Reverse Logistics Talk
By Jennifer Bilodeau, Independent Consulting
Historically, reverse logistics can be dated back throughout history where unwanted items would be reused or recycled into new items. Early settlers used whatever they had to make life easier such as the women who made quilts from old clothing and rags. Montgomery Wards, an American furniture shop, established in 1872 was the first company to have a 100% customer satisfaction or your money back guarantee (Liu, u.d., p.15).
World War II was plagued with shortages across the supply chain. The government created the first recycling program. “Economizing initiatives seemed endless as Americans were urged to conserve and recycle metal, paper, and rubber” (World War II Rationing, u.d., para. 11). The automotive industry was forced to recycle and reuse parts for vehicles as a direct result of the materials shortages associated with World War II.
The first major product recall involved the Ford Pinto in 1978. The designer, Lee Iacocca, wanted to build a competitive compact, low cost vehicle. There was a considerable safety risk that caused the gas tank to explode when there was a rear impact on the vehicle. Iacocca was known for saying “safety does not sell” (Casotti, et al, 2004, slide 9). Although the vehicle failed safety tests and a solution to prevent gas tanks from exploding was a one dollar piece of plastic to reinforce the bolts, it was rejected placing priority on reducing the weight and of the vehicle. Several law suits brought by victims and their families involving injury and wrongful death impacted the way the industry viewed safety, risk mitigation, and recall management improving accountability and communication throughout the supply chain.
Historically we can find many examples of re-use and recycling, however, it was not recognized as a reverse product or material flow until the 1970’s. Prior to the seventies reverse product flows was lumped with green or environmental logistics. Returns management continued to evolve recognizing the complexities of the reverse flow compared to that of forward flows (Bilodeau, 2013, para.2). Reverse logistics began to separate from forward logistics and was defined as “the process of planning, implementing, and controlling the efficient and cost effective flow of raw materials, in-process inventory, finished goods, and related information from the point of consumption to the point of origin for the purpose of recapturing value or proper disposal” (Rogers and Tibben-Lembke, 1998, p.2).
Reverse logistics continues to evolve improving transparency across the supply chain, efficiencies by reducing risk, cost, and environmental impacts across the supply chain by focusing on developing collaborative relationships.
Approaching Reverse Logistics
Defining reverse logistics has been an evolutionary process. The complexities associated with the reverse flow of goods extend into many operational areas within an organization that can significantly impact the forward flow of goods. “In a traditional supply chain, a non-optimized management process results in the production of less than optimal output, which leads to solid and hazardous waste, as well as additional operating costs throughout the supply chain” (Weeks, et al, 2010, p.1090). Operations managers often do not understand the full impact across the organization from waste reduction and recycling programs because it is often difficult to quantify returns on investment. Some of the cost savings are projected such as transport savings, reduced energy costs, and understanding other benefits from effective returns management decisions. A reverse logistics specialist can be dedicated to research and determine quality control, customer service, warranty repair, warehousing, or other financial implications throughout the returns process.
The Department of the Army launched a Reverse Logistics Process Action Team who was tasked with measuring velocity management (VM) and defining process methodologies for define, measure, and improve (DMI) initiatives (Banks, u.d., para 5). The initial progress was compared to skeet shooting, constantly aiming at a moving target. This is a fair assessment as the variables of reverse logistics are constantly changing whether they are associated costs, environmental regulations, or consumer demand.
The military defined the beginning of the reverse logistics cycle at the point of property turn in, however it was more difficult to define where the reverse cycle ends. Manufacturers and retailers face similar issues throughout the supply chain as they examine reutilization programs, repairs, maintenance, warrantee management, as well as many other aspects associated with the reverse flow of goods. The military faced a unique challenge that a private manufacturer should consider while negotiating terms of lease products. Government contractors often act as a third party furnishing equipment to perform specific tasks and whose costs may be absorbed by the government customer further complicating ownership, handling, and disposition issues at product end of life. At the end of the product lease, consider the financial implications of independent disposal, refurbishment, or resale of the used equipment. Some leased items may provide the most value having the vendor manage disposal and salvage, while other items might have after market value worth considering. When approaching reverse logistics, it is important to examine the organization and develop a plan to find the most cost effective way to manage and reduce returns.
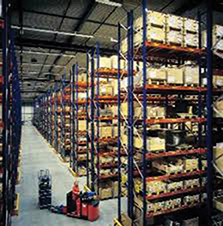
Product returns fall under many different categories making the approach to examining the issues an organizations faces much more challenging. Product returns can be for any reason making it important to capture this information to determine return trends for process improvements. Returns management should begin with a clear written policy that identified product life cycle, and what point is a consumer not eligible to return that merchandise. Without a clear guideline, there will be a point where the costs will outweigh the benefits. Consider how strategic communication of policies and collaboration will impact organizational efficiencies throughout the product life cycle.
