Right to Repair
By Sam Goldheart, iFixit
The first Right to Repair law since 2012, and the first-ever electronics Right to Repair law has just passed in New York. So is it the law of the land? Not yet. But the tide is turning and if manufacturers don’t want to get wet, they’ve got to get moving. Moving where? And why, and how? Let’s break down what the Right to Repair means for the companies building the tech that needs repairing!
The Right to Repair is a catchall term for all legislation that protects the free market of repair. It has been most popular in the venue of electronics products, given the complexity, price, and increased manufacturer control of these devices. From laws like the 1975 Magnuson–Moss Warranty Act, to this year’s landmark bill in New York, legislation lets repair happen on the free market, and not just in a single walled garden. It would be absurd to have subscription-only BMW wiper fluid pods, so why do we let printers get away with it? Batteries wear out just like tires, so why can’t we replace them, too?
Given the broad nature of Right to Repair, the focus of legislative fights is continually changing. Magnuson–Moss raised the bar when it secured the right to maintain a warranty despite doing a repair with third-party parts. So too will today’s fight for repair documentation and parts availability be a step on the way to curtailing software repair restrictions and copyright law overreach.
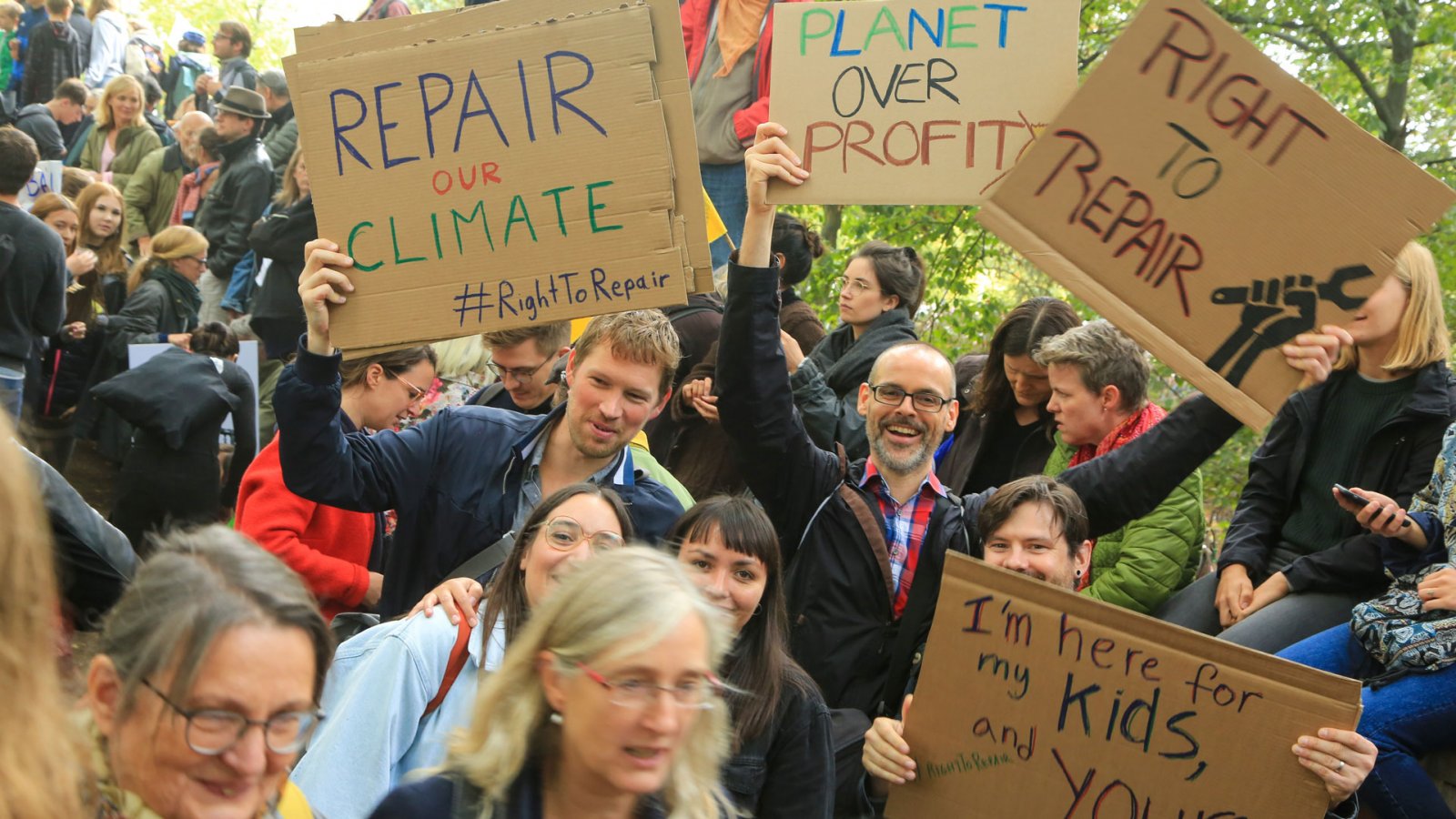
While investment in repair infrastructure may strike fear in the hearts of CFOs at first, building a better, more repairable product is actually good business. Tech built with repair in mind saves money during manufacturing and rework, and it can save billions in the event of a part recall disaster (Samsung’s Note 7 recall cost $5.3 billion—much of which could’ve been avoided if the battery was easy to change). Repairable devices are also easier to recycle, so end-of-life planning is greener and less hassle.
