Bold Work-Out
By Rob Bromley, Lenovo
Lenovo is engaging teams in dramatic, rapid improvements beyond traditional continuous improvement with a focus on reverse logistics at its National Returns Center
Lenovo, the world’s leading computer manufacturer, is redefining the reverse logistics process for its North American region. The company’s Returns, Refurbishment and Repair operation, part of the National Returns Center (NRC) in Whitsett, NC, is leveraging complex reverse logistics processes into a multi-million dollar asset recovery. Lenovo has implemented creative and innovative process improvements in Whitsett to establish the model for Lenovo Returns Centers worldwide. Lenovo uses resources around the world to ensure a successful returns process that is scalable for the demands of today and for future business opportunities.
As a consumer do you ever think about that product you opened, reconsidered and then returned to the store, after you have your refund in hand? Are you just happy to have your money back and ready to buy something else? Did you assume the store clerk puts it back on the shelf and voila, it’s ready for the next customer to buy? Easy, right? No big deal...life goes on for everyone. Well, those of us in the returns business know that it’s just not that easy!
With Lenovo’s rising market share in North America and its tremendous success in the Retail sector, its NRC operation has experienced significant growth over the past three years. The NRC team is four times the size it was just three years ago. Return volumes are up year over year in line with the total volume of sales. Statistics show return rates are better but with the boom in sales come higher volumes for the NRC team.
So it just goes back in the racks like you thought, right? What’s the challenge in that?
The challenges, as is common in the returns business, are many and complex due to multiple customer channels, products and returns processes.
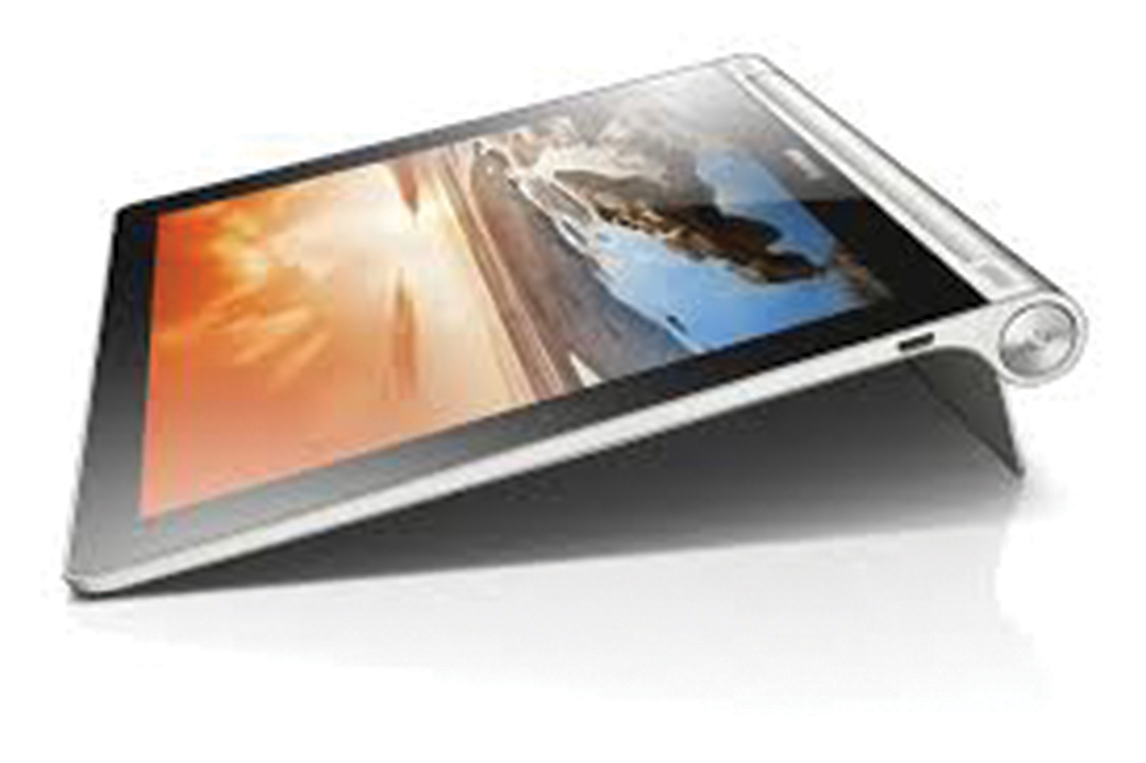
Lenovo’s NRC has established high level operational metrics to guide the team and help measure the success of the returns operation in meeting Lenovo’s overall business objectives. There are three key operational metrics for its NRC team:
1) Cycle Time: Dock to Stock
2) Quality: Refurbished product to internal and external quality measurements
3) Efficiency: Cost
While there are other metrics that Lenovo tracks for the NRC Operation, these three key metrics drive the operation day to day. Lenovo’s North America inventory team tracks metrics related to the age and value of inventory returned to the NRC. Lenovo’s sales teams track available inventory for re-sale in a number of channels. At the end of the day, if the NRC team executes on its three key operational metrics, the other Lenovo teams, such as Inventory, Excess and Obsolete Management are assured to get the results they need to be successful.