When approaching a reverse logistics operation, it is beneficial to take the return one step back in the supply chain throughout the reverse flow to find the optimal point to reintroduce the product back into the forward supply chain. This process is used to recapture the most value. Products with short shelf lives such as seasonal merchandise or quickly changing technology rely of the speed decision making and expedited handling to reduce costs of managing the returns.
Cooperative Relationships Sharing Data
Larger organizations are beginning to understand the power of collaboration across the supply chain. Kellogg’s reduced the amount of unsaleables by 75% in an effort to not only reduce returns but increase profitability (Carolina Supply Chain Services, 2006, p.2). Before implementing any changes, two years had been spent collecting data. “Kellogg’s and Carolina Supply Chain Services (CSCS) developed a plan to collect data for Kellogg throughout the supply chain and at the customer, including warehouse, retail store, and reclamation centers” (Carolina Supply Chain Services, p.4). Identifying all critical points in the supply chain will help improve decision making processes.
A level of trust must be developed for collaboration to function as it is. It is important to institute cross divisional teams not only to keep them vested in the project, but to benefit from the way they interpret the data relevant to their division. “Kellogg’s and CSCS senior level managers worked together to fain knowledge about each other’s operating processes, including knowledge of CSCS’s complete audit processes and Kellogg’s processes and internal structures of the Kellogg’s organization” (Carolina Supply Chain Services, 2006, p.4). Examining various interpretations of data relevant to different areas across the organization both internal and external will help in the development of scorecards to measure decisions and opportunities to reduce returns.
Separate scorecards were developed by Kellogg’s addressing potential improvements in manufacturing, plants, and distribution as well as marketing, sales, and quality control. Tools were created to measure and identify improvements in manufacturing and defect free shipments. Older equipment was identified using the methodology that identified production error in the manufacture of the food. The scorecard approach was able to identify the profitability to replace or repair the older equipment. In a second area, Kellogg’s recognized “sweating” in the frozen food cases at the customer’s warehouse which weakened cardboard packaging and damaged product. In this situation, Kellogg’s was able to assist their customer by providing data that reflected optimal storage temperatures for better control and continued monitoring temperatures to assist their customers as an ongoing continuous improvement strategy. Multiple improvements were made in packaging and shipping from improvements to adhesive that was failing with routine retail handling, to secondary packaging that caused creasing the food containers as well as increased product exposure to the elements. When implementing improvements to packaging, a gold star was placed on the improved packaging to quickly identify and compare products during random audits in retail and warehouse locations. Marketing found the gold star promoting best quality packaging was a marketing tool to improve sales (Carolina Supply Chain Services, 2006, p.7-11).
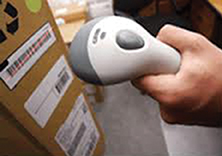
Wal-Mart implemented new policies in their procurement strategies to recapture values from returns and excess merchandise. If the manufacturer wants to reclaim merchandise, they must pay for costs associated with transport. If the manufacturer chooses to have Wal-Mart liquidate or dispose of their product, Wal-Mart keeps all profits earned and charges the manufacturer for disposition costs (Greve Davis, 2010, p 8). With increased customer demands, it is important to share and manage data.
Some of the challenges faced in the military has been an ongoing disconnect between various military inventory and financial databases. Different data collection systems provide different functions such as Unit Supply Logistics (ULL), Standard Army Maintenance Systems (SAMS), and Standard Army Retail Supply Systems (SARS). Although each system addresses inventory in different stages throughout the supply chain, they do not communicate with each other. “Disconnects in data management are further exacerbated by separate systems between quartermaster, ordinance, and transportation” (Banks, u.d.). With data manually moving from one information system to another, there is more room for error and created an inconsistency throughout the supply chain resulting in lost man hours, increased repair times, and increased operational costs. Other challenges surrounding data inconsistency issue is evident in the military’s Total Asset Visibility (TAV) which is designed to track RFID items as it moves from point to point throughout the shipping process. “The item is also entered into the Logistics Support Activity data center (LOGSA) which does not use RFID tag numbers, but document ID numbers creating confusion when trying to access records” (Banks, u.d.). Although there are instances where government supply chain processes may face issues of regulatory control, security concerns, or other operational issues that may justify multiple data sources, a private company with more flexibility in their supply chain would find rare situations where benefits of utilizing independent systems would outweigh potential cost savings.