And most importantly, supporting repair builds brand loyalty. 95% of iFixit members say that a successful repair makes them more likely to buy from that company. And 96% of all Americans say that when they’re picking a car, repairability is important to them. 77% say it’s important when picking a smartphone. Repairability is integral to the Right to Repair, in that our stuff is only repairable when parts, information, and tools are available.
What Will Manufacturers Be Required to Do?
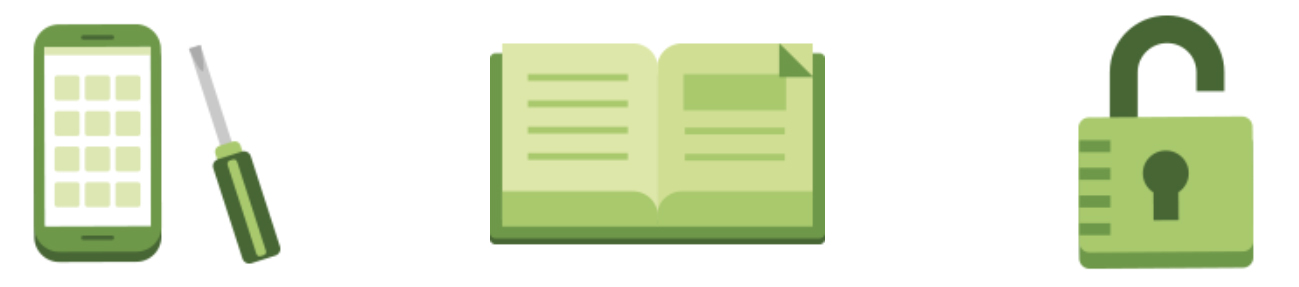
Repair tools, knowledge, and free access to repair are fundamental needs.
The current focus of Right to Repair has three main tenets: parts should be available at reasonable prices, service manuals should be free and public, and repair information like software tools and schematics should be available.
Repair advocates are also working to support repairability labeling to inform consumers of the likely lifetime and fixability of the product, stricter policing of copyright law to prevent abuse, and enforcing repairable designs (e.g., replaceable batteries, long-term software support, etc).
These rights are being fought for tooth and nail, and bit by bit, they’re taking hold. Colorado has gained protections for wheelchair repair—breaking a monopoly that leaves people waiting weeks for the fundamental right to movement. New York is freeing a chokehold on many electronics but has yet to secure appliance repair coverage. Right to Repair is winning, and it’s time for manufacturers to fix their broken repair policies.
If you work for a manufacturer and that sounds intimidating, we’ll tell you what we’ve been telling DIY fixers for almost twenty years: You can do it. We’ll show you how.
How Can Manufacturers Meet Right to Repair Requirements?
While repair support may seem daunting to many companies, it shouldn’t be onerous to roll out. It could be as simple as expanding the resources used by authorized mechanics—as Apple has slowly done over the years—but for manufacturers without service centers, there’s plenty of options out there.