Now imagine that product you returned and its journey to find a new consumer. After it goes back to the store clerk it’s joined at the store with other returned products. The store contacts Lenovo to request a Return Authorization (RA) for those products. Once enough returns have accumulated, they’ll be sent to the retailer’s distribution center or to a third party returns management company. After all returns have been collected they’ll be organized by RA and sent back to the NRC in Whitsett, North Carolina.
When the products arrive they are received, credit processed, placed into inventory, refurbished and/or repaired and then listed in appropriate sellable condition, i.e. redistributed, refurbished, scratch and dent, etc. Lenovo then advertises on the Web to find new consumer homes for units that were supposed to just “go back on the shelf”.
So there you have it, a bit longer journey for that returned product. A little more involved than you may have thought but ultimately the Lenovo NRC team has been successful in getting a new consumer home for returned products and realizing the benefit to Lenovo in the process.
In 2013, Lenovo’s Americas Group President Gerry Smith asked, “How do you go from good to great?”
The NRC team decided to utilize Lenovo’s Lean Six Sigma (LSS) culture, believing this would provide solid improvements and yield 10%+ process improvement.
Where did the team start with LSS?
• Forecasted product output for better Sales visibility - done via a production control model for the returns inventory to help plan and anticipate what will be available to the Sales and Outlet teams. Operations are now flexible enough to handle all products that Lenovo sells in North America, with no restrictions on what can be returned, refurbished and re-sold.
• Inventory value reduction - achieved through planning and priority setting to focus on the reduction of excess and obsolete inventory first, with significant wins already realized.
• Improving yield through Refurb & Repair Operations – accomplished through multiple LSS projects which enhanced the operation and increased the yield of higher valued finished goods.
Like many successful businesses, Lenovo leveraged Lean Six Sigma and LSS tools to enable modest improvements in its Reverse Logistics Operations. Successes since 2008 include:
• Creating Lenovo proprietary Shop Floor Control systems
• Creating operation flexibility to handle all brands, models and platforms of products
• Creating universal packaging to support multiple platforms and models
• Creating alternate work schedules to implement a seven day per week operation, in lieu of adding space or equipment costs
• Creating in-house Test capabilities for refurbishment of all systems
• Creating multiple re-sale vehicles (Web, Lots, Brokerage and Retail)
Lenovo’s NRC team ultimately was successful, but the level of success was just….good. What is the answer to be GREAT? The NRC answer was…. BOLD WORK OUT!
Lenovo implemented a new evolution to continuous improvement by engaging cross-functional teams in a new event called Bold Work Out. Lenovo’s Bold Work Out name takes its roots from GE’s Work Out program that developed by Jack Welch in the early 1990s. The program, based in LSS, is composed of several speed driven steps that take improvement to aggressive goals within ninety days of start of the event. Lenovo’s desire to implement a “Bold” version of Work Out in its NRC began in September 2013 and successfully concluded that December with a BOLD celebration.
Bold Work Out has been successful across several of Lenovo’s in-house factories in Mexico, China, Brazil and the U.S.--most recently with the new U.S. Assembly Operation also located in Whitsett, North Carolina.
