recreational cannabis, you might just find yourself in a position where you have no choice but to offer Reverse Logistics.
More than “Pick Up and Go”
Sometimes just picking up a return and putting it in a vehicle is not the way to go. Cost and documentation are key considerations in the choice to use Reverse Logistics.
Pick Up and Go?… it’s just Drop and go but in Reverse
While “Pick-Up and Go” does reduce the cost of the initial pick-up, it significantly increases the overall cost of your reverse logistics process by creating more labor and costs further down the chain.
That’s because Returns almost always result in a direct financial payment or credit which carries tax implications.
When dealing with controlled substances – like cannabis, pharmaceuticals, and tobacco – government regulations regarding accuracy of Return contents must be satisfied.
“Pick-up and Go” means the contents of a return will not be audited until the package arrives back at the reclamation center. This could be days or even weeks later. Any mistakes will result in the expense of further communication with the customer, manually updating financial records, and sending out yet another vehicle, all to pick-up the Return again. Hopefully the second pick-up will be correct.
The Reclamation Centre is the central warehouse of Reverse Logistics.
A simple, innovative solution – currently in use – is to scan each product’s SKU or UPC at the point of pick-up to document the accuracy of the Return shipment.
For controlled substances and goods of high value, a location scan can also be included to prove the product scan took place at the pick-up location.
By scanning each product’s SKU or UPC at the point of pick-up, the accuracy of the Return is immediately confirmed. This reduces the overall cost – when including customer service, taxes, and extra pick-up expenses – of your Reverse Logistics process.
One last point: imagine a customer requesting a Return and credit for goods worth $1000. This customer then ships the wrong the products which only have a value of $100. How and when do you capture this cost?
Creating Documented and Audited Returns in the Field
How do you create an efficient process for those large retailers who refuse to provide, in advance, an itemized list of what is being returned? They simply demand that a vehicle is sent to their location to pick-up all the products to be returned.
An innovative way to meet this challenge is to take the solution from above, “More than Pick-Up and Go”, a step further.
When the driver arrives at the location, they simply scan the SKU or UPC of each product into their mobile device. The scanned SKU or UPC is then matched to a product and the number of times the item is scanned is equal to the number of pieces of that product. From these scans an itemized return is created, complete with electronic documentation.
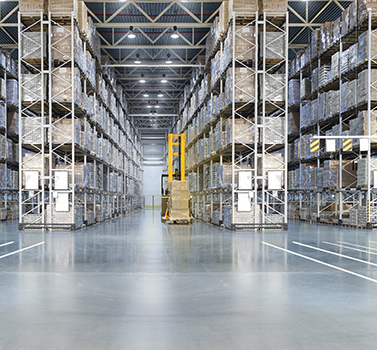
Think of it as turning the mobile device into a mobile shipping portal.
For controlled substances and extra security, a pick-up location scan can be added into the process.
Why not simply pick-up the product, bring it back to a reclamation center, then sort and create a return at that time?
It comes down to loss prevention – especially for controlled substances and goods of high value – and customer service.
By creating a true itemized shipment at the point of pick-up, you can ensure that all the product is accounted for as the Return works its way back through the Reverse Logistics chain to the Reclamation Center.
You can also instantly provide to your customer an itemized list of exactly what was returned. They will not have to wait days – if not weeks – for the Return to work its way back to the reclamation center and be audited to receive their itemized list.
Verifying Authorized Returns
Some manufacturers restrict Returns to a maximum per annum, by product type and/or amount. How do you meet those requirements and ensure what is being picked up matches the authorized return amount?
An innovative process currently implemented is as follows:
1) the customer calls in or enters online their request for a return;
2) the request is authorized;
3) the exact product type, quantities, and customer’s location is transferred to the logistics company’s TMS which in turn creates a detailed Return.
When the driver arrives at the pick-up location, they scan the product’s SKU or UPC against the created Return to ensure an exact match to what was authorized. At this point the driver can refuse to pick-up any extra or incorrect stock.
Some might balk at having the driver enforce the accuracy of the Return. The alternative is to pay the internal costs of shipping the incorrect Return back to the reclamation center and having an employee contact the customer to try and fix the mistake. Then, the company must decide if the mistake should just be absorbed as a cost or if they should spend more to dispatch another vehicle to pick-up the Return, hoping that it’s accurate this time.
Reverse Logistics and the Chain of Custody
Sending out your fleet to pick-up Returns without any proper control can be a mistake. It’s interesting to see final-mile deliveries demand a proper Proof of Delivery (POD), while the Reverse Logistics of the very same product amounts to placing the product into the back of a vehicle without a proper Proof of Pick-Up (POP). Some products that are being returned hold significant value and demand proper tracking and tracing.
POP? Its not Proof of Delivery, its Proof of Pick Up
A simple, innovative solution is to treat the Return just like a delivery, but capture the POP and Shippers….AKA the “Return’er“… signature. From that point onwards, the normal Chain of Custody procedure is observed.
Reverse Logistics Offers Superior Customer Satisfaction
In addition to capturing a POP, some Reverse Logistics providers are then affixing the POP and signature onto a PDF eBol – which contains a list of products picked-up – that is then instantly emailed to the customer. eBol? Electronic Bill of Lading
Why have the customer wait to receive the itemized eBol days – or even weeks – later? Just so the Return can arrive back at the reclamation center and be audited? That wait defeats the purpose of a Bol.
Some innovators have taken this even further: by connecting their TMS to their accounting system (SAP, etc.) they can instantly apply a credit to customer for the return at the point of pick-up. Customers can see their credit within minutes of the Return being picked up.
These are some of the innovative ways the Reverse Logistics process starts at the point of pick-up.
Gordon MoreGordon More has been designing
software and mobile applications for
the Delivery and Logistics Industry
since 2005. He is passionate about
designing software to solve complex
issues with elegance and simplicity. His
work improves security and efficiency in
US pharmaceutical delivery, and brings
ease to Reverse Logistics in Australia.