Option 1: Build your own repair solution from the ground up
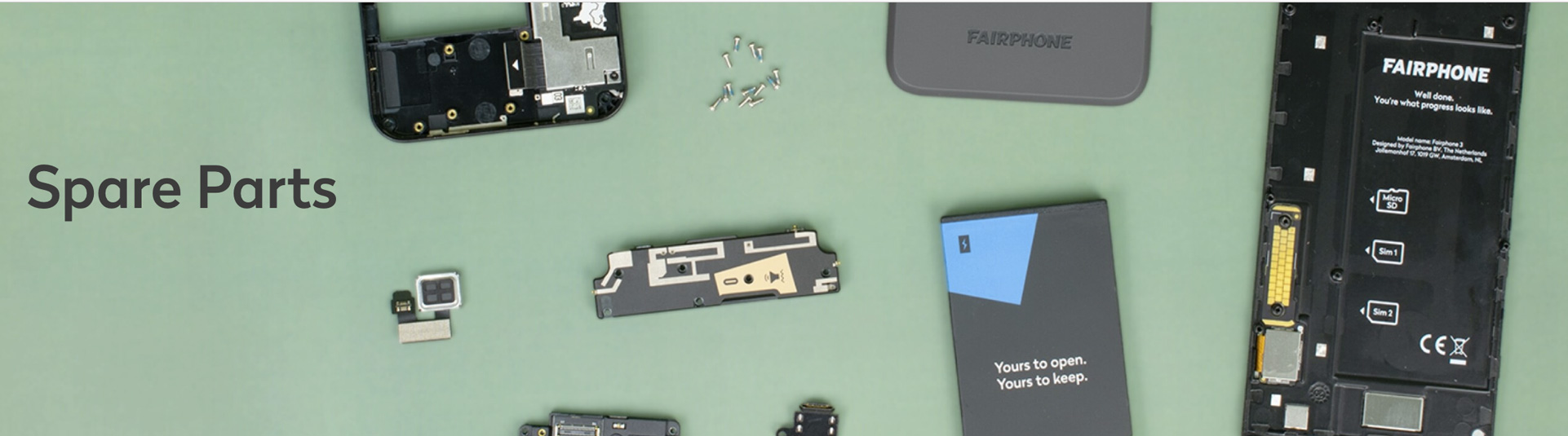
Built to be repairable, and supported by parts and software, Fairphone is an industry leader in Europe.
Companies like Fairphone and Framework have built their products with part replacement in mind. This is the easiest way to comply with regulations—if you’re starting a new device manufacturing company from scratch. For large corporations with internal inertia, creating a repair platform can be difficult. Not only must the culture shift from maintaining strict privacy and control to transparent support, but logistics and data can be hard to whip up overnight.
Option 2: Trust a third party to tackle your logistics
Apple has opted to engage a third party service for its Self Service Repair program, creating an entirely separate website and system. It was likely a relatively turnkey solution, and it shows. Okay, maybe we’re a little biased. But it’s not hard to argue that the typical Apple polish is missing, and the branding could leave many customers wondering about the authenticity of the parts.
Local repair options from companies like uBreakiFix have enabled Samsung to provide solutions without too much trouble. Any one of these services could be expanded to fulfill the three-pronged repair needs—parts, tools, and guides. But we’ve got some good news, too. At the risk of stating the obvious, we know a company who already does that.
Option 3: The iFixit way
As you may have heard, we’ve been working with manufacturers including Google, Samsung, and Valve to get repair parts to individual fixers. The beauty of the repair community is that we have always, well, fixed. iFixit was born out of the need for repair manuals. We manufactured the tools that were designed to keep us out. Every day, we help fixers—and manufacturers—fix their stuff. iFixit has the ability and experience to handle everything from parts sales to service manual hosting and creation.
Working with iFixit is just one of the many ways to comply with Right to Repair legislation, but if you’re looking for help, let us know.
Which Companies Are Already Prepared for the Right to Repair World?
Manufacturers around the world are preparing for the paradigm shift that is Right to Repair. Some companies opt for a conservative approach, others have made a serious effort to futureproof. Huge corporations are making moves, and whatever level of investment you want to put in, someone is out there doing one better. Let’s take a look at some industry leaders and their level of commitment.
Quick and dirty compliance
Samsung has provided service manuals online for years—for a price, and if you know where to look. Compliance could look as easy as making service manuals available digitally on their site, for free. But that’s a bare minimum that will quickly lag behind regulations. Samsung has since started working on a more complete solution.