Strategic data management planning and collaboration will help the organization to develop consistency throughout a complex returns process. Data collected might identify the reason for return is the inability for the customer to use the product. This information could be used to redesign the product, implement a toll free number to troubleshoot set up, or create a pictorial image of set up procedures to reduce the likelihood of the return. Ultimately, consistency in returns handling will expedite the reverse logistics flow, recapture more value, reduce returns handling costs, and improve customer satisfaction.
Data management will act as communication tool between manufacturer and retailer improving gate-keeping identifying the validity of the return and ensuring proper credit is issued as a result of the return. Without a system designed to act as a gatekeeper and help customer service representatives at the point of return to stay within established parameters, the costs could start exceeding the benefits. Many game manufacturers have offered on-line upgrades, free access to private social media communities and other added bonuses for the customer to register the product right away and create a cohesive inventory control system (Sims3 Login Community, u.d.). Establishing communication policies, no matter what the product may be, outlining the returns policy is setting expectations throughout the supply chain and significantly reduces the likelihood of a customer returning a product after the warrantee period has expired.
Data is critical in any organization because a manager cannot manage what is not measured and tracked. Good business decisions come from good data management. “Tracking data across all operations, where returns or recycling infrastructures may not be fully developed, allows for lessons learned” (General Motors News, 2012, p.3) and collaboration to improve material management in the reverse supply chain.
Automation Facilitating Communications
Data management and automation of processes will drive the management of returns developing a closed loop supply chain. It is important to identify what data should be collected, and limit decision making to those are in a position to see the big picture through data analysis, and provide tools to assist with gatekeeping of returns. Return policies and procedures are often confusing and not communicated outside the area which is directly involved with returns. It becomes more problematic across the supply, especially at the point of collection in retail outlets where employee turnover is traditionally high. When considering a strategic automated communication plan, many aspects should be considered identifying criteria associated with product quality, servicing instructions, transport costs, potential profit recovery, and potentially hazardous material risks. Additionally, data capture forms can bring improved and consistent reverse logistics operations by encouraging customers and service or repair representatives to capture why the product was returned. Identifying return trends for further analysis will be essential for continual process improvements.
Automation will help facilitate transparency in the supply chain, provide real time data for continual process improvements, and communicate information providing guidance across the supply chain when the information is needed. “Strategic communications should be developed to define rules, acceptable action, and decision points on whether to accept or reject the return” (Norman, 2007, para.6). The benefits of automated decision making are at the initial point of return. The ability to manage high turnover staff providing the tools to quickly and consistently assess the return and isolate the item for testing, repair, refurbishment, decommissioning, as well as ensure compliance with environmental laws. Well managed data and documentation collected will be the backbone of decision-making throughout the reverse logistics cycle. “An item is assigned a document number that remains with it until it reaches the reverse pipeline endpoint and leaves the system” (Diener, 2004). As the item takes one step back in the supply chain, a decision point can be communicated on how to manage that item. Information can be transmitted from the document numbers that will help develop consistency in how returns are managed.
img4
It is important communicate a sustainable culture not only to demonstrate commitment to reverse logistics and sustainable business models, but to engage employees and build a desired culture. This will reinforce the policies and procedures and help employees contribute to continuous process improvements to reduce waste and recapture value. Collaborating across divisions with employees has proven effective with General Motors (GM). “An employee identified an opportunity to reduce costs by utilizing recycled cardboard packaging into Buick Verano and Lacrosse headliners to provide acoustic padding that reduces noise in the passenger compartment” (General Motors News, 2012, p.4). Another employee initiative included “mixing plastic caps that protect vehicle parts during shipment with other post-consumer plastics like bottle caps to make air deflectors for Chevrolet Silverado and Sierra pickup trucks” (General Motors News, 2012, p.4)
The customer should be considered while implementing communication strategies that reflect consistency and clear communication throughout the supply chain. In one case study, an electronics manufacturer failed to quantify the weight of return management decisions that would impact that customer. The high tech electronics manufacturer decided that they wanted to send customers replacement items quickly, but did not trust their customers implementing fraud prevention without quantifying the impacts or likelihood of fraudulent returns. The manufacturer required a consumer to provide a credit card number to facilitate the return and the card would be credited if the damaged unit was returned within a specified period of time. This alienated customers who may have received the item as a gift, used a pre-paid credit card, or cash payments. Customers complained claiming they were not credited the charge when the item was returned and some were billed multiple times for the same return creating a poor customer experience. The company failed to conduct a risk analysis to determine the level of fraud they could expect, and failed to mitigate that risk by building the cost of the return in their pricing as a form of customer self-insurance. These were drastic measures for a fraud rate of less than 1% creating a “self-fulfilling prophesy where their customers distrust them as they distrust their customers” (Blumberg Advisory Group, 2013, para. 2-4).