Bold Work Out has six guiding principles:
• Executive Support - Direct Involvement
• Expert Guidance - Champion support and guidance
• Talent and Skill Development - Specific skills developed
• Team Engagement - Involvement at All Levels
• Complete cooperation - Guaranteed success
• Bold Targets - Aggressive results
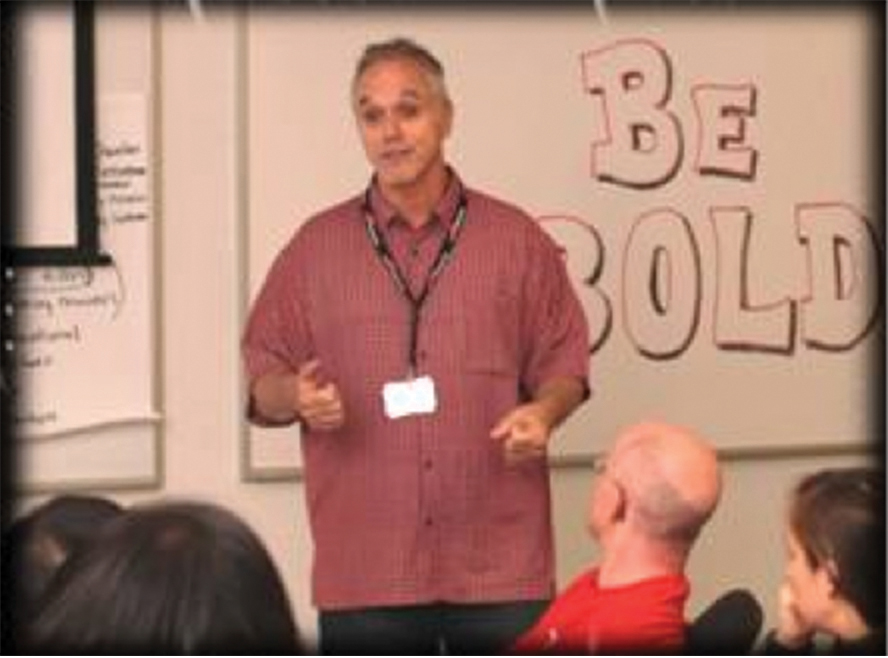
“Together we do more!” explains Mario Bofill, Western Operations LSS Black Belt for Lenovo, as he kicks off another Bold Event. Bofill explains, “A consistent message that I hear from teams is, ‘This isn’t easy”. Bofill continues, “Trust the process you are executing” “Believe in yourself that you can do the activities” and “Believe in your team for together you will achieve your goals”. Successful completion of Bold Events in multiple Lenovo locations worldwide provides confidence in the program.
Bold delivers success through three key strengths: Engagement, Speed and Execution.
Engagement
• Where leadership engagement & empowerment is required
• Where an issue impacts people from many functional areas at many levels
• Where there are multiple opportunities for improvement
• Where a forum for dialogue and change builds systemic thinking and breaks down organizational boundaries
Speed
• Where you get, or need to get, results quickly
• Where changes can take place within three months
• Where “on the spot” decision making is required
• Where concentrated time and the pressure of a deadline gets rapid results
Execution
• Where results exceed our normal incremental approach
• Where gaps can be closed through addressing issues that stand in the way of meeting goals
• When needing to identify the “right things” to go work on – and then doing it
• Where concentrated decision making and empowerment is needed to resolve issues – with clear lines of accountability for actions
The benefits of Bold Work Out include:
• Increased speed and quality of decision making & results
• Gives a ”voice” to all colleagues
• Teams cut across barriers of functions, organization & hierarchy
• Creates passionate ownership for results by the team
• Drives innovation & BOLD change
Typical continuous improvement events such as Kaizen, Quality Circles and LSS focus on improvements and stretch goal opportunity.
With Bold Work Out, “We do more”!
So how did the NRC team do with its new Bold Work-Out program?
The NRC team divided into three teams of BOLD team colleagues. The first team included the Refurb Rock Stars who focused on improved efficiency of Refurbishment. The second team, known as the Cycle Time Assassins, focused on cycle time reductions. The third team, called Nucleus 10 (10 members strong), jumped in to quality improvements.
To ensure the main event Bold would be successful, several days before the smaller team of facilitators, team leaders and specialists worked through a two day target setting session.