If you’re looking for the best place to put those PDFs, why not in the world’s largest, free, online service manual? During the pandemic, we ingested 13,000 medical device repair manual PDFs to help technicians at hospitals around the world keep their respirators up and running. If we can tackle a whole new device category and a whole new repair community overnight, iFixit might be a great place to plant your flag.
Compliance when you don’t have service documentation
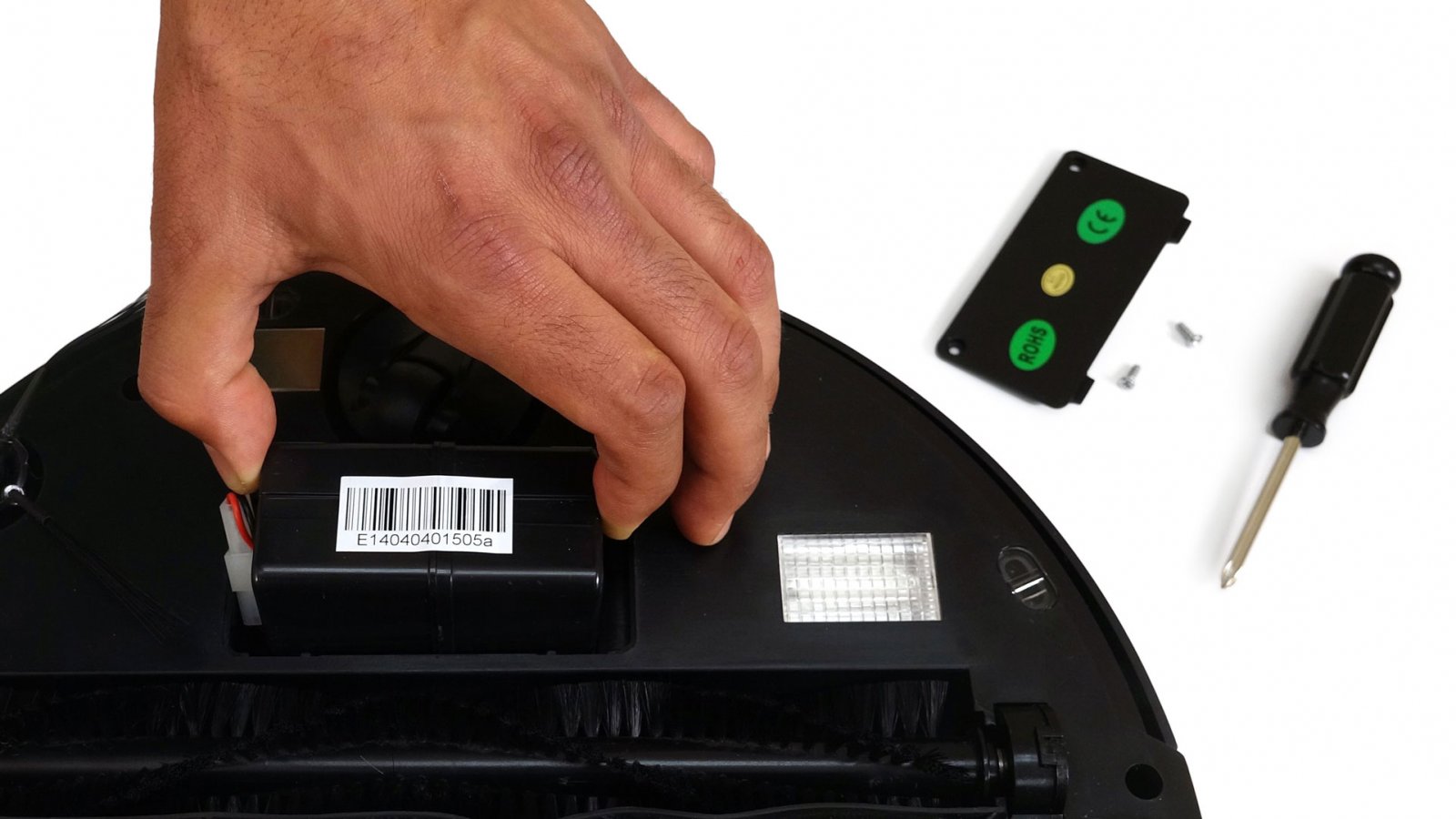
Replaceable batteries, and a free public guide—well done, bObsweep!