Web based technologies will play a significant role, to facilitate communications. Each organization throughout the supply chain may use varying internal data management systems that are effective in their line of work. Creating a common, standard platform that can communicate information while customizing the data entry, business rules, or organizational needs will be essential to the success of managing returns and creating new opportunities to improve efficiencies. Data sharing across the supply chain can be used to keep supply chain partners working efficiently, controlling inventory, reducing excess or out of stock items, and more closely manage demands for promotional items ensuring products are available when the consumer needs them. Web-based technologies will help control unauthorized product returns as well as provide shipping and packing labels to ensure the return is managed and shipped correctly.
Retailers are facing new challenges with returns. Lawsuits against retailers for hazardous material handling violations have included claims of improper storage, transportation, and disposal of bleach, paint, pesticides, batteries, light bulbs, and other products that may contain hazardous materials. While the forward supply chain, any company handling hazardous material is required to have designated HAZMAT personnel who have training and are qualified to classify, package, mark, and shop hazardous materials. In the reverse flow, returns are more complex and it can become costly and problematic to train personnel in in hazardous material handling due to high employee turnover. When it comes to returns and the reverse logistics process, retailers and consumers may be mishandling returns containing hazardous materials unknowingly. Web based technologies providing real time assessment, shipping, and handling instructions to the customer or retailer providing proper handling instructions will help mitigate these risks.
Many industries are looking to outsource returns management activities which are placing a higher demand for web-based solutions that will span multiple organizations across the supply chain, multiple time zones, and multiple work shifts to provide information on demand. “Nearly 70% of telecom and utility companies currently outsource repair/refurbishment functions with 44% who rely on partners for asset recovery functions” (Norman, 2007, para. 19-20).
Integrated solutions will help organizations to adopt collaborative communications technologies that will drive decision-making processes and consistency throughout the supply chain. Value can be extracted from reverse logistics processes by optimizing, tracking, and reconciliation inventory while providing decision-making support features. Cloud computing is beginning to evolve within reverse logistics providing manufacturers, and logistics service providers delivering their goods, better control and visibility of returned or refused products with ease in a collaborative system. These systems are designed to facilitate efficiency in collaboration and communication “complimenting SAP, Epicor, Infor, Unit 4, Microsoft Dynamics, and Warehouse/Transportation Management Systems” (Percepetant, 2010). The cloud communicates internal data externally with more ease. A partner in the supply chain is not faced with delays of their partner supplying reports, working with the data to integrate it into their systems, or manually analyzing those reports to capture the information they need. This type of collaboration will maximize service levels as well as identify potential risks that would warrant product improvements or redesign.
To be continued …..
REFERENCES
Amini, M., Retzlaffroberts, D., & Bienstock, C. (2005). Designing a reverse logistics operation for short cycle time repair services. International Journal of Production Economics, 96(3), 367-380. doi: 10.1016/j.ijpe.2004.05.010
Banks, R. (n.d.). Defining and improving reverse logistics. Retrieved fromhttp://www.almc.army.mil/alog/issues/MayJun02/MS745.htm
Bilodeau, J. (2013, May 24). Reverse logistics vs. green logistics: Is there a difference? Reverse Logistics Talk. Retrieved May 26, 2013, fromhttp://reverselogisticstalk.wordpress.com/
Burgess, W., & Stevens, C. (2010). Reducing environmental impact of returns. In Canadian Encyclopedia of Environmental Law. Retrieved June 17, 2013, fromhttp://www.returntrax.com/site/ywd_returntrax/assets/pdf/RTX_Environmental_White_Paper.pdf
The business case for zero waste [PDF]. (2012, October 19). Detroit: General Motors News.
Carolina Supply Chain Services, Inc. (2006). A closed loop returns management system: Turning failures into profits [Brochure]. Winston-Salem, NC: Author.
Casotti, L., N., & Lindaman, J. (2004, Fall). Ford pinto case study. Retrieved May 26, 2013, from www.cofc.edu/~blocksonl/…/Ch.%2012%20-%20Ford%20Pinto.ppt
Creating the optimal supply chain. (n.d.). Boston Consulting Group. Retrieved June 27, 2013, fromhttp://knowledge.wharton.upenn.edu/papers/download/BCGSupplyChainReport.pdf
Diener, D. (2004). Measuring the reverse logistics process. In Value recovery from the reverse logistics pipeline. Santa Monica: Rand.