The first day of target setting, Tony Pulice, Site Director; Mark Kerr, Senior Manager and Rob Bromley, Functional Manager, all addressed the team and expressed strong support for the coming sessions and future Bold Work Out event.
Bold Facilitator, Mario Bofill and NRC’s Engineering and Quality Manager, Will Lawrence, continued the message of “Be Comfortable being Uncomfortable”. They helped facilitate the discussion the first day which resulted in 150 ideas for improvement!
The second day, the NRC Team established the initial Bold Targets and direction. This group would then help lead the extended Bold Work Out teams to achieve 30, 60 and the final 90 day targets!
The teams presented their Bold plans to Muzzi Palmieri, Lenovo’s Western Operations Executive Director. He provided great support and encouragement to the team as well as extending the challenge to go even more Bold with their targets!
So now it was time for the big event and so with additional cross-functional team colleagues joining the teams Day 1 of the event was starting. With Senior leadership represented by Muzzi, Tony and Mark helping kick off the WOW, all gave inspirational words and shared their energy with the teams. Focus and energy and the feeling of being uncomfortable were really present as there were huge targets and so much to learn and know in the coming days. The senior leadership agreed to cooperation and to help in breaking down any barriers that would block the ability for the teams to achieve success.
Mario Bofill stepped in and acknowledged the strong work the leaders, facilitators and specialists had put in to this point. The NRC’s senior Manager, Mark Kerr noted that he had “goose bumps” from the energy he was feeling. “Wow” was the overriding theme of the first day as support, direction and expectations were created for the Bold Work Out team.
So the teams probably went home full of ideas, fears, but also enthusiasm which made sleep a little difficult. Day two of the Bold Work Out starts and movement was obvious out of the gate with the team activity. The three teams began to measure and define how their ideas would improve their process. The focus was on automation, environmental components and more creative ideas. The teams were able to advance forward by quantifying and categorizing the ideas for their 30, 60 and 90 day targets.
img4
And then there was Muzzi….”I challenge you to be even Bolder!”
Day three the momentum was at warp speed! The teams took Muzzi’s challenge of “being bold” and identified more ideas to improve the process. The total number of ideas jumped from 150 to 657. The teams had truly embraced bold and the commitment to “WOW” was obvious by from the demonstrated excitement, passion and ownership.
Team colleagues shared their ideas with their peer groups out in the Returns Center still working on the Returns, Refurb and Repair operations. The excitement was shared and the unknowns of what was being committed by the Bold team explained to the extended teams. Now the “WOW” was taking form and the stir on the floor also was generating more ideas!
The final day of the Bold Work Out event, the teams presented their ideas to the leadership team. Joining Tony Pulice, Muzzi Palmeiri and Mark Kerr was Kim Davis, Lenovo’s Executive Director of Fulfillment. This would be her first exposure to the NRC’s Bold Work Out. The teams presented their progress, ideas and the expected improvements to support their bold targets.
Were the ideas approved? Would the team get the senior leadership support?
Tony Pulice, Plant Manager, gave the thumbs up, Kim was very pleased and Muzzi exploded “Heck Yeah!”
Lenovo’s National Return Center was BOLD! The Dock to Stock cycle time journey was improved by more than 5 times! WOW! The refurbishment operation improved efficiency in that process by 100%. Finally, the Quality team improved product quality by 147%. BOLD!
So think again about that product you returned now. Look at the journey and experience the Lenovo team has put in to ensuring this unit gets “put back on the shelf”.
Leader Testimonial
My Bold Work-Out experience is one that I would call nothing short of amazing, as a certified Lenovo Lean Six Sigma Professional (Certified Black Belt from North Caroline State University)with over 10 years experience. I am currently the Western Operations Lean Six Sigma Manager responsible for Lean initiatives within our Monterrey Mexico, Itu Brazil and Whitsett NC plants (which comprises from training to Bold Work-Out events).
This past year I was tasked with implementing Bold Work-out within our region (which has been very successful within our China facilities). And I have to be honest; my first impression of Bold W-O was “just another rebranded Kaizen effort”. As I’ve done Kaizen events and the results were pretty much always the same results. You get people in a room for 3 – 5 days, then you schedule a meeting with the sponsoring leader, then you implement with minimal monitoring. Compounded with the fact of achieving targets of 100% or greater with plant colleagues leading the effort… as an engineer the concept seemed irrational.