For manufacturers who want something a little more user-friendly than a PDF—or who don’t have the guides to begin with—the iFixit platform is a great way to create, host, and share repair information with the global community. Remember that successful repairs make loyal customers. San Francisco bag company, Timbuk2, chatted with us and decided they wanted to make some guides themselves, and honestly, they’re not bad. bObsweep—apparently Canada’s leading manufacturer of home robotic products—showed up on the site one day with a full suite of thorough repair guides. Color us impressed! The iFixit guide platform really is that easy. (P.S. we’ve got guides on making guides!)
Full Suite Compliance
Companies like Apple, known for foresight and speedy action, have made parts, tools, and repair information available ahead of legislation. This not only gives them time to work the bugs out of the system, but the sooner manufacturers get on the repair bandwagon, the better off the planet will be. And let’s face it: sustainability is good business.
As for Samsung, Google, and Microsoft? Well, we’re hoping to have more good news soon. Keep an eye on our collaborations for more inspiration.
The Extra Mile
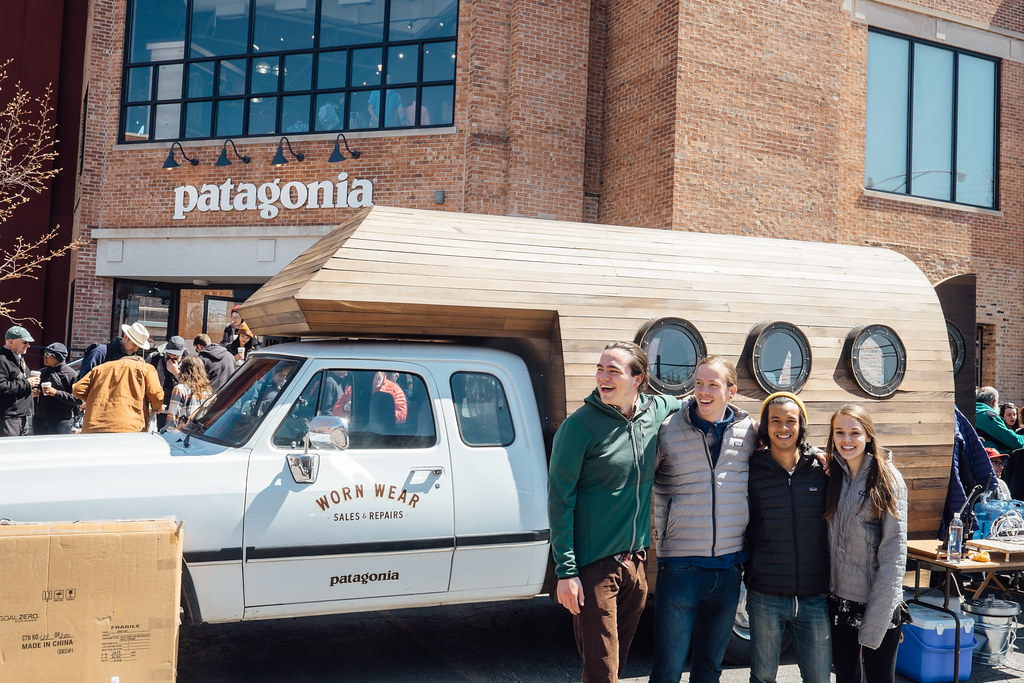
Patagonia has eco-consciousness written into its very DNA, so it may not be surprising that they were the first manufacturer to collaborate with iFixit to help their customers get stuff fixed. They have fully-fledged support for lifetime garment repair, and have a popular refurbished product line. They have also posted dozens of product repair guides, sewing tips, and even product care guides right here on iFixit. We’ve also worked with manufacturers to make guides and distribute parts, as well as to manufacture tools for them. Your imagination is the limit, chances are the repair community can help you get there.
What is the one thing all CEOs should know about the Right to Repair?
Repair won’t hurt you. Whether it seems like it or not, the Right to Repair will be a win for everyone—for the health of local businesses and the health of the planet, and yes, the bottom line. The Right to Repair is coming, make no mistake. Whether it’s national adoption of a repair bill, or EU labeling requirements, repairable is the future. There will likely be some growing pains as companies adjust to new requirements; that’s to be expected. But the world is ready for repair. Shareholders have pushed back, and behemoths like Microsoft and John Deere have blinked. Voters have overcome the spurious arguments of bad-faith lobbyists. And the world will be better for it.
The only question now is: will you lead the charge? Or be forever chasing the competition?
Sam Goldheart