Excel. (n.d.). Collaboration drives waste to zero [Brochure]. Author. Retrieved June 13, 2013, from http://www.exel.com/exel/exel_customer_successes.jsp?page=1
Field, J. M., & Sroufe, R. P. (2007). The use of recycled materials in manufacturing: Implications for the supply chain management and operations strategy. International Journal of Production Research, 45(18/19), 4439-4463. doi: 10.1080/00207540701440287 (EBSCO)
Foroohar, R. (2013, April 11). How ‘Made in the USA’ is Making a Comeback. Business Money How Made in the USA Is Making a Comeback Comments. Retrieved June 08, 2013, from http://business.time.com/2013/04/11/how-made-in-the-usa-is-making-a-comeback/
Greve, C., & Davis, J. (n.d.). Recovering lost profits by improving reverse logistics (Tech.). UPS.
Greve Davis. (n.d.). Future trends that will impact reclamation [Brochure]. Author. Retrieved June 8, 2013, fromhttp://grevedavis.com/files/2010/09/Future%20Trends%20in%20Reverse%20Logistics%20Sept%202010.pdf
Iles, J. (n.d.). Re-thinking progress: The circular economy. TED-Ed. Retrieved June 01, 2013, from http://ed.ted.com/on/2Yy019iv
InformationWeek: The Business Value of Technology. (2001, December 10).Informationweek. Retrieved June 08, 2013, fromhttp://www.informationweek.com/companies-reconsider-offshore-outsourcin/6508358
Konrad, T. (2012, October 01). New Trends in Reverse Logistics – Tim Konrad [Interview by B. Bowman]. Retrieved May 26, 2013, from http://www.youtube.com/watch?v=UQIXxrfd90w
Liu, F. (n.d.). Reverse logistics matters: Impact of resource commitment on reverse logistics and customer loyalty (Unpublished master’s thesis). University of Maastricht. Retrieved May 26, 2013, from http://arno.unimaas.nl/show.cgi?fid=11285
Login – Community – The Sims 3. (n.d.). Login – Community – The Sims 3. Retrieved June 26, 2013, from https://www.thesims3.com/webLogin.html?redirectTo=http://www.thesims3.com/registeragame.html&forceLoginMessage=login.force
Norman, L. (2007, May/June). Five Considerations for Evaluating Returns Software Solutions. Reverse Logistics Magazine -. Retrieved June 02, 2013, fromhttp://www.rlmagazine.com/edition06p29.php
Reverse Logistics Today Blog. (2013, May 14). Reverse Logistics. Retrieved June 08, 2013, from http://www.blumberg-advisor.com/reverse-logistics-today/?Tag=Reverse%20Logistics
Roach-Patridge, A. (2011, June). Full circle: Reverse logistics keeps products green to the end. - Inbound Logistics. Retrieved June 15, 2013, fromhttp://www.inboundlogistics.com/cms/article/full-circle-reverse-logistics-keeps-products-green-to-the-end/
Rogers, D. S., & Tibben-Lembke, R. S. (1999). Going backwards: Reverse logistics trends and practices. Reno, NV: University of Nevada, Reno, Center for Logistics Management.
Shaughnessy, L. (2012, May 22). Probe finds ‘flood’ of fake military parts from China in U.S. equipment. CNN Security Clearance RSS. Retrieved December 26, 2012, fromhttp://security.blogs.cnn.com/2012/05/22/probe-finds-flood-of-fake-military-parts-from-china-in-u-s-equipment/
The Springville Museum Quilt Show. (n.d.). The Springville Museum Quilt Show. Retrieved May 26, 2013, from http://www.americaslibrary.gov/es/ut/es_ut_quilt_1.html
Weeks, K., Gao, H., Alidaeec, B., & Rana, D. S. (2010). An empirical study of impacts of production mix, product route efficiencies on operations performance and profitability: A reverse logistics approach. International Journal of Production Research, 48(4), 1087-1104. Retrieved May 29, 2013, from EBSCO.
World War II Rationing. (n.d.). World War II Rationing. Retrieved May 26, 2013, fromhttp://www.u-s-history.com/pages/h1674.html
Jennifer BilodeauJennifer Bilodeau, a Reverse Logistics specialist, formerly supported the Department of the Defense in day to day management of both inbound (return) and outbound distribution of goods throughout the command. She was recognized for exemplary performance throughout the base relocation effort working with internal/external stakeholders managing multiple projects assessing tangible goods for movement to new facilities, acquiring replacement items, as well as recapturing value from left behind products. In this role she oversaw reverse logistics operations including repair and warrantees, secondary markets, deconstruction and re-utilization of parts, as well as final disposition instructions.