Well I couldn’t have been more wrong about Bold Work-Out. The methodology of management allowing plant colleagues to “take control” of a process, then presenting of ideas to management for approval is well “Bold!” My experience as the Bold champion is one of complete astonishment , I witness plant colleagues “grow” as they are given a “voice” to express their thoughts and ideas on how a process should be defined (not as the engineer defines the process). And management becomes a “sponsor” and a receptor of ideas and at the end both groups become “one” with a single voice and message. The truly remarkable thing is that now the plant culture has been changed “forever”, you now have colleagues that now have a voice and are not bashful about coming up with new ideas or asking of when is the next event. This is truly an amazing transformation to lead and witness and I look forward to the next event……….
Colleague Testimonial #1
The BOLD workout has been an exciting experience for the receiving and refurb operations here at Lenovo’s USFC. We have identified many opportunities to enhance efficiency, quality and overall customer service in a short timeframe and with a relatively small financial outlay.
I came to Lenovo seven months ago, during the company’s expansion to a multi-shift operation in their Refurb/Repair department. With my past experience in small lot manufacturing and production inventory planning, I expected to quickly understand the processes at the National Return Center. I quickly realized that Reverse Logistics was a completely different creature than the supply chain with which I was familiar. I jumped at the chance to learn the processes better by participating in the BOLD Workout.
For the Workout, management had identified three major improvement focus areas - received goods processing, refurbishment and overall process quality - and a team was created for each area. Non-management colleagues were chosen to lead each group, and were given initial training in goal setting, communication, team motivation and business case creation.
The Workout teams were chosen from colleagues throughout the NRC, including floor workers, team leads and test engineers. These teams were blended with people from all shifts and departments to enhance site-wide collaboration.
The success of the BOLD Workout depended primarily on eliciting process enhancement ideas and commitment from all of the colleagues in the NRC. This was achieved by management’s encouragement of “no holds barred” idea brainstorming, quick test case implementation approval, and expedited financial backing based on ROI projections presented to them by the teams.
To me, the greatest benefit of the BOLD Workout has been the greatly enhanced communication and teamwork between all shifts and departments. With common goals, created and agreed upon by the employees themselves, there is energy and engagement that cannot easily be measured by financial analysis or reports. However, it can be seen every day in the quality and pride in our work, and a commitment to the Lenovo DO mentality.
Colleague Testimonial #2
“BOLD WORKOUT was eye-opening career experience as well as personally enriching. It was entirely about building, developing and applying more effective leadership skills; not just in terms of the more commonly thought of team model, but self-leadership as well... Better self-awareness has led me to more effective decisions and responses based on valid, purposeful objectives versus emotion or pre-programmed thinking. Consequently, I am able to be more aware of the moment and adapt my leadership style accordingly.
The BOLD WORKOUT are much more than “motivational seminars”. BOLD is indeed a profound and inspiring experience for anyone truly interested in effective personal and professional leadership development.”
Colleague Testimonial #3
After attending my first “Bold Work Out” two words come to mind, teamwork and motivation. I choose these two words to describe it because of the sheer amount of anxiety and feeling of being overwhelmed
when you first set your goals. With that being said the only way you push through it is by motivating each other as a team. Each one of your team members bring a unique view and skill to the table and by motivating each other’s ideas we were able to come together with many big and “BOLD” ideas. Overall with the conclusion of the Bold Work Out not only did I leave this experience with new ideas, but with new appreciation for my team.
This article submission on behalf of Lenovo is an exclusive story for the Reverse Logistics Magazine.
Rob BromleyRob Bromley
Operations Manager
Lenovo National Returns Center since January 2011
Bromley has 12 years of progressively responsible roles in Manufacturing Management with Tier 1 and 2 Automotive Component Suppliers. I have 5 years of operations leadership with Dell Computers and 3 years of Reverse Logistics Leadership with Lenovo Computers.
Bromley has LSS experience, Quality Circle Training and Kaizen Event training and facilitation. Bromley is from Statesville, North Carolina and a graduate from Appalachian State University with a BSBA degree in Business Management. Bromley lives in Burlington, NC with his wife and 5